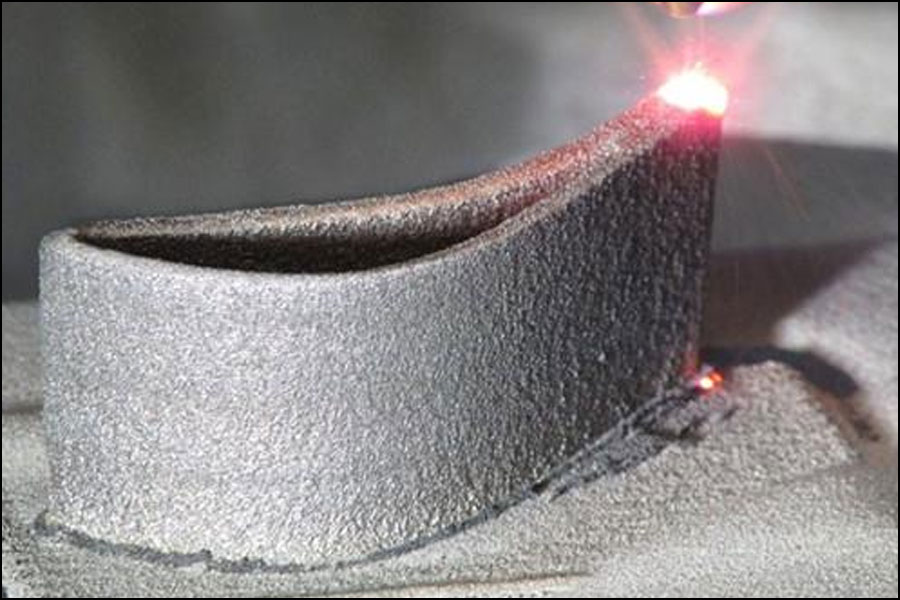
増材製造/金属3 D印刷技術は油圧弁体設計に最適化空間をもたらしました。特に弁体流体チャネルの最適化において、金属3 D印刷技術は特殊な優位性を持っています。
金属3 D印刷技術は油圧弁体製品の開発における柔軟性と複雑な部品の生産能力は従来の方法では不可能であるが、もし金属3 D印刷技術の弁体生産における応用をさらに開拓するなら、弁体デザイナーは表面処理プロセスによって金属3 D印刷部品の表面粗さを低減する方法を理解し、実際の生産を満足させる必要がある。必要です。
設計の初めはまもなく表面後処理計画を含める
表面粗さは金属3 D印刷技術にとってどれぐらいの影響があるかは主にその応用分野に依存する。場合によっては、粗さは重要ではないかもしれません。場合によっては、いいことかもしれません。しかし、多くの部品は表面の粗さに対して一定の要求があります。弁体は油圧システムの構成部分であり、最終的にはシステム全体と一体化するため、弁体の粗さに対して一定の要求があり、流体流量が正確に制御されることを保証する。
部品を加工する時、デザイナーはどのような加工技術を使うかを決定するために秤量を必要とします。
典型的な金属粉末射出成形は良好な表面品質(一般的にはRaは30-50)を持ち、鋳造は比較的粗い(Raは100から500ミクロンの間)。金属3 Dプリントの表面粗さは、通常Ra 250−400+より高い。
設計者の注意に値するのは、金属の3 D印刷の技術は多種があって、例えば:方向性のエネルギーは沈殿して、粉末のベッドは区のレーザーを選んで溶かして、各工芸の加工の金属の部品の持っている表面の粗さは異なっています。また、使用するプリンターの種類、ワークの複雑さ、プリント材料及び増材製造部品の設計方式、印刷時の部品の配置方向などの要素が3 D印刷部品の最終的な粗さに影響する可能性があります。
表面後処理プロセスによって、金属3 D印刷弁体の最終的な仕上げ度が向上しますが、表面後処理によってコストが発生し、一定の製造時間が増加します。そのため、設計者が金属3 D印刷を弁体の製造手段として決定した当初は、これらの要因を考慮して、弁体製造の総コストと周期に組み入れて、3 D印刷部品を設計する時にも必要です。後処理の残量を残します。
通常、後処理を行う前に、3 D印刷部品が必要な最終光沢度に近づくほど、仕上げの消耗が低くなり、逆に高い消耗が生じます。例えば、3 D印刷部品の表面の粗さが800 Raであれば、最終的には<50 Raを達成するには、かなりの費用がかかります。
多くの一般的な研磨後処理技術は、3 D印刷部品を表面粗さの要求に達することができる。しかし、これらのプロセスは必ずしもメーカーが独自に完成したものではなく、外注加工が必要となると、輸送や管理費用などの余分なコストが発生します。いろいろなことに参加する必要があると、品質問題のリスクも高くなります。
従来の製造方式は,弁体の設計,特に流体チャネルの設計最適化に及ぼす限界が明らかである。しかし,金属の3 D印刷技術は複雑な流体チャネルを持つ一体化した弁体を作ることができる。ますます多くの工業デザイナーが設計段階で増材製造を選択し始めるにつれて、金属3 Dプリント技術の真の潜在力は開発され、他のいかなる方式でも実現できない新型の弁体を作り出します。
市場研究機関Infinium Globalリサーチは2017年から2023年までの3 Dプリント市場は33%程度の年間複合成長率を維持すると予測していますが、油圧部品の3 Dプリントは無視できない3 Dプリント応用の成長領域になります。
弁体の加工について言えば、伝統的な方法でバルブブロックを製造する時、まず金属ブロックから始めて、伝統的な製造方法で金属ブロックを必要な外形に修正して、それから油圧流体の流れのための内部配管路を掘削します。これらの管路を正確に掘るのは非常に困難であり、管路は特定の点で正確に交差する必要があるが、いくつかの「ブラインド」ドリル位置では、管路は常に正確に整列できない。また、穴を掘る時にはプロセス穴を開けて最後に密封する必要があります。これは部品がプロセス穴の位置で漏れが発生する可能性があります。
3 Dプリント技術を採用することで、内部設計の柔軟性を高め、部品の重量と体積を低減し、機能性を向上させることができます。3 D科学谷の市場観察によると、3 D印刷技術は複数のメーカーが複雑な油圧部品を製造する選択となっている。例えばDomin Fluidd Power社が新たに設計し、製造した3 Dプリントバルブは、軽量、小型、弁体効率が高い。Aidrohydraulicsは3 D印刷技術を使って、お客様のために小ロットの油圧バルブブロックを生産しています。レニー绍はランドローバーBAR帆船が金属3 D印刷の油圧システム部品の性能を向上させて、滑らかな角を含む部品を加工して、流体輸送の効率を大幅に向上させました。エアバスは最初の3 D印刷用油圧部品を搭載したA 380飛行機が試験飛行に成功しました。
しかし、金属3 Dプリントのこのような増材製造技術は、弁体製造分野の発展において、従来の減材製造技術と競争関係になるとは限らない。逆に、増材と減材は相補的な技術であるが、多くの場合、機械加工などの減材後処理技術と金属3 D印刷の組み合わせで、要求に合う弁体を加工することができる。