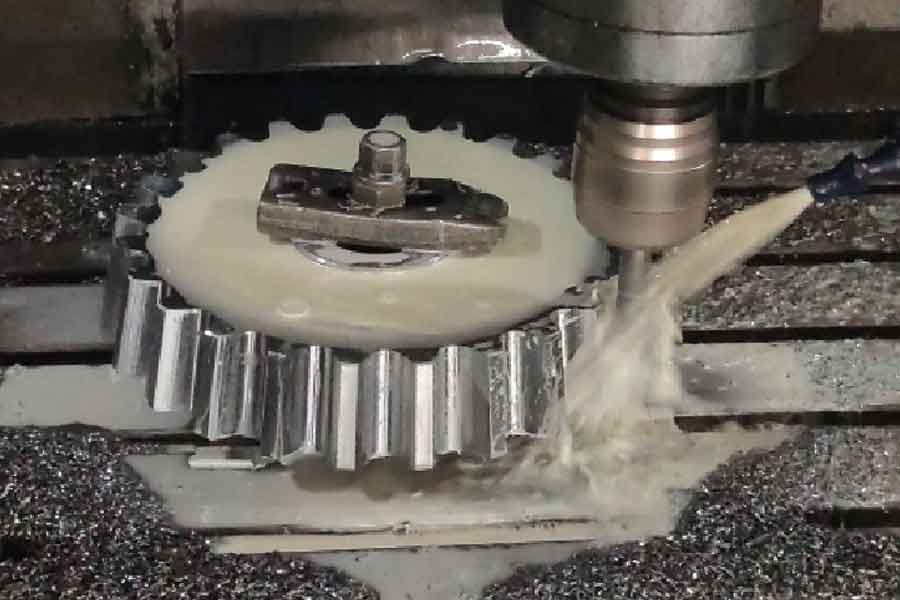
理想的なCNC加工プログラムは、図面に従って適格なワークピースを確実に処理するだけでなく、CNC工作機械の機能を適切に適用して十分に活用できるようにする必要があります。CNC工作機械は高効率の自動化装置の一種で、通常の工作機械より2〜3倍効率が高いので、CNC工作機械の特性を十分に発揮させるには、その性能、特性、操作方法の使用だけでなく、プログラミングの前に処理プログラムを正しく決定する必要があります。生産規模の違いにより、同じ部品の処理計画は異なり、特定の条件、経済的で合理的な処理計画の選択に基づく必要があります。1つは、処理プロセスがCNC工作機械の処理部品に分割されていることです。プロセスをより集中化することができます。プロセス全体を完了するには、クランプを可能な限り行う必要があります。通常の工作機械加工と比較して、加工工程分割には独自の特徴があり、一般的に使用される工程分割原理には次の2種類があります。
1.CNC加工の精度を確保する原則
CNC加工では、プロセスを可能な限り集中化する必要があります。多くの場合、ワークの形状、位置精度、寸法精度、表面粗さに対する熱変形と切削力変形の影響を減らすために、粗加工と仕上げ加工はクランプの下で完了します。荒加工と仕上げ加工は別々に行う必要があります。シャフトまたはディスク部品の場合、表面品質要件を確保するために、最初に粗加工が行われ、少量の仕上げが残されます。同時に、一部のボックス部品では、穴の加工精度を確保するために、穴を加工する前に表面を加工する必要があります。
2.CNC加工の生産効率向上の原理
工具交換の回数を減らすために、工具交換の時間を節約し、すべて完了した同じナイフ処理部品で使用してから、別のナイフを交換して他の部品を処理する必要があります。同時に、ワークピースの同じナイフ処理部品を使用して、空のストロークを減らすために可能な限り遠くにある必要があり、処理部品への最短ルートにある必要があります。実際には、CNC機械加工プロセスは、特定の部品の構造特性と技術要件に従って包括的に検討する必要があります。
処理ルートの決定
CNC加工では、ワークピースに対する工具の経路と方向(厳密には工具点)を加工経路と呼びます。つまり、工具が工具点から加工プログラムの終了まで移動する経路です。これには、切削経路と、工具の導入や返却などの非切削の空の移動が含まれます。加工経路の決意は、第一の寸法精度と表面品質を保証しなければならないCNC機械加工部品を、そして次に数値計算は、単純な、可能な、高効率の短いとしてCNC切削経路で考えます。以下の加工ルートでよく使用されるCNC工作機械加工部品の例です。
1.CNC旋盤のアウターコーンは、大径D、小径D、コーン長Lを想定しています。ターニングコーンの加工経路をします。
ップ切削ルートによると、2つの粗い切削工具と最後の細かい切削工具。2つのラフカッターの最終距離Sは正確に計算する必要があり、同様の三角形を取得できます。
これにより、工具の切削距離が短くなります。
対角線処理ルートによれば、最終的な工具距離を計算せずに、毎回ナイフ量apのみが決定されるため、プログラミングに便利です。ただし、切削ごとに切削量が変化し、工具の切削経路が長くなります。
2.カーアークアプリケーションG02(またはG03)コマンドカーアークの処理ルートの分析。
アークがナイフで処理されているため、ナイフが大きすぎてナイフにぶつかりやすい場合。したがって、実際の車のアーク、複数のナイフ処理の必要性、最初はマージンの大部分になり、最後に車は目的のアークになります。以下に、カーアークの一般的な処理ルートを紹介します。
カーアークのステップカットルートです。つまり、はしごに入る最初のラフカー、弧から出た最後のナイフファインカーです。この方法では、各刃の量apを決定した後、粗旋盤の最終刃距離S、つまり円弧と直線の交点を正確に計算する必要があります。この方法の切削距離は短くなりますが、数値計算はより複雑になります。
カーアークの同心アーク切断ルートです。つまり、異なる半径の円を使用して回転し、最後に目的の円弧処理を行います。この方法では、各切削apを決定した後、90°円弧の始点と終点の座標を簡単に決定できます。数値計算が簡単で、プログラミングに便利です。ただし、図2-3Bに従って処理すると、空の移動時間が長くなります。
ターニングアークのターニングコーン方式の切断ルートです。つまり、最初にコーン、次にカーアークです。ただし、カーコーンの始点と終点が適切に決定されていないと、コーンの表面が損傷したり、マージンが大きくなりすぎたりする可能性があることに注意してください。決定方法を図2-4に示します。OCを接続してDで円弧を交差させ、円弧の接線ABをDに通します。幾何学的関係CD = OC-od = -r = 0.414rによると、これは円錐を回転させるときの最大切削許容値です。 、コーンを回すとき、加工ルートはABラインを超えることはできません。AC = BC = 0.586rは、図に示されている関係から取得できます。これにより、コーンを出るときの開始点と終了点を決定できます。Rが大きすぎない場合は、AC = BC = 0.5rを選択します。
3.ねじ山時の軸送り距離の解析
ねじ切りの場合、ねじ山方向に沿ったカッター送りは、ワークのスピンドル回転に厳密に比例する必要があります。停止状態から指定された送り速度まで、または指定された送り速度からゼロまでのドライブシステムを考慮すると、処理スレッドの長さを保証することに加えて、軸方向の送り処理ルートの長さに沿った遷移プロセスを追加する必要があります図2-5に示すように、距離のデルタ1(2〜5 mm)ツールの導入と距離の切り出しにおけるデルタ2(1〜2 mm)へ。これにより、ねじ切り時に、速度の上昇が完了した後に工具がワークピースに接触し、ツールがワークピースを離れた後に速度が低下します。
4.連続フライス盤の輪郭、特にアークの処理では、接合部での繰り返し処理を避けるために、切削工具を切り抜くように配置するように注意する必要があります。
そうしないと、明らかな境界トレースが発生します。図2-6に示すように、円弧補間方法の外側でのフライス盤では、接線点ではなく円全体が処理された後、接線から周辺フライス盤に工具を配置し、工具の移動距離を調整します。切削工具の補正をキャンセルしないように、接線方向に沿った方が最適です。切削工具とワーク表面が衝突し、ワークが削られます。内弧をフライス盤加工する場合も、図2-7に示すように、接線切断の原理に従い、遷移円弧を切断および切断するように調整する必要があります。
5.高位置精度での穴加工ルートの解析
高精度の穴システム処理の位置精度については、穴処理シーケンスの配置に特別な注意を払う必要があります。配置は適切ではなく、座標軸に沿って逆ギャップをもたらす可能性があり、位置精度に直接影響します。図2-8に示すように、図Aは部品の図面です。パーツで処理される同じサイズの6つの穴には2つの処理ルートがあります。図1に示す経路に従って処理する場合。B、穴5、6の位置決め方向が穴1、2、3、4と反対であるため、Y方向の逆クリアランスは位置決め誤差を大きくし、穴5、6などの位置決め精度に影響を与えます。穴。図Cに示すルートに従って、4つの穴の加工が終了した後、点Pまで距離を上に移動します。その後、プロセス5と6の穴に戻ります。このようにして、方向が一定になり、逆クリアランスの導入を回避でき、5穴と6穴およびその他の穴の位置精度を向上させることができます。
6.CNCフライス盤の加工ルートの分析
CNCフライス盤表面、一般的に使用されるボールヘッドナイフの「ラインカット法」による加工。いわゆるラインカット法とは、切削工具を指し、接点トラックの輪郭のパーツをラインごとに配置し、パーツの加工精度の要件に応じてライン間の距離を決定します。境界が開いた表面加工の場合、2つの加工ルートを採用できます。図2-9に示すように、エンジンの大型ブレードの場合、図2-9Aに示す処理方式を採用すると、ブレードポイントが直線に沿って処理されるたびに、カッターポイントの計算が簡単になります。そしてプログラムは少ないです。処理プロセスは、バスバーの真直度を正確に保証できる線織面の形成に準拠しています。図1に示すような加工方式の場合。2-9Bを採用、このような部品のデータに適合しており、後処理検査に便利です。刃の形状の精度は高いですが、手順はたくさんあります。湾曲部分の境界が開いているため、他の表面制限がなく、湾曲した境界が伸びることがあります。ボールヘッドナイフは境界の外側から処理を開始する必要があります。
上記の一般的な処理ルートでのCNC加工のいくつかの例、実際の生産、部品の特定の構造特性に従って決定するCNC加工ルート、包括的な考慮事項、柔軟な使用。CNC加工ルートを決定する一般原則は、部品の加工精度と表面品質を確保した状態で生産性を向上させるために、CNC加工ルートを可能な限り短くすることです。