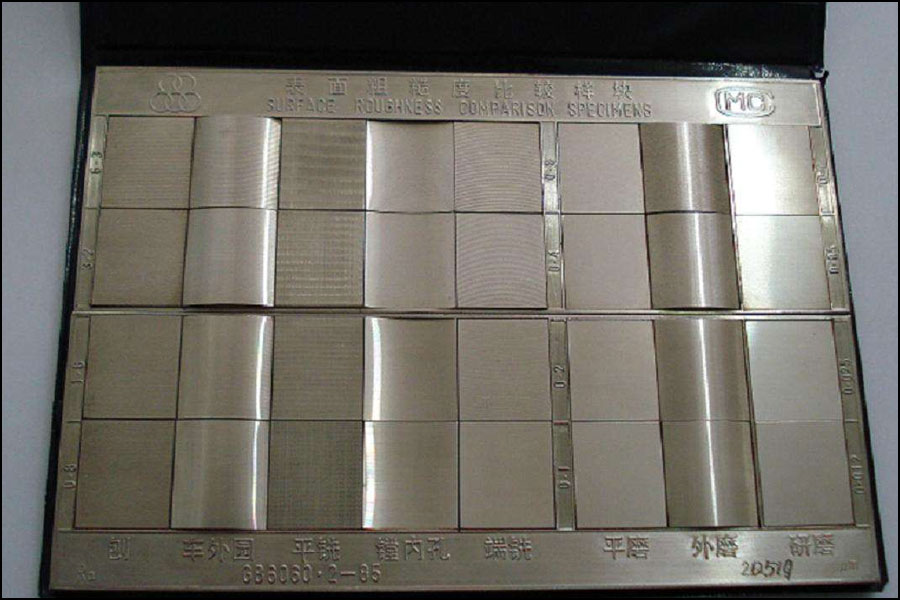
粗さはアルミニウム板製品の表面品質を測定する重要なパラメータである。より小さな粗さは、製品の表面仕上げを改善するのに有益であり、効果的にアニーリング中の層間摩擦に起因する表面付着を低減することができる。切断面のトポグラフィーは2つの異なる部分に分けられる。上面は平坦で滑らかであり、切断ストライプはニートで微細であり、粗さ値は小さい。下部切断ストライプは無秩序であり、表面は凹凸であり、粗さ値は大きい。上部はレーザビームの直接作用に特徴があり,下部は溶融金属の侵食により特徴づけられる。切断面の上部の表面粗さは一般に均一であり、高さによって変化しないが、下部の表面粗さは高さと共に変化する。下縁に近いほど、表面粗さ値が大きくなる。表面粗さは上限に達する。
それが連続レーザ切断またはパルスレーザ切断であるかどうかにかかわらず、切断面は明らかな上部と下部を示している。違いは、パルスレーザ切断面の上部の切断フリンジがパルス周波数に対応することである。また,連続レーザ切断中の切断面における切削縞密度と表面粗さは主に切削速度に関連する。従って、切断面の品質を評価する場合は、下縁の表面粗さを基準とする。しかし、本当の一番下の端はちょうど線です、そして、粗さは測定するのが難しいです。底部縁近くの粗さは、「近底面エッジ粗さ」と呼ばれている。ワークの厚さは物理的パラメータでも調整可能なパラメータでもないが、レーザ切断の表面品質に大きな影響を与える。一般的には、肉厚が小さい金属材料は、金属厚の厚い被削材よりも高い粗さを得ることが容易である。
レーザ切断技術は,低コスト,高効率,高精度のため,計装やエレクトロニクスなどの精密産業で広く使用されている。レーザ切断壁シームの粗さを改善するために,国内外の研究者が処理プロセスパラメータに関する研究を行い,様々な最適化方法と理論を提案したが,研究対象として代表的な直線スリットを取るだけで,最終的には最小粗さを得るその目的,レーザ切断アークモデルの確立と加工品の全体粗さの最適化は考慮されない。この状況に基づき,レーザ精密切断と脱離法のアークと直線の粗さの違いに関する研究を行った。
- 1)レーザ切断におけるアーク壁縫い目の粗さの数学モデルを確立した。0 . 5 mm厚の1060枚の純アルミニウム板を正確に切断するためにnd:yagレーザを使用した。切断後,表面スラグや他の破片を除去するためにアルコールでこすり,顕微鏡を通して試料のアーク切断壁縫い目の微視的形態を観察し,幾何学的関係推論によるアーク粗さの簡略化した数学モデルを確立した。内部および外側のアーク壁面の粗さの式を取得します。
- 2)レーザ切断のアーク粗さに及ぼす切断寸法の影響を論じた。直線粗さ公式を直線粗さ公式と比較すると,切断速度,レーザパルス周波数及びパルス幅に加えて,内部アークとアウターアーク粗さも切断アークサイズの影響を受けることが分かった。同じ切削パラメータのもとで,理論計算と実際の切削実験により,内半径と外壁の違いに対する切削半径の影響を解析した。その結果,切断半径が増加すると,外壁壁面粗さが増加することが分かった。切断半径が7 mm以下では、内側と外側の円弧の粗さは著しく異なり、切断半径が7 mm以上では、両者の粗さ差は無視できる。
- 3)応答曲面法の最適化への応用,粗さの違いを除く。切削実験は設計支援設計ソフトウェアエキスパートを用いて設計し,二次回帰式を構築し,分散解析した。その結果,モデルはフィッティング効果が高く,フィッティング効果が良好であり,フィット感がないことが分かった。得られた二次回帰式を用いて予測値を推定することは有効である。最後に,応答曲面法(rsm)を用いて,内側と外側のアークの最小粗さと直線をそれぞれ最適化し,得られた理論最小値の最大値を二次最適化の目標値とし,アークと直線の最小値を求める。粗さに対応したプロセスパラメータ実際の切削実験で測定した粗さ値はほぼ同じであり、直線と円弧との粗さの差がなくなる。この方法は実行可能で有効であることを証明した。金属切削用の同一切削面の上、中、下の粗さは同じではない。レーザ光の上端に近い面の粗さ、Raは小さく、粗面Raは下端に向かって大きい。しかし、細くなったワークでは、厚さが3 mm未満では、レーザ切断面の上部、中央、下部の粗さの差が非常に小さい。レーザ切断の表面品質は、一般的に、下端粗さ及びRaを基準とし、より現実的である。また、マスターすることは簡単です。