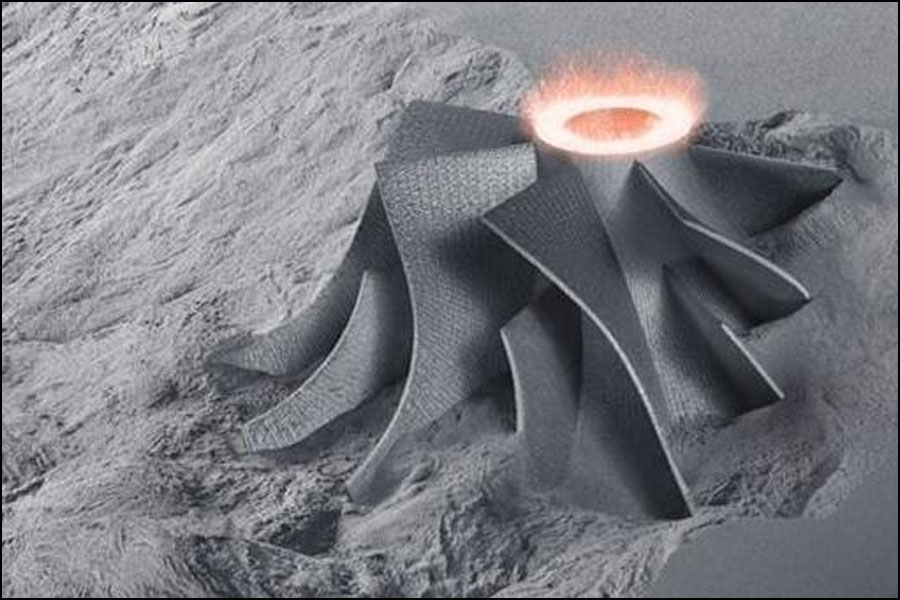
挑戦的な金属を選んで加工する場合、経済効率が重要な考慮要素です。強化された面取りエッジを持つCBNブレードは50 RC以上の切削硬度を持つ材料を除去したときによく見られるエッジ破断を除去した。
全硬化鋼、硬質粉末金属、耐熱高温合金、二金属は工業的に広く認められています。このような材料はほとんど堅固な部品を提供できますが、加工が困難になりました。幸いなことに、切削工具の供給商はフライスと旋削困難材料の刃において大きな進歩を遂げました。
今日のコーティング硬質合金,金属セラミック,立方窒化ホウ素(CBN)および多結晶ダイヤモンド(PCD)ブレードが役割を果たしている。特殊な幾何学形状とコーティングを備えた高級材料ブレードは機械的衝撃と耐熱に耐えられ、研磨材の摩耗にも耐えられます。しかし、これらのブレードを有効に使うには、さまざまな外部要因が必要かもしれません。そのうちの一つは経験豊富なツールサプライヤーとパートナーシップを構築することです。
切削刃のコストが比較的低いため(通常は硬質合金の刃を使うのは総加工コストの3%だけで、CBN刃を使うのは5%から6%だけです)、安い刃を使うのは間違いの経済的なやり方かもしれません。先進的な材料ブロックはサイクルタイムを短縮できます。或いは交替ごとにもっと多くの優れた部品を獲得して、コストを回収できます。
一方、大フライスに不必要にヘテロブレードを充填することは高価なミスである。CBNブレードのコストは硬質合金の8倍から10倍です。これらの高級材料の刃は誤った速度と送り速度で作動すると部品の品質と刃物の寿命を損ないます。在庫が難しい場合、適切なブレード
正しい送りとスピードを採用します。
アプリケーション全体を考慮します。解像度と切片の交換にかかる時間を考慮して、公差と表面あらさの面で効果を発揮できる安価な硬質合金ブレードは高価かもしれない。本当の生産性はスループット,循環時間およびブレード性能のトレードオフに対する理解から生じる。
専門的で、小ロットの例では、コーティング硬質合金の切削刃で炭化チタンガスターボ羽根の焼結に成功した。120 sfmでは、硬質合金の切削刃は5~10分しか切削できません。大量生産において、加工しにくい材料は通常許容できる刃の寿命を15分から30分と定めていますが、低速部品に対して、刃の寿命が短く、頻繁に工具を交換するのは主要な欠点ではありません。より長いブレードの寿命は生産全体において確かに重要になりますが、ブレードの停止時間と人工を減らし、マシンの利用率と生産性を向上させます。硬質合金は現在タービンの葉っぱによく使われていますが、部品がより高い量産を行うなら、CBNを使ったより硬く、より高価なブレードが合理的であることが証明されます。
先進的な材料のブレードを使って生産性を高めるには、正しい送りとスピードを採用しなければなりません。山特维克乐満のCBN刃は、50 RC以上の硬质材材を切削する际によく见られる縁破裂を除去することができる强固な面取りを持っています。この靭性にもかかわらず、CBNブレードは切削マシンパラメータに厳しい公差を保つように要求されています。切削速度が10%以下、または10%以上となり、性能に大きな影響を与えます。
加工が難しい材料が必要なら、切削工具の供給先に連絡してください。サプライヤーは他の人がどうやって同じ問題を解決するかによって解決案を提供することができます。試験が必要な場合は、通常、硬質合金ブレードから慎重に試験を開始し、その後、より硬く、より高価な刃物を使用します。近代的なブレードの幾何学形状、剛性ブレードと完璧な加工手順は、通常、コストの低い硬質合金ブレードを困難な作業に適しています。いつ炭化物を越えるかは応用によって違いますが、さまざまな材料がよくある加工に挑戦します。
硬化鋼
多くの応用に用いられる鋼合金はますます硬くなった。工具鋼は45 RCの硬い材料と考えられていましたが、63 RCに硬化した鋼は今では金型工業でよく見られます。熱処理前に部品を切断した金型メーカーは、現在は完全硬化状態の精密加工工具鋼で、熱処理変形を避ける。フライス削りが完全に硬化した合金の場合の熱量と圧力は切削刃の塑性変形と刃の高速失効をもたらす。
それでも、完全に硬化した鋼は炭化物で経済的に加工できます。一例は航空宇宙加工に関するものです。主要な航空メーカーは、山特維克GC 1025硬質合金ブレードを選択し、4340型の改造型急冷300 M型鋼の大型鍛造品を新たに穴あけしました。鋼の硬度が30から32 RCの場合、熱処理前に大部分の金属を除去します。しかし、変形を是正するためには、ワークを完全に54または55 RCに硬化させると、大きなワークに穴を開け直さなければなりません。
部品の深いところの一つは特に挑戦的な特徴があります。三回ボーリングしてこそ、必要な公差と光沢が得られます。一度しかない時間に、硬質材料は切れ目の切断と結合して、金属セラミックの切削刃を磨耗しました。折れた縁が部品を破損する恐れがあることを考慮して、特に衝撃的です。対照的に,先進的な微細結晶粒硬質合金ブレードは硬い物理蒸着(PVD)皮膜と鋭い切削作用を持ち,6〜9回の切削が可能である。硬質合金ブレードを利用するために、バイト先は切削速度を300 sfmから175 sfmまで下げることを提案していますが、同じ切削深さを維持しています。硬質合金の刃は低いスピードで孔を三回通ると約20分かかりますが、金属セラミックナイフは一時間以上かかります。もっと重要です
加工パラメータを構築するには、硬質合金ブレードを有する硬化鋼をフライスで削り、通常は100 sfmから開始する。試験紙の速度は150から180 sfmに達することができます。通常の送り速度は歯あたり0.003~0.004インチです。中性またはやや負の前角を持つブレード幾何学形状は,通常,正前ブレードよりも強いエッジを提供する。円形硬質合金ブレードは、硬鋼を加工する際にも優れています。輪郭はより強力なツールを提供し、傷つきやすい尖角がない。
硬質合金のナンバーを選ぶ時は、強靭なナンバーを考慮してください。それらは硬化鋼に遭遇する高い径方向切断力と厳しい輸出入衝撃に抵抗するためのエッジ安全性を提供する。また,特殊な調合の高温鋼種は,60 RCまでの急冷した鋼から発生する熱に耐えることができる。アルミナコーティングを施した耐震硬質合金ブレードは、硬鋼フライスによる高温にも抵抗できます。
焼結金属
粉末冶金技術の進歩は,種々の応用に用いられる超硬焼結金属を生産している。メーカーは53から60 RCまでの硬さを実現するためにタングステンまたは炭化チタンを含む粉末状のニッケル複合合金を開発した。ニッケル合金マトリックス内の炭化物粒子は90 RCに達することができる。このような材料をフライスで削ると、コーティングされた硬質合金の刃が急速に側面の摩耗を受け、主な切削刃が平らになります。微細構造中の超硬粒子は「微屑」を形成し,ブレードの摩耗を加速させる。硬質合金ブレードは硬質材料を加工するせん断圧力でも破断する。
CBNブレードはタングステンと炭化チタンを含む硬質粉末金属の切削に使用できる。先進的な幾何学形状は微細チップを克服できる。あるフライス削り粉状複合合金のユーザーは、先進的なCBNブレードの使用寿命は最適な硬質合金ブレードの使用寿命より2,000倍長いことを発見した。一台の五面フライスは200 sfmの速度で運行しています。各エッジの送り量は0.007インチで、硬質切削加工より早く硬質材料の切削を完成しました。スピードは75%アップしました。
CBNを十分に利用するためには、切削パラメータは狭い範囲に保たれなければならない。速度は約160 sfmで、送り速度は歯あたり0.004~0.006インチであるが、焼結材料を加工する際の生産性は高い。正確な加工パラメータは30秒から60秒の試験切削によって決定するのが望ましい。低速から、切削刃が過摩耗するまで積み重ねていきます。
加工しにくい材料は通常機械で加工して乾燥させ、切削刃の温度を一定に保つ。ほとんどの場合,二重負性幾何形状を持つ円形工具が最も有効で,切削深さは通常0.04から0.08インチに制限される。
定義によると、フライス削りは間欠切削です。ロックウェル60または高硬度の材料に次々と金づちをかけて硬化すると独特の加工応力が発生します。したがって、機械と工具は最大の剛性、最小の懸垂と最大の強度を提供しなければなりません。加工中の高衝撃負荷に適応します。
超合金
航空宇宙事業のために開発された耐熱スーパー合金(HRSA)は、自動車、医療、半導体、発電用途で広く認められています。現在、より新しいチタン基体とアルミニウムマグネシウム基体材料は、Inconel 718と625、Waspalloyと6 Al 4 VチタンなどのおなじみのHRSAを結合しています。これらは全部加工に挑戦しました。
高温合金は難しいです。いくつかの等級のチタンは330布の硬さで加工します。従来の合金では,切削温度が2,000°Fを超える温度は分子結合を軟化し,切削粉の流れ領域を形成する。逆に、HRSAのような理想的な耐熱性は、加工サイクル全体にわたって硬く保たれています。
HRSAは切削時にも硬くなり、切削刃に切欠きが生じ、早期に失効することがあります。HRSAを切断するのはもっと難しいです。皮をむいていない原料に研ぎ刃状の刃の酸化皮を覆うので、切削刃が早く磨かれます。
加工の難しさから、スーパー合金は切削速度が遅い。例えば、マティックGC 2040クラスの硬質合金ブレードを使用して、Inconel 718を200 sfmのブレーキキーに削ります。室外旋削/装飾面応用において、サントビック7020 CBNブレードを使用して同じ合金に対する旋削速度は260 sfmである。対照的に、非コーティングの硬質合金ブレードは通常400から800 sfmの速度で工具鋼を切削する。HRSAに使用される供給は通常、工具鋼の加工時に使用される供給に相当する。
HRSAを加工する切削ブレードの選択は材料とワークに依存します。前角幾何学形状が正の硬質合金ブレードは薄壁HRSA在庫を効率的に切断する。しかし、厚い壁の部品は負の切削刃幾何学形状のセラミックチップを必要とするかもしれません。ほとんどの加工しにくい材料の中で、均一なエッジ温度を維持するために乾式加工を採用したほうがいいですが、チタンは極めて低い速度でも冷却剤が必要です。
HRSAの持続硬さは切削刃先半径の摩耗を加速させる。先端のない円形刃は最強の切削刃を提供することができますが、HRSAによくある加工硬化はブレードの漸進的な切削溝を引き起こすことができます。連続加工時に切削深さを変えると加工硬化領域が回避され、切欠きの形成がなくなり、切削刃の寿命が長くなります。切断深さは、一度に通過する0.3000インチから、後続のカットの0.25インチと0.100インチに変化することができます。
二重金属
二金属部品は、よりソフト合金に囲まれたまたは混合された特定の摩耗領域に硬質材料を置く。彼らは自動車工業や他の分野でますます人気があり、加工に対して特別な挑戦をしました。CBNブレードは切削性の高い高硬度切削合金で、柔らかい材料に当たると破裂する恐れがあります。アルミを研磨したPCDチップは、黒い金属を切削する際に、過剰な摩耗を受けることがあります。
機械加工二重金属部品は有効的にユーザー、工具サプライヤーと機械サプライヤーに完璧な加工手順を開発するように要求します。1つの応用では、前述の硬質粉末金属複合合金熱などを低コストの316ステンレス基板上に静圧する。機械制御システムにプログラミングした螺旋補間工具の経路は最適な送りとスピードを採用して、粉末金属エリアを先に加工して、底材を加工します。
二金属シリンダーを効果的に加工するために、自動車メーカーは同時に腐食性アルミニウム合金と鋳鉄シリンダーカバーに対応しなければなりません。部品の設計は硬鉄磨耗エリアがソフトアルミニウムと切り離せないことを意味します。しかし、非常に低い速度と非常に浅い切削深さを提供する工作機械プログラムは、工具を頻繁に交換することなく、耐磨耗PCD刃を同時にアルミニウムと鉄を加工することができます。