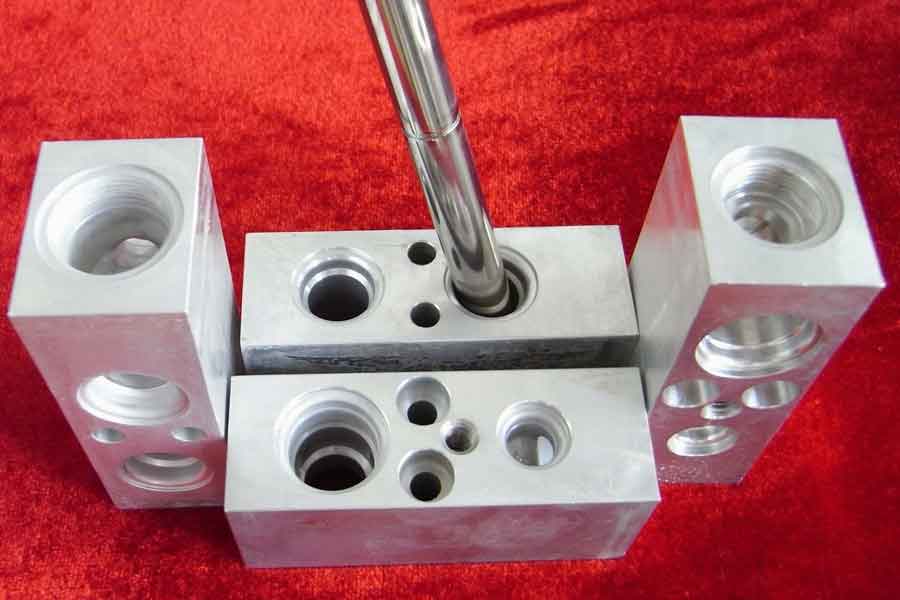
金属切削のプロセスは、しばしばバリの形成を伴います。バリの存在は、ワークの加工精度や表面品質を低下させるだけでなく、製品の性能に影響を与え、時には事故を引き起こすことさえあります。結果として生じるバリの問題は、通常、バリ取りプロセスによって解決されます。バリ取りは非生産的なプロセスであり、製品のコストが増加し、製品の生産サイクルが長くなるだけでなく、バリの除去が不適切な場合、製品全体が廃棄され、経済的損失が発生します。
この論文では、エンドミルバリの形成に影響を与える主な要因を体系的に分析し、構造設計から製造までの全プロセスからバリを低減および制御する方法と手法について説明します。 I.切削動作に応じたエンドミリングのバリの主な形態–工具刃先バリ分類システム。エンドミリングの過程で発生するバリは、主にバリの方向の両側に主エッジがあり、切削方向バリ、切削方向バリからのボトムカット、バリ方向からのカットイン、カットアウトの5つの形状。
エンドミルで形成されるバリ一般的に、下側切削方向のバリは、他のバリに比べてサイズが大きく、除去が困難です。そのため、本論文では、下端の切削方向のバリを主な研究対象としている。エンドミルでの下端の切削方向のバリの大きさや形状により、タイプIバリ(大きいサイズ、取り外しが難しい、除去コストが高い)、タイプIIバリの3種類に分類できます。 (小さいサイズ、取り外しできない、または簡単に取り外せない)およびタイプIIIのバリ、つまりネガティブバリ
バリの形成は、非常に複雑な材料変形プロセスです。バリの形成は、ワークピースの材料特性、形状、表面処理、工具形状、工具切削経路、工具摩耗、切削パラメータ、クーラントの使用など、多くの要因によって直接影響を受けます。エンドミルバリの影響要因のブロック図です。特定のフライス盤条件下では、エンドミルフライス盤の形状とサイズはさまざまな要因の包括的な効果に依存しますが、さまざまな要因がバリの形成にさまざまな影響を及ぼします。
1.工具の出入り
一般に、工具をワークピースから回転させたときに発生するバリは、工具をワークピースに回転させたときに発生するバリよりも大きくなります。
2.平面カット角度
平面切削角度は、下切削方向のバリの形成に大きな影響を与えます。平面切削角度は、刃先が回転するときのフライスの軸に垂直な平面内の刃先上の点での切削速度の方向(工具速度と送り速度のベクトルの組み合わせ)の間の角度として定義されます。ワークの端子面とワークの端子面の方向から。ワーク端子の方向は、工具挿入点から工具抽出点までです。図1に示すように。 5、ψは平面の接線角度であり、その範囲は0°<ψ≤180°です。実験結果は、バリの高さが切削深さとともに変化すること、すなわち、バリが切削深さの増加とともにタイプIのバリからタイプIIのバリに変化することを示している。タイプIIのバリが発生する最小のミリング深さは、通常、限界切削深さと呼ばれ、DCRで示されます。
平面切削角度が大きいほど、境界の切削深さが深くなります。平面切削角度が120°より大きい場合、タイプIバリのサイズが大きくなり、タイプIIバリへの境界遷移の切削深さも大きくなります。したがって、小さな平面切断角度は、タイプIIバリの生成を助長します。これは、ψが小さいほど、端子面の支持剛性が高くなり、バリの形成が困難になるためです。図5から、送り速度の大きさと方向が合成速度Vの大きさと方向に、したがって平面切断角度とバリの形成に一定の影響を与えることがわかります。したがって、送り速度と出口エッジオフセット角度αが大きいほど、ψは小さくなり、大きなバリの形成を抑制しやすくなります。
3.ヒント終了順序EOS
エンドミル加工では、バリのサイズは工具先端の出口順序に大きく依存します。点Aは二次刃先の点、点Cは主刃先の点、点Bは先端です。先端が鋭いと仮定します。つまり、先端の半径に関係ありません。 BC側が先にワークから出て、AB側が後でワークから出ると、切りくずは加工面にヒンジで固定され、フライス盤が進むにつれて切りくずがワークから押し出され、より大きな下端カットが形成されます。切削方向バリを出します。 a-B側が最初にワークピースから出て、B-C側が後でワークピースから出る場合、チップは遷移面にヒンジで固定されてワークピースから切り出され、切断方向のバリから切り出された小さな下端が形成されます。結果は次のことを示しています。
- バリサイズが大きくなる工具先端出口シーケンスはABC / BAC / ACB / BCA / CAB / CBAです。
- EOSによる結果は同じですが、同じ出口順序で、プラスチック材料のバリサイズは脆性材料のバリサイズよりも大きくなります。
工具先端の出口シーケンスは、工具の形状だけでなく、送り、フライス深さ、ワークの形状、切削条件などにも関係します。これらは、さまざまな要因によるバリの形成の影響を受けます。
4.その他の要因
- フライス盤のパラメータ、フライス盤の温度、切削環境、およびバリの形成に関するその他の要因も、一定の影響を及ぼします。送り速度、フライス盤の深さ、および平面切削角度理論とツールによるその他の影響などの主な要因のいくつかポイント出口順序EOS理論が反映されていますが、これは詳細ではありません。
- 被削材の塑性が良いほど、I型バリが発生しやすくなります。脆性材料のエンドミル加工の過程で、送りまたは平面切削角度が大きい場合、タイプIIIのバリ(欠陥)の形成を助長します。
- ワークの端面と加工面との角度が直角よりも大きい場合、端面の支持剛性が向上するため、バリの発生を抑えることができます。
- フライス盤の使用は、工具寿命の延長、工具摩耗の低減、フライス盤プロセスの潤滑、そしてバリのサイズの縮小に役立ちます。
- 工具の摩耗はバリの形成に大きな影響を及ぼします。工具がある程度摩耗すると、工具の出口方向のバリのサイズだけでなく、工具先端の弧も大きくなります。切削工具の入口方向にバリがあります。そのメカニズムはさらに研究する必要があります。
- 工具材料などの他の要因もバリの形成に一定の影響を及ぼします。同じ切削条件の下で、ダイヤモンド工具は他の工具よりもバリの形成を抑制するのに有益です。
エンドミルバリの形成は、特定のフライス盤プロセスだけでなく、ワークピースの構造、工具の形状、およびその他の要因にも関連する多くの要因の影響を受けます。エンドミルのバリを低減するには、多くの側面からバリの発生を制御および低減する必要があります。
01.合理的な構造設計
バリの発生は、ワークの構造に大きく影響されます。ワークの構造が異なると、ワークのエッジのバリの形状やサイズも大きく異なります。ワークピースの材料と表面処理が事前に決定されている場合、ワークピースの形状とエッジは、バリの形成を決定する上で重要な要素です。
02.適切な処理シーケンス
加工順序は、エンドミルバリの形状とサイズにも一定の影響を及ぼします。バリ取りの量と関連費用は、バリの形状とサイズによって異なります。したがって、適切な処理シーケンスを選択することは、バリ取りのコストを削減するための効果的な方法です。
平面を最初に穴あけしてからフライス盤にすると、穴の周囲に大きなカットフライス盤のバリが発生しやすくなります。平面が最初にフライス盤で次に穴あけを行う場合、穴の周囲には小さな穴あけカットバリしかありません。上面をフライス盤し、次に凹面プロファイルをフライス盤することによって形成されるバリは、凹面プロファイルをフライス盤し、次に平面をフライス盤することによって形成されるものよりもサイズが小さい。
03.ツールの終了を避ける
工具の引き抜きは、カットアウト方向のバリ形成の主な要因であるため、工具の引き抜きを回避することは、バリの形成を回避するための効果的な方法です。一般に、フライスで発生するバリは、ワークを回転させると大きくなり、フライスで発生するバリは小さくなります。したがって、フライスは機械加工の過程で可能な限り避ける必要があります。
04.適切なルートを選択してください
以前の分析によると、平面カット角度が特定の値よりも小さい場合、バリのサイズは小さくなります。平面カット角度は、ミリング幅、送り速度(大きさと方向)、回転速度(大きさと方向)を変えることで変更できます。したがって、適切な切断ルートを選択することにより、タイプIのバリの発生を回避できます。
従来のジグザグ切削ルートと図の網掛け部分は、より大きなサイズの切削方向バリが発生する可能性のある部分を示しています。切削バリの発生を回避する改良された切削ルートを使用します。供給ラインよりもパートbの供給ラインですが。
05.適切なフライス盤パラメータを選択します
エンドミルパラメータ(1歯あたりの送り、エンドミル幅、エンドミル深さ、カッターの幾何学的角度など)は、バリの形成に一定の影響を及ぼします。エンドミリングバリの形成は多くの要因の影響を受けますが、その主な要因は次のとおりです。工具の出口/入口、平面切削角度、工具先端の出口シーケンス、フライス盤のパラメータなど。バリの最終的な形状とサイズは、要因の組み合わせ。本稿では、構造設計、ワークの加工工程の配置、フライス盤工程の投入量、切削工具の選定、フライス盤バリを分析します。主な影響要因は、カッタールートの制御方法を提唱し、適切な加工を選択します。バリのフライス盤の技術、プロセス、方法を抑制または低減するシーケンスおよび構造設計の改善方法。これは、バリのサイズを積極的に制御し、製品の品質を向上させ、コストを削減し、フライス盤の生産サイクルを短縮するための実行可能な技術スキームを提供します。
当社の製品にご興味がおありでしたら、図面と一緒にご要望をメールでお送りください。私たちはあなたに最も有利な見積もりを与えることを非常に嬉しく思います。もしそうなら、私たちの電子メールは次のとおりです:[email protected]、私たちに迅速かつ簡単に電子メールを送信するには、左側の電子メールアドレスをクリックしてください