
航空宇宙は、製造業の主要なサポートです。 開発から完成品まで、航空宇宙産業の製造が最も重要な役割を果たします。 どの航空宇宙製造技術が使用されていますか? 航空宇宙部品の適切な材料を見つける方法は? この記事では、航空宇宙の一般的な製造方法、材料、検査、品質管理について説明します。
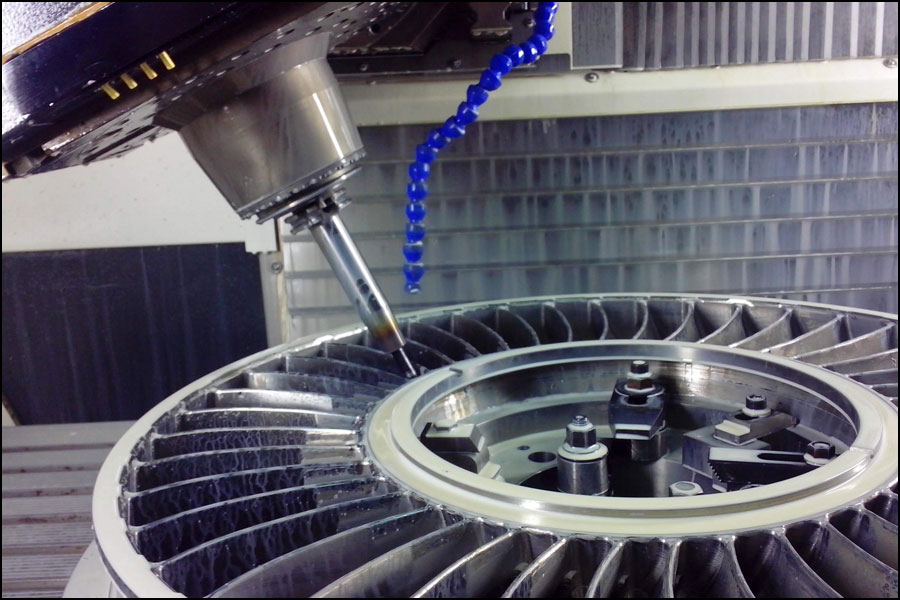
航空宇宙製造技術
航空宇宙製造技術
部品設計が承認されると、生産を開始できます。製造プロセスは、生産量と必要なリードタイムに基づいて選択する必要があります。
積層造形
アディティブマニュファクチャリング(AM)とは、仮想3次元コンピューターモデルから、通常は層状に材料を追加することにより、物理コンポーネントを作成するプロセスを指します。一般的な積層造形技術には、3D印刷、シート積層、材料押し出しなどがあります。航空宇宙は、積層造形の先駆的なセクターの1つであり、このセクターの特徴は、バッチサイズが小さく、製造元固有の適応が特徴です。アディティブマニュファクチャリングは、独自の形状と格子構造を作るために使用でき、重量を減らし、熱を放散するのに役立ちます。また、航空宇宙製品の開発傾向に沿って、高度な材料で半中空の部品を作成し、強度を維持しながら重量を減らす優れた手法でもあります。アディティブマニュファクチャリングは、少量で高価値の生産ニーズのある航空宇宙部品向けに設計されています。
CNC加工
飛行機の精度は非常に重要であり、機体から小さな部品まで、CNC機械加工サービスは特定の航空宇宙部品およびツールを正確に生産できます。たとえば、CNCマシンは、エンジン内部にほとんど見えない部分を作成したり、飛行機の翼を非常に正確に変更して、翼が効率的に機能するようにすることができます。 CNCMACHINING.JPは、航空宇宙製品のエンジニアリングおよび機械加工サービスで認められているCNC製造会社です。見積、製造、試験、仕上げなどのワンストップサービスを提供し、お客様固有の困難なニーズに対応します。訓練を受けた技術者は、各CNC航空宇宙加工プロセスを監視して、品質と精度を確認します。 CNC機械加工は、完成した部品に追加の仕上げサービスが必要な場合、または正確な寸法と良好な表面仕上げのニーズに最適です。
航空宇宙部品の材料
航空機構造の独自の機能と要件に基づいて、軽量素材の複雑な部品が推奨されるため、業界に適した素材の種類を決定します。現代の技術の発展に伴い、新しい複合材料や合金などのより過酷な環境条件に耐えることができる、より軽量で空気力学的な面を作成する代替材料がますます増えています。いくつかの人気のある航空宇宙材料がここにリストされています。
- –ステンレス鋼:ステンレス鋼17-4 PHは、その高強度、優れた耐食性、および最高600°Fの温度での優れた機械的特性により、航空宇宙CNC機械加工または3D印刷で広く使用されています。
- –アルミニウム:アルミニウムは航空機ハウジングおよびブラケットに最適なオプションです。強度と重量の比率が高く、機械加工が容易でコスト効率が高いため、高荷重をサポートします。ほぼ1世紀の間、航空宇宙産業は部品を作るためにアルミニウムに依存していました。航空宇宙で使用される最も一般的なアルミニウム合金は7075アルミニウムで、鋼と同じくらいの強度があり、優れた疲労強度と平均的な機械加工性を備えています。
- –チタン:チタンは、軽量、高強度、優れた耐食性、耐熱性の組み合わせです。今日の民間航空機は、以前に設計された航空機よりもはるかに多くのチタンを使用しています。チタン製の部品やコンポーネントは通常、航空機のジェットエンジンや宇宙船などの飛行機の固定要素、機体、着陸装置の製造に使用されます。また、エンジンの部品には、ディスク、ブレード、シャフト、ケーシングなどがあります。チタン6AL-4V合金は航空機で使用されるすべての合金のほぼ50%を占めます。重量と強度の比率が高いことを利用して、チタン製の航空宇宙部品は燃料消費量が少なくなっています。
- –インコネル:ロケットエンジンコンポーネントやその他の高温耐性が必要な航空宇宙用途の3Dプリントで通常使用されるニッケルクロム超合金です。
- –複合材料:炭素繊維、ガラス、アラミド強化エポキシなどの複合材料は軽量で、燃料効率の高い航空機の作成に使用できます。彼らはまた、翼を作るのに適した高い抵抗と疲労に耐えることができます。
航空宇宙検査および品質管理
航空宇宙産業の品質管理に関しては、製造工程の後に、特に航空宇宙部品の検査が必要です。それぞれの小さな部品は、特定の品質基準と認証に準拠している必要があります。航空宇宙の最も重要な認定はAS9100Dです。 AS9100Dは、ISO 9000 / ISO 9001規格から採用された航空宇宙業界の品質基準です。
生産中の品質管理方法は?複数の品質管理方法を適用できます。たとえば、部品構築中のリアルタイムフィードバックや調整のための現場モニタリングなどです。作業が完了すると、コンポーネントは座標測定機による破壊的または非破壊的な試験を受け、使用できます。タッチプローブまたはレーザー、X線またはその他のスキャン技術を使用して、寸法精度をチェックします。さらに、材料の各バッチおよび部品のバッチの完全な追跡可能性により、すべてのアイテムのソースと軌道を使用して、問題をより簡単に見つけることができます。