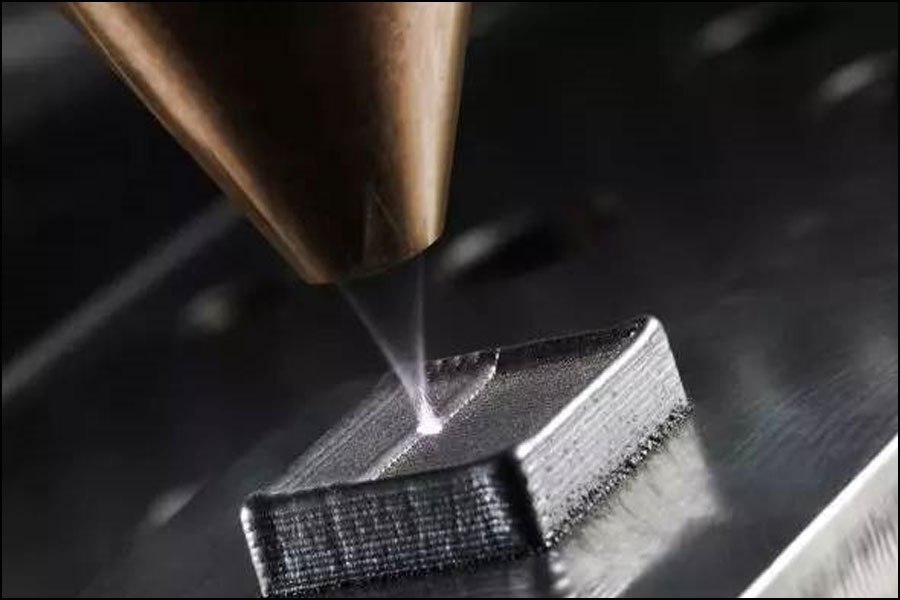
増材製造(AM)は、ほぼいかなる材料でも高度に固定化された製品を生産する技術であり、設計の柔軟性のため、航空宇宙から医療までの様々な応用のために3 D印刷金属部品を生産することができる。
しかし、AMのユニークなデザインには障害があります。
新しく印刷された金属部品は構造支持を除去するために追加の加工ステップが必要で、粗面のあらさと信頼できない寸法精度は精密部品(嵌合面とねじ穴など)の標準に達しないかもしれない。増材製造には複雑さが必要ではなく、部品は従来の直交形状に適合する必要がないため、カスタム部品はワーククランプに特に挑戦的な形状を持つことがあります。
なぜ金属を使って増材製造をするのですか?
AMは金属の理想的な工芸です。これは伝統的な工具を必要としないで、多くの幾何学的な制限を考慮する必要がなく、部品の結合を許可して、より効果的な設計を実現します。これは複数の金属合金を航空宇宙、自動車、医療応用の理想的な材料にし、射出成形の生産性を高め、建築などの創意産業の可能性を広げた。
特に溶接と鋳造に適した金属は3 Dプリントの理想的な選択です。逆に切削や加工コストの高い金属も増材製造の理想的な選択です。いくつかのよく使われている3 D印刷金属はチタン、アルミニウム、ステンレス、工具鋼、クロムニッケル鉄合金、銅とタングステンを含んでいます。
チタンは軽量で航空宇宙や医療用途で人気があります。内部格子構造を利用して,骨格の内側成長に適応するために,インプラントを設計することができる。一方、鋼は、極端な環境(例えば、燃焼や高圧力)に耐えることができる堅固な部品を印刷するために用いることができる。これらおよび他の金属は粉末または溶融した金属糸から印刷できる。
種々の技術を用いて,粉末ベッド用の選択的レーザ焼結(SLS)と,粉末または金属フィラメント用のレーザ金属堆積(LMD)と金属フィラメント配向エネルギー堆積(WED)を含むMetal AMを実行することができる。
SLSは、X軸とY軸に沿って密封された不活性ガス環境において、金属粉末を下降したトレイに融解するCO 2レーザを用いて、より複雑な設計を有するより小さな部品を「堆積」技術を用いて製造することで人気がある。トレイはレーザーの次の通過前に下がります。ローラーは平らに保ちます。
WEDはレーザ融解を用いてノズルを通して注入されたワイヤを用いて、通常は密封された気体シェルにおいて行われる。この方法はSLSに比べてより高い堆積速度を得ることができるが,分解能はより低い。WEDは、より簡単な部品が必要とされるアプリケーション及び従来の製造技術の緩やかまたは高価なアプリケーションで人気があります。例えば、航空宇宙や自動車分野で。
この技術によって、AMは製造しにくい部品のために大量のコストと時間を節約することができます。また、より複雑で、より小さいロットの部品を製造することもできます。
なぜ金属を使って増材製造をするのですか?
AMは金属の理想的な工芸です。これは伝統的な工具を必要としないで、多くの幾何学的な制限を考慮する必要がなく、部品の結合を許可して、より効果的な設計を実現します。これは複数の金属合金を航空宇宙、自動車、医療応用の理想的な材料にし、射出成形の生産性を高め、建築などの創意産業の可能性を広げた。
特に溶接と鋳造に適した金属は3 Dプリントの理想的な選択です。逆に切削や加工コストの高い金属も増材製造の理想的な選択です。いくつかのよく使われている3 D印刷金属はチタン、アルミニウム、ステンレス、工具鋼、クロムニッケル鉄合金、銅とタングステンを含んでいます。
チタンは軽量で航空宇宙や医療用途で人気があります。内部格子構造を利用して,骨格の内側成長に適応するために,インプラントを設計することができる。一方、鋼は、極端な環境(例えば、燃焼や高圧力)に耐えることができる堅固な部品を印刷するために用いることができる。これらおよび他の金属は粉末または溶融した金属糸から印刷できる。
種々の技術を用いて,粉末ベッド用の選択的レーザ焼結(SLS)と,粉末または金属フィラメント用のレーザ金属堆積(LMD)と金属フィラメント配向エネルギー堆積(WED)を含むMetal AMを実行することができる。
SLSは、X軸とY軸に沿って密封された不活性ガス環境において、金属粉末を下降したトレイに融解するCO 2レーザを用いて、より複雑な設計を有するより小さな部品を「堆積」技術を用いて製造することで人気がある。トレイはレーザーの次の通過前に下がります。ローラーは平らに保ちます。
WEDはレーザ融解を用いてノズルを通して注入されたワイヤを用いて、通常は密封された気体シェルにおいて行われる。この方法はSLSに比べてより高い堆積速度を得ることができるが,分解能はより低い。WEDは、より簡単な部品が必要とされるアプリケーション及び従来の製造技術の緩やかまたは高価なアプリケーションで人気があります。例えば、航空宇宙や自動車分野で。
この技術によって、AMは製造しにくい部品のために大量のコストと時間を節約することができます。また、より複雑で、より小さいロットの部品を製造することもできます。
治具と万力は通常第一選択の治具解決策であるが、この選択は幾何学形状が複雑な3 D印刷部品に対して無効である。
より複雑で精緻な部品に対して、柔軟なピンセットはとても良い解決策です。それらの輪郭はより正確に部品に適合できるからです。これらの柔らかい顎は自分で3 Dプリントができます。これらの解が有効であることはカービィ(Kirby)により発見されたが、小さい印刷部品(例えば医療用部品)は通常、機械加工に耐えられる負荷公差に設計されていない。
加工技術と適切な治具解決案を考慮する時、これらの制限をしっかりと覚えなければなりません。
添加過程によっては、まずベースまたはバックプレートからフルプリントの金属3 D部品を切り取る必要があるかもしれません。いくつかの材料は非常に硬くて、手作業で帯鋸操作が危険になり、浪費と高価になります。この場合,電気スパーク線切断または電子放電加工は良い選択である。
MakinoのEDM製品ラインマネージャーBrian Pflugerによると、EDMは部品としての単独操作が可能であり、非常に高い再現性と精度を持っています。部品の除去と表面仕上げに使用できます。Wire EDMのようなオプションは、手動でのドリフト操作に比べて無駄が大幅に低減され、部品が破損する可能性が非常に小さい。
Wire EDMを使用して、部品の最終的な一致を約10ミクロンの範囲で維持して、最終的な研磨、フライスまたは部品加工を行うことができます。部品が切断された時には、もっと一致します。廃品をなくすことができます。
従来の機械加工と表面仕上げのオプションに比べて,EDMはまた優れた解決策であり,斜め穴,異形特性を生成し,厚み可変の部品に沿って表面を精密に加工することができる。
Wire EDMマシンごとに、いわゆる適応電力制御があります。材料厚の動的変化により,可変厚さは非常に骨が折れる。マシンジェネレータは、見て感じて反応する必要があります。断線の原因になります。」
通常、粒状の材料(粉末など)は濾過されますが、大きな粉末袋はシステムを破壊し、適応電力制御によって補える範囲を超えて、断線してしまいます。これは機械の運行速度を低下させ、破壊されます。これらの穴は3 D部品として設計された中空空間に堆積している。
このような凹凸を洗浄ノズルが越えると流体の流れは圧力を失い,効率が低下し,圧力が低下し乱流が発生する。浮遊粒子はEDMワイヤを破損する。大径の電線は、あるいは異なる種類の電線を使用すると、より長い時間耐えられますが、多くの電線EDMマシンでも自動的に線を通すことができます。
Sinker EDMは別の選択であり、より高い精度とより良い表面あらさを必要とするより小さな特徴を専門に研究する。Sinker EDMは加工が困難な鋭い内角半径またはブラインドを作るための理想的な選択である。
Big Kaiser作業場製品マネージャーのJohn Zayaは、WireやSinker EDMが理想的な解決策ではないようであれば、ハイブリッドマシンは添加剤も含まれており、加工能力も含まれていると説明しています。
「理論的には、部品を皿に3 Dプリントし、3 Dプリントの部品に組み立てて、機械が加工モードに入ります。実際の切削工具を使って切削工具を減法し、そのワークを最終加工します。」
ハイブリッドマシンでは、2回の操作の間、部品は同じ治具にしっかりと保持され、精密加工のために部品を位置決めする面倒がなくなりました。
金属増材製造の冶具ソリューション
Zayaは、作業管理は増材製造過程において最も重要な要素の一つであり、生産過程の各段階において考慮しなければならないと考えている。部品は製造可能であり、サイズ、形状、材料を含めて考慮しなければならない。部品に使用されるあらゆるマシンの治具ソリューションに関連しているからだ。
Zaya氏は「製造エンジニアとの初歩的な相談によって、生産ラインで発生する可能性のある問題を多く避けることができます。」
Zayaは、いくつかの事前の計画により、部品を固定板に積み上げるか、それともワークの設計において特殊な取り付け幾何形状を考慮して、部品をプリンタから取り外した後、クランプノブを部品に接続することができると続けています。
マイケルは、金属の3 Dプリント部品を処理する方法の一つとして、5軸工作機械を使って、少なくとも1/8インチの材料を挟んだり、燕尾ほぞを使ったり、位置決めピンを直接ワークに置いたりしています。基本的にはマシン全体の加工を一度にして、反対側を反転させて掃除してもいいです。
このような展望解が使えない場合(例えば高度に複雑な幾何学形状や敏感な設計のため)は,柔軟なクランプが鍵となる。しかし、この方法は部品の輪郭と顎の半径に注意する必要があります。
Gaunceは、ソフト顎の半径を部品の半径よりも小さくし、正確なグリップ力を確保し、二つの点に締め付けることを提案しています。Zayaは、3 Dプリントの効果を知る必要があると付け加えた。
Zayaは「柔らかいピンセットにワークを入れて、ワークの表面のあらさが非常に粗い場合、その特徴の高いところに位置します。」完全な連絡が取れていないかもしれません。一部の地域でしか登録できません。
固形の特徴をあらかじめ設計しておくと、部品の設計がより簡単になり、より信頼できるようになります。Zayaは、位置決め穴と締め付け特徴は予めワークや鋳物に印刷しても良いと説明していますが、ステーやクランプやボルトの凹み領域は、大きな部品のワークに印刷できます。「ワークの設計をクランプ位置やツール位置を含めて計画しておくことは、後続の操作に備えておくために非常に有益です。」
最悪の場合は部品が特に弱く、壊れやすいです。そして、万力や治具がないと安全に仕事ができます。また、意匠チームは、接着剤のある薄いワークや小さなワークに対して、特にユニークな解決策を提案することができる。
レイニー紹とウォータールー大学は最近、手術中に人の股関節に合わせるための装置を設計しました。部品のユニークなデザインと生成デザインにより、チームは部品を「コブラ」とニックネームで呼んでいます。部品には4つのピンを加工する必要があります。医療プログラムのためにインストールして反射器に向かうためです。重要なのは加工中に部品を変形させないことです。
部品を基板に固定するために、3 Dに対して一連のパッドをプリントし、板に締めます。特殊な接着剤を下敷きに塗って、部品を所定の位置に固定します。
Kirbyは「接着剤は紫外線で活性化され、部品が変形しないようにしています。」「部品を接着剤の中に入れて固化すると、部品の位置は大体1ミリ以内と分かります。その後、我々は最も適切な探知を使用しなければならない。
紫外線にさらされると、糊は90秒で硬化し、チタン部品を適切な位置に効果的に接着します。
部品の設計と製造におけるユニークな挑戦を解決したいメーカーにとって、金属増材製造はツールボックスの中のツールですが、これらの部品を適切に固定して、最終仕上げと後処理を行います。