最新ニュース
- 2025年における日本の機械加工業界への影響
- アロジンコーティング:欠かせない表面処理技術
- アームス ブロンズ
- 紫外線 塗料
- 重金属トップ10のランキング:特性、影響、利用法
- ステンレス鋼の切削における加工硬化を防ぐ方法
- へら 絞り 加工 と は
- チタン鋳造とは: プロセス、用途、温度、価格
- プロトタイプ射出成形: 究極のガイド
- LEDライト部品 ダイカストサービス
- カスタムメカニカルキーボードはなぜ人気なのか?
- CNC加工サービスによるCCTV機器アクセサリー不足の解消
- カスタムバイクのパーツを近くで入手する方法
- CNC加工が精密部品業界を変える
- 複雑な部品の精密加工時の注意点
- CNC機械加工会社とは?
- 2022年 中国におけるCNC工作機械の開発動向
- アルミニウム高速加工ガイドの決定版
- CNC加工用工具と送り装置の選び方
- CNC機械加工部品の材料選択時の考慮点
板金 加工・クイック 板金・板金 工場
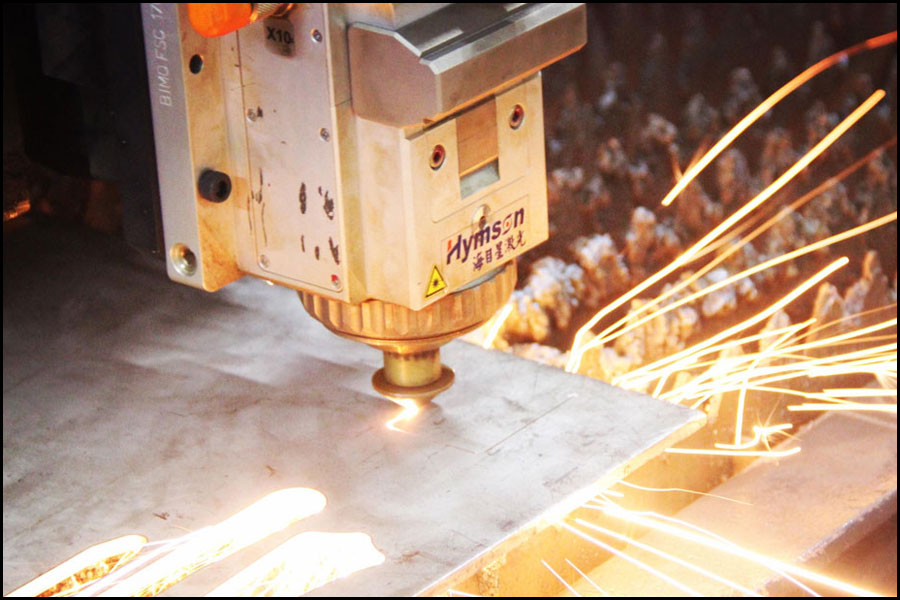
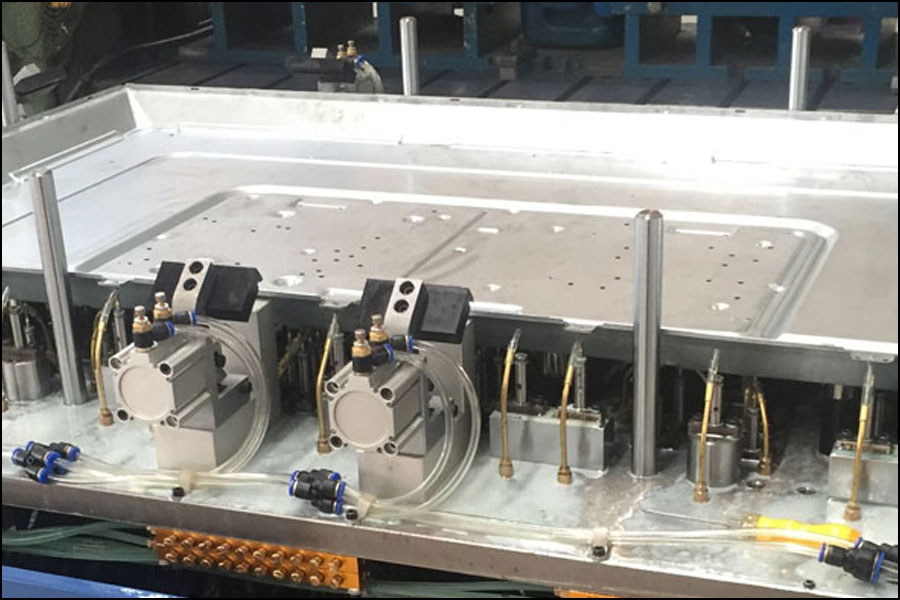
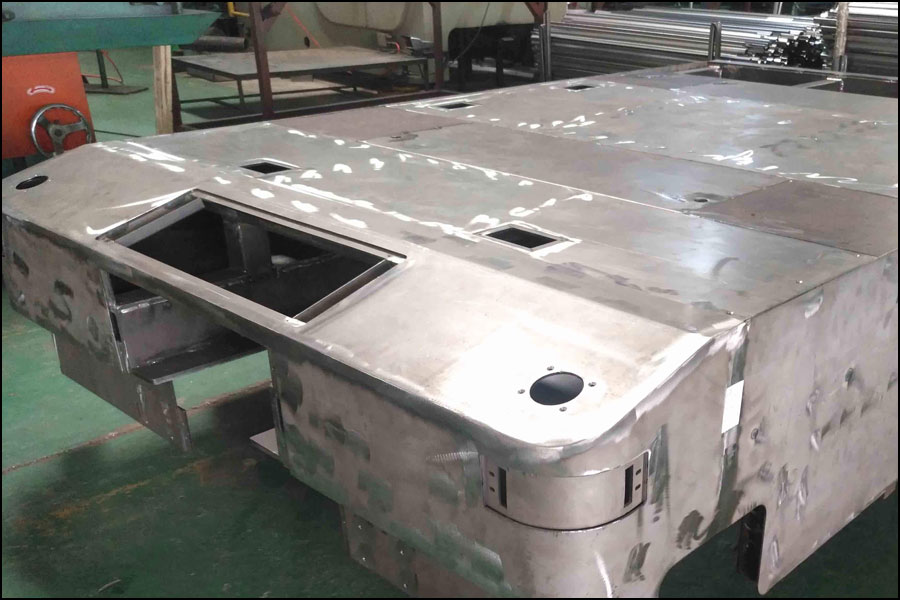
PTJを選択すると、プロジェクトのマテリアルの可用性とタイムリーな配信に自信を持たせることができ、ビジネスの運用の継続性を提供するのに役立ちます。
PTJシートメタルサプライは、剪断、スリッティング、リコイルから複雑で正確なルーターの切断まで、高品質の処理能力を提供することをお約束します。
大規模プロジェクトでの豊富な経験を持つ当社は、供給の継続性と、設計から完成まで継続的なコミュニケーションが成功に不可欠であることを理解しています。お客様との緊密なコラボレーションは、大規模で複雑なプロジェクトの要件を満たすための鍵です。設計、処理、量、またはスケジュールの変更に迅速に対応できる柔軟性により、パーソナライズされたサービスを提供し、お客様のニーズを満たすリソースと機能を備えています。
PTJの品質プロセスの不可欠な部分は、テスト証明書が利用可能であり、必要な基準に準拠していることを確認することです。すべての製品はオーストラリアの基準に準拠しており、ISO 9001品質管理システム認定を取得しています。
品質への取り組みに裏打ちされた当社は、ISO 9001品質管理システムの認定を通じてコンプライアンスリスクの削減を支援し、お客様のビジネスを保証します。
提供される産業
- インフラ
- 防衛
- 再生可能エネルギー
- エンジニアリングと建設
- 鉱業、石油、ガス
- 一般的な製造
- 輸送および自動車
- 住宅および商業ビル
- 農業と農業
板金サプライでは、次のような幅広い製品群を誇っています。
- 自動車用鋼
- 冷間圧延帯鋼
- 熱間圧延鋼
- メタリックコーティングされ
- たストリップスチール
- 塗装済みストリップ鋼
- プレート鋼
- 熱間圧延コイル
- 冷間圧延コイル
加工技術である板金は、まだ板金の比較的完全な定義を持っていません。 外国の専門誌の定義によれば、次のように定義できます。板金は、板金(通常6 mm未満)の包括的な冷間加工プロセスであり、せん断、パンチング/カット/コンパウンディング、折り曲げ、リベット留め、スプライシング、 フォーミング(車体等)等 その注目すべき特徴は、同じ部品の同じ厚さです。
板金は、軽量、高強度、導電性(電磁波シールドに使用可能)、低コスト、量産性に優れ、電子機器、通信、自動車、医療機器など幅広い分野で使用されています。 コンピュータケース、携帯電話、MP3では、板金は不可欠な部品です。 板金の用途がますます広まるにつれて、板金部品の設計は製品開発プロセスの非常に重要な部分になりました。設計された板金が製品の要件を満たすように、機械エンジニアは板金部品の設計スキルに熟練している必要があります。 機能と外観の要件により、スタンピングダイの製造をシンプルかつ低コストにすることができます。
プレス加工に適した板金材料は多数ありますが、電子・電気業界で広く使用されている板金材料には以下のものがあります。
- 通常の冷間圧延板SPCC SPCCは、冷間圧延機を介して鋼塊を鋼コイルまたは必要な厚さのシートに連続圧延することを指します。 SPCCの表面には保護がありません。特に湿気の多い環境では、空気にさらされると容易に酸化され、酸化速度が加速され、濃い赤錆が現れます。使用する場合は、表面を塗装、電気めっき、またはその他の保護する必要があります。
- 亜鉛めっき鋼板SECC / SECCの基材は通常の冷間圧延鋼コイルで、連続電気亜鉛めっき製造ラインでの脱脂、酸洗、電気めっき、およびさまざまな後処理プロセスの後に電気亜鉛めっき製品になります。 SECCは、一般的な冷間圧延鋼板の機械的特性と同様の加工性だけでなく、優れた耐食性と装飾的な外観も備えています。それは非常に競争が激しく、電子製品、家電製品、家具の市場で交換可能です。たとえば、SECCはコンピューターのケースで一般的に使用されます。
- 溶融亜鉛めっき鋼板SGCC溶融亜鉛めっき鋼コイルとは、熱間圧延および酸洗または冷間圧延を行った後、洗浄および焼きなましを行った後、約460°Cの温度の溶融亜鉛浴に浸漬して鋼板に亜鉛めっきを施す半製品です。その後、層は焼き戻し、平坦化、化学処理されます。 SGCC材料はSECC材料よりも硬く、延性が低く(深絞り設計を避けます)、亜鉛層が厚く、電気溶接性が劣ります。
- ステンレス鋼は、SUS301 Cr(クロム)の含有量がSUS304に比べて少なく、耐食性は劣りますが、冷間加工後の引張力と硬度が得られ、弾力性も良好です。主に破片ばねやEMI対策に使用されます。
- ステンレス鋼SUS304は、最も広く使用されているステンレス鋼の1つです。Ni(ニッケル)を含むため、Cr(クロム)鋼よりも耐食性と耐熱性に優れています。機械的特性が非常に高く、熱処理硬化現象がなく、弾性がありません。
一般的に言って、板金プロセスの基本的な機器には、シャーリングマシン(Shear Machine)、CNCパンチングマシン(CNC Punching Machine)/レーザー、プラズマ、ウォータージェット切断機(Cutting Machine)、ベンディングマシン(Bending Machine)、ドリルマシン、および次のようなさまざまな補助機器が含まれます:機械、レベリング機、バリ取り機、スポット溶接機など
一般に、板金加工の最も重要な4つのステップは、せん断、パンチ/カット、折り曲げ/圧延、溶接、表面処理などです。
板金は、金属板として使用される場合があります。一般的に、一部の金属板は、手作業またはダイスタンピングによって塑性変形して目的の形状とサイズを形成し、さらに溶接または少量の機械加工により、次のようなより複雑な部品を形成できます。家庭で一般的に使用されている煙突、鉄製のストーブ、車の殻はすべて板金部品です。
板金加工は板金加工と呼ばれます。具体的には、例えば、プレートを使用して煙突、鉄製バレル、燃料タンク、オイルタンク、換気パイプ、エルボ、エルボ、四角、漏斗などを作成します。主なプロセスは、せん断、曲げ、曲げ、成形、溶接、リベット留めなどです。特定の幾何学的知識。
シートメタルパーツは、薄い金属パーツ、つまり、スタンピング、曲げ、ストレッチなどの方法で処理できるパーツです。一般的な定義は、
加工時の厚みが一定の部品。例えば、鋳造部品、鍛造部品、機械加工部品などに対応し、車の外鉄シェルは板金、ステンレス製の調理器具も板金です。
最新のシートメタル技術には、フィラメントパワーワインディング、レーザーカット、重加工、メタルボンディング、メタルドローイング、プラズマカット、精密溶接、ロール成形、シートメタル曲げ、ダイ鍛造、ウォータージェットカット、精密溶接などがあります。 。
板金部品の表面処理は、部品の錆びを防ぎ、製品の美観を美化する機能を備えているため、板金加工工程において非常に重要な役割を果たします。板金部品の表面前処理は、主に油、酸化スケール、錆などを除去するためのものです。表面後処理に備えて、後処理は主にスプレー(ベーキング)塗料、プラスチックスプレー、防錆コーティングです。
3Dソフトウェアでは、SolidWorks、UG、Pro / E、SolidEdge、TopSolid、CATIAなどすべてにシートメタルパーツがあり、主に3Dグラフィックスを編集して、シートメタル処理に必要なデータ(展開された図面、曲げなど)を取得します。ラインなど)、CNCパンチングマシン(CNC Punching Machine)/レーザー、プラズマ、ウォータージェット切断機(Laser,Plasma,Waterjet Cutting Machine)/複合機(Combination Machine)、CNC曲げ機(CNC Bending Machine)のデータを提供します。
製品の機能と外観の要件を満たすために、板金の設計は、簡単なスタンピングプロセス、簡単なスタンピング金型製造、高品質の板金スタンピング、および安定した寸法を保証する必要があります。板金設計ガイドラインの詳細は、機械工業出版社発行の「部品構造設計加工性」「製造・組立時の製品設計ガイドライン」をご覧ください。
図面が用意できたら、展開されたさまざまな図面やバッチに応じて、レーザー、CNCパンチング、シャーリング、モールドなどを含むさまざまなブランキング方法を選択し、図面に従って対応する展開を行います。 CNCパンチングマシンは、工具の影響を受けます。特殊形状のワークや異形穴の加工では、エッジに大きなバリが発生します。後のバリ取り加工を行う必要があり、ワークの精度にある程度の影響があります。レーザー加工には工具がありません絞り、平面、特殊形状ワークの加工に適していますが、小さいワークの加工には時間がかかります。 CNCとレーザーの隣に作業台を置きます。これは、処理のためにシートを機械に置いて、ボードを持ち上げる作業負荷を軽減するのに役立ちます。
一部の使用可能なサイドマテリアルは、指定された場所に配置され、曲げ時にトライアルモールド用のマテリアルを提供します。ワークピースを打ち抜いた後、必要に応じてコーナー、バリ、コンタクトをトリミング(研削処理)する必要があります。ツールコンタクトはフラットファイルでトリミングする必要があります。バリが大きいワークピースの場合は、グラインダーを使用してトリミングし、内側の穴のコンタクトを小さくします対応する小さなファイルを使用して、美しい外観を確保するためにトリミングします。同時に、形状のトリミングによって、曲げ時の位置決めも保証されるため、曲げ時の曲げ機でのワークピースの位置が一定になり、同じバッチの製品のサイズが一定になります。
ブランキングが完了したら、次のプロセスに入り、異なるワークピースが処理要件に従って対応するプロセスに入ります。曲げ、リベット留め、フランジ付けとタッピング、スポット溶接、凸包、およびセグメントの違いがあります。ナットまたはスタッドは、1つまたは2つの曲げの後でプレスする必要があります。これらのうち、金型の凸包とセグメントの違いを考慮する必要があります。最初に処理した後、他の処理との干渉を避けるために最初に処理し、必要な処理を完了できません。アッパーカバーやロアシェルにフックが付いている場合、曲げてもタッチ溶接できない場合は、曲げる前に加工する必要があります。
曲げるときは、最初に、図面の寸法と材料の厚さに従って曲げに使用する工具とスロットを決定する必要があります。製品と工具の衝突による変形を回避することが、上金型を選択するための鍵です(同じ製品では、それを使用できます)異なるタイプの上型)、下型の選択はプレートの厚さに応じて決定されます。曲げの一般的な規則は、最初に内側、次に外側、最初に小さく、次に大きく、最初に特殊、次に一般的です。プレスする刃先のワークは、まず30°〜40°に曲げ、レベリングダイでワークを潰します。
リベットするときは、スタッドの高さを考慮し、同じ金型と異なる金型を選択してから、プレスの圧力を調整して、スタッドがワークピースの表面と同じ高さになるようにし、スタッドがしっかりと押し込まれたり、ワークピースの表面を超えて押し出されたりしないようにします。スクラップ。
溶接には、アルゴンアーク溶接、スポット溶接、二酸化炭素シールド溶接、手動アーク溶接などが含まれます。スポット溶接では、最初にワークピースの位置を考慮し、大量生産では、スポット溶接位置が正確であることを確認するための位置決めツールの作成を検討する必要があります。
しっかりと溶接するために、溶接するワークピースにバンプを作成します。通電溶接の前にバンプをプレートに均一に接触させて、各ポイントの加熱が一定になるようにし、溶接位置を決定することもできます。同様に、溶接も必要です。予圧時間、保持時間、メンテナンス時間、休止時間を調整して、ワークピースをしっかりスポット溶接できるようにします。スポット溶接後、ワークの表面に溶接痕が出ますので、フラットグラインダーで処理してください。アルゴンアーク溶接は、主に2つの大きなワークをつなぐ場合や、ワークの角を処理してワークの表面を滑らかにする場合に使用します。 、スムーズ。アルゴンアーク溶接の際に発生する熱はワークを変形させやすく、溶接後は特にグラインダーとフラットグラインダーを使用してコーナー部を加工する必要があります。
曲げ、リベット留めなどのプロセスが完了した後、ワークピースの表面処理を行う必要があります。異なるプレートの表面処理は異なります。コールドプレートが処理された後、表面には通常電気メッキが施されます。電気メッキがスプレーされない後は、リン酸塩処理が使用されます。化学処理後、スプレー処理が必要です。電気めっきされた基板の表面は、洗浄され、脱脂された後、スプレーされます。曲げる前にステンレス鋼板(ミラーパネル、フォグパネル、伸線ボード付き)を描くことができます。スプレーは必要ありません。スプレーが必要な場合は、粗くする必要があります。アルミニウムプレートは通常酸化されており、異なるスプレーの色に応じて異なる色を選択できます。酸化したアンダートーン、
一般的に使用されるのは、黒と自然な色の酸化です。アルミニウムパネルは、クロメート酸化処理後にスプレーする必要があります。表面前処理により、表面をきれいにし、塗膜の密着性を大幅に向上させ、塗膜の耐食性を2倍にすることができます。洗浄プロセスは、最初にワークピースを洗浄し、最初にワークピースを組立ラインに吊り下げ、最初に洗浄液(合金脱脂)を通過し、次に清浄水に入り、次にスプレー領域を通過し、次に乾燥領域を通過して、最後に組立ラインからワークピースを取り出します。削除する。
表面前処理後、溶射工程に入ります。組み立て後にワークを溶射する場合は、歯または導電穴の一部を保護する必要があります。歯の穴は柔らかい接着剤スティックに挿入するか、ねじでねじ込むことができます。大量の位置決め工具を使用して位置決めと保護を行い、スプレーがワークピースの内部に噴霧されないようにします。ワークピースの外面に見えるナット(フランジング)穴は、スプレー後にワークピースのナット(フランジング)穴を避けるためにねじで保護されます。戻る必要があります。
一部の大容量ワークピースは工具保護も使用します。ワークピースにスプレーが装備されていない場合、スプレーする必要のない領域は高温のテープと紙で塞がれ、露出したナット(スタッド)穴はネジまたは高温ゴムで保護されます。ワークピースの両側にスプレーする場合は、同じ方法を使用してナット(スタッド)穴を保護します。小さなワークピースにはリード線またはペーパークリップなどのアイテムを一緒にスプレーします。一部のワークピースは表面に高い要件があるため、スプレーする前に削る必要があります。一部のワークピースは接地されていますシンボルは特殊耐熱ステッカーで保護されています。スプレー時は、まずワークを組立ラインに吊り下げ、表面のゴミをエアパイプで吹き飛ばします。散布エリアに入る散布後、組立ラインをたどって乾燥エリアに入り、最後に散布したワークを組立ラインから取り出します。その中で
手動スプレーと自動スプレーの2種類があるため、使用する工具は異なります。
スプレー後、組み立て工程に入ります。組み立てる前に、スプレー工程で使用した保護ステッカーを剥がします。部品の内部のネジ穴に塗料や粉末がふりかけられていないことを確認します。工程中は手袋を着用して、手にほこりが付かないようにしてください。ワークには、エアガンで吹き飛ばす必要のあるワークがあります。組み立て後、梱包工程に入ります。検査後、ワークは専用の梱包袋に入れて保護されます。特別な梱包のないワークには、バブルフィルムなどで梱包された後、バブルフィルムがワークのサイズにカットされます。包装と切断を同時に行わないようにして、処理速度に影響を与えます;大量にカスタマイズできます
特別なカートンまたはバブルバッグ、ゴムパッド、パレット、木箱など。梱包後、カートンに入れ、対応する完成品または半製品のラベルをカートンに貼り付けます。
板金部品の品質は、製造工程での厳しい要件に加えて、製造とは無関係に品質検査が必要です。1つは、図面に従ってサイズを厳密に確認することであり、もう1つは、外観品質を厳密に確認することです。サイズが一致しない場合は、修理またはスクラップします。スプレー後の色差・耐食性・密着性を確認できます。このようにして、展開図面のエラー、プロセスの悪い癖、およびパンチ数のプログラミングエラーやモールドエラーなどのプロセスのエラーを見つけることができます。
自動車の板金は自動車の修理の技術的手段です。この点で、自動車の板金は自動車の板金の修理と同じであり、自動車の衝突後の車体の修理を意味します。つまり、車体の防錆と装飾のスプレー作業を除くすべての作業です。 。車体損傷の分析、車体の測定、車体板金の成形、ストレッチ補正、応力緩和溶接、車体付属品の組み立てと調整など。
自動車板金は自動車整備の加工方法であり、正直に言うと、車体の外観が傷ついたり変形したりすると板金の加工が必要になります。車の衝突修理は、元の「プル溶接修理」から車体の二次製造アセンブリに進化しました。衝突時の車両の修理は、もはや自動車の板金を打つだけではなく、修理の品質は肉眼だけで車両の外観と隙間を観察することに頼ることはできません。保守要員は、車体の技術的パラメータと寸法を理解するだけでなく、車体素材の特性、力特性の伝達、車体の変形傾向と応力点、溶接技術などの車体の製造プロセスを習得する必要があります。この知識を習得した上で、メンテナンス担当者は高度な測定ツールを使用して、車体の正確な3次元測定を通じて車体の直接的および間接的な損傷と変形を特定し、完全な車体を作成する必要があります。修理計画は、正しいメンテナンスプロセスとボディのキーポイントの正確な3次元サイズデータと調整され、ボディのキーポイントは元の位置に戻され、損傷したボディが工場を出たときの状態に復元されます。
アルミ 板金 品
クイック 板金
板金加工、煙突、鉄ドラム、オイルタンク、エアダクト、エルボ、丸頭、丸いスペース、漏斗などを作るための板金の使用。主なプロセスは、せん断、曲げ、曲げ、曲げ、溶接、リベット、等。特定の幾何学的知識。シートメタルパーツは薄板のハードウェア、つまり、スタンピング、曲げ、ストレッチなどの手段で処理できるパーツです。一般的な定義は、処理中に一定の厚さを持つパーツです。鋳物・鍛造品・機械加工部品等に対応
PTJは、板金から高品質の部品を加工することで定評があります。大型のレーザーカッターとCNCターニングセンターで複雑な部品を加工できます。
鋼、ステンレス鋼、アルミニウム、真鍮、銅、青銅、チタンの部品および部品の板金加工。長さ36フィート、幅20インチまでの部品を+/- 0.005インチの公差で加工できます。厚さは0.005インチから0.188インチの範囲で、プレス能力は5トンから100トンです。ロール成形製品には、チャネル、チューブ、アングル、バー、リングが含まれます。事前亜鉛メッキ、事前塗装、事前陽極酸化、事前メッキ仕上げが可能です。低公差のミニチュア部品も生産されています。機能には、挿入、スウェッジ、パンチング、バリ取り、溝加工、溝入れ、リング曲げが含まれます。矯正、スカイビング、エッジローリングなどのフラットで成形されたワイヤー成形技術。今すぐお問い合わせください!
認定と品質
|
|