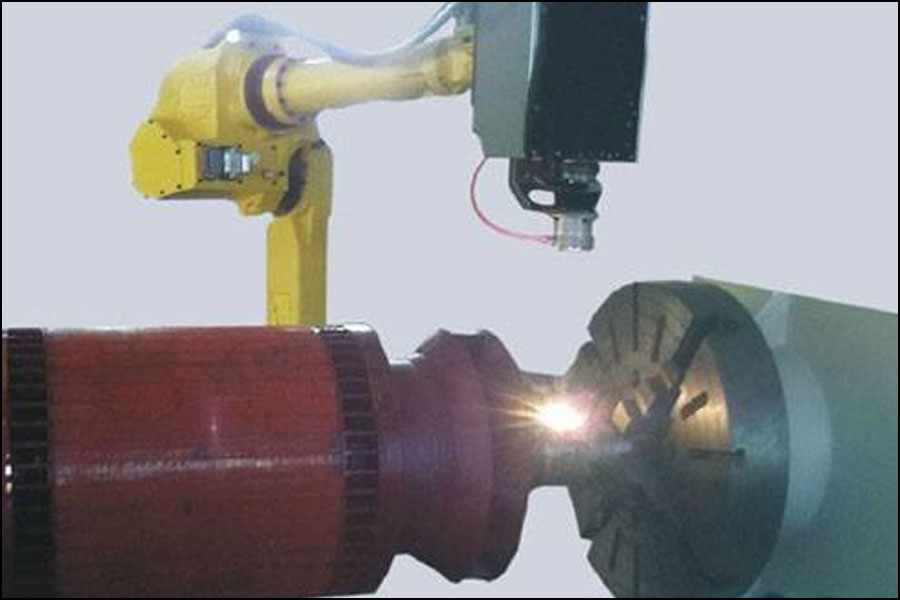
セラミックス基複合材料(CMC)は航空エンジンや高速航空機での応用を拡大していますが、高い信頼性と高精度の加工に挑戦しています。CMCの高硬度と損傷しやすい特性は加工速度が遅く、工具を絶えず交換することと材料性能に悪影響を与え、部品規格の要求を満足できないことをもたらす。レーザ技術は加工効率を向上させ,工具の繰返しコストを終結させる解決策である。しかし,レーザで発生した熱は材料中に散逸し,マイクロクラックと材料の変性を生じる可能性がある。レーザーはビームの焦点で切削し,V字切り欠きをもたらし,公差の正確な制御に影響する。スウェーデンが開発したレーザーマイクロジェット技術は上記の課題を解決するための最良の方法を提供しています。2017年、米ゼネラル・エレクトリック航空グループは、米国ノースカロライナ州のアシュビルにあるCMCエンジン部品生産工場にレーザーマイクロジェット技術を配置し、LEAPエンジンのCMCカバーリング上の穴を加工した。生産検証プロセスは,この技術は高効率で孔直径の高精度を維持するのに役立ち,マイクロジェットは2分間で穴あけができ,従来の加工は1時間の穴あけが必要であることを示した。
一、レーザー水噴流の加工技術原理と優勢
全内部反射原理に基づいて、レーザマイクロジェット技術は、水噴流に完全に含まれるレーザビームを生成し、レーザビームはより低い密度の媒質を有する空気−水界面で反射し(原理的には光ファイバと似ている)、ノズルからワークまでの狭い直線経路に沿って伝播し、エネルギーが内壁を横切ることなく、水は切削領域を冷却し、切欠きから切欠きを除去する。従来のレーザと比較して,この技術は材料を燃焼させたり熱を退化させたりせず,より少ないバリを発生させることで,表面をより滑らかにすることができ,直辺切削とより高い精度を実現できる。
レーザパルスの持続時間はナノ秒単位で,各レーザパルスに対して,生成したプラズマは水を押し上げることを体得し,それにより効率的なアブレーションを実現した。パルスが終わると,プラズマは崩壊し,その後表面を水できれいにし,熱を散逸する。水噴流はまた、レーザ集束による複雑さとプロセス変化を維持する必要がある乾式レーザシステムを除去し、焦点問題を心配することなく、厚いまたは非平面の部品を切断することができる。この技術を用いて作製した円筒形レーザは,完全に平行な壁を生成でき,切欠き幅がコンパクトである。
二、ゼネラル・エレクトリック航空グループCMCレーザー水噴流加工工程の詳細
1.MCレーザーマイクロジェットシステムとプロセス
シノワール社のCMCレーザーマイクロジェット(LCS)システムでは、加圧水室を介してレーザービームがノズルに集束されている。レーザは工業的に一般的な固体ネオジムドープイットリウムアルミニウムガーネットレーザであり、毎秒パルスは10000回、電力は10から200ワット、波長は1064(赤外)、532または355ナノメートルである。噴流は濾過された脱イオン水で、わずかに発糸の細い(直径50から70ミクロン)しかなく、200から650巴の低圧で使用されています。
レーザヘッド自体に対して,ビームはそれを通過するのではなく,ある角度で境界に接近しなければならないという挑戦である。水噴流もビームの脱出を防ぐために高度に安定しなければならない。シノワール社の国際特許は、ガスで密封された液体ジェットをどのように使用して乱流の形成を防ぐかを示しています。サファイアやダイヤモンドからなるノズルは耐久性があり、特殊な形状はガスと水が適切に相互作用することを確保する。低圧で投射した純水、脱イオン水、フィルター水はビームを包み、水流の悪影響によるリスクを制限する。このような水の流れは光ファイバケーブルと非常に似ています。
レーザマイクロジェットシステムのノズルの直径範囲は25から120ミクロンで,低圧水の流量はこれより15%小さい。内部連続反射ビームのエネルギーを利用して,水の流れは本質的に完全な円柱羽根となり,その軌跡には完全な直壁を残した。水の流れをガイドしない場合,レーザビームは自然のテーパであり,源から特定の焦点に狭くして再び外に向けて展開する。このため、切削深さと焦点位置を厳しく制御し、切削に必要でない勾配が発生しないようにしなければならず、水の添加はこの問題を解消した。シノワール社が提供したデータによれば、水噴流とその内部のレーザーが分離を開始する前に、ノズル径の1000倍の距離(最大動作範囲は100ミリ)まで水噴流を投射することができる。切欠き幅はノズル直径と緊密に一致し,精度と繰返しはミクロン単位である。
2.ゼネラル・エレクトリック航空グループCMC部品加工プロセス
ゼネラル・エレクトリック航空グループCMC部品加工ラインの各工作機械は真空チャック付きの3 Rインターフェイスを使用しています。できるだけ生産をシングルフローに近づけるようにしています。3 Rインターフェースはワーク治具システムに関連しています。加工ラインには様々な部品を挟み込むことができます。ワークは接着剤を通してインターフェースに固定されています。ロボットに挟まれて、自動化加工ラインを通して、マイクロジェット加工機を含みます。各駅には別途の設置作業が必要ではありません。加工ラインの最後のステップは非破壊検査であり、GEのコンピュータX線断層スキャン(CT)機を使用する。部品ごとに検査します。スキャン時間は15分です。完成時間は30分です。データ評価も含まれています。
日本の牧野工作機械会社(Makino)と西ノワール社が共同で開発したレーザーマイクロジェット機は「工場4.0」の機能を備えています。レーザーパワー計、測位センサー、自動噴流角度補正はレーザーマイクロジェットシステムに集積されています。このシステムは実際に非常に柔軟で、独立したシステムとして部品生産に集積しやすく、あるいは全自動生産ラインの一部として、オペレーターによる大量生産を実現する必要がない。工業用インターネットは工作機械の重要な特徴であり、工場の中の工作機械から屋上まで室内イーサネットケーブルを敷いて、工場のデータベースシステムに接続して、「銀管ネットワーク」と呼ばれています。このため、加工指標とCTスキャンなどは各CMC部品のデジタル手がかりに記録され、技術者のプロセスの最適化を助けるために分析されます。
三、レーザー水噴流加工技術の応用見通しが広いです。
1.炭素繊維複合材料の加工
レーザマイクロジェット技術は,非常に一定の1立方メートル/分のアブレーション速度に基づいて,1インチ厚のCMC積層板を高速に切断できる。CMCに加え、炭素繊維強化プラスチック(CFRP)にも適用され、厚み2.6 mmのCFRP積層板に直径3ミリの穴を生成し、速度は1440ミリ/分と高い。従来のレーザを使用すると、熱がドリルカット速度を低下させなければならないため、従来のフライスは同様の速度に達することができますが、刃物を交換する必要があるため、運営コストがより高いです。
シノワールは2018年に5軸CNC LCS 305システムを導入し、高精度の3 D切削が得意で、小型CMC部品にとても適していますが、大型CFRP部品には適していません。このため、西ノワはまたレーザーマイクロジェットシステムを龍門工作機械に集積し、2メートル×3メートル以上の部品を加工することができます。このシステムはロボットと統合しやすく、プログラミングしやすく、加工能力を拡大します。2 D切削に対しては、マイクロジェットソフトウェアはCADファイルを工作機械コードに変換し、検証すれば、操作者はボタンを押すだけで、旋盤は切削プログラムを実行します。3 D切削については、CADファイルから必要な3 Dデータを抽出し、マイクロジェットソフトウェアにフォーマットする。
2.金属加工
テーパなし、熱影響なし、材料なし堆積の三つの利点は、レーザ水噴流を多機能性にし、ほとんどの材料を複雑な特徴に切断することができ、このプロセスは乾式レーザ切断だけではなく、多くの他のプロセスに取って代わることができ、金属加工にも使える。
西ノワールのLCSシリーズの工作機械は小型金属を精密に加工できます。LCS 300の最大作業範囲は300ミリ×300ミリです。牧野工作機械と西ノワール社が共同で開発した五軸MCS 500は500ミリ×400ミリに達することができます。MCSシリーズは牧野工作機械自身のフライスと電気スパーク加工(EDM)製品ラインを補充しました。牧野工作機械はいわゆる「ハイブリッド加工ユニット」を販売しています。MCS 500と牧野EDBVの電気スパーク加工ドリルマシンを含んでいます。タービンの葉の中にある冷却穴と中空内部のガイド羽根の部品をドリルで削って、ユーザーが一番良い成果を持つ完全な羽根を開発できます。
これらのタービンの葉とガイド羽根は通常セラミックの断熱層を塗って、高温を防ぐのに役立ちます。しかし,これらの被覆は導電性ではなく,電気スパーク加工は導電性材料にのみ適用される。そのため、メーカーは通常、コーティング前に穴あけを電気スパーク加工する。さらに厄介なことに、現在は冷却孔がますます複雑になり、設計者はテーパ、四角形、または他の非円形開口を持つ拡散器孔を多く採用している。これらの開口は常に外部拡散器の形状を中心としているわけではない。電気スパーク加工のみを使用して、メーカーは通常、コーティングの厚さに適合するように規格より大きな特徴を加工することを選択しています。いくつかの特徴は後に手動で除去する必要があります。機械間のデータ転送機能を備えた自動化ハイブリッド加工ユニットは、このプロセスを簡略化した。初期被覆の浸透と拡散器形状の加工は,レーザ水噴流により行うことができ,一方,大部分の孔を電気スパーク加工に残した。
穴が十分浅いと,レーザ水噴流は全幾何学形状を完全に加工でき,電気スパーク加工よりも高速になり得る。しかし,ある深さでは,水流が分解し始め,電気スパーク加工がより速くなり,唯一の選択であった。EDBV工作機械は他の長所も持っています。例えば、発電機はダイナミックフィードバック回路を持っています。パイプ式電極の位置を感知し、必要に応じてインクリメントを増加させて「空気切削」を最小化します。特に、高い接合角度の時に。工作機械はまた、電極が一秒または0.04インチ(約1ミリ)の深さで内部空洞を突破して速度を維持し、気流の火花を乱させる恐れがあるということを感知することができます。牧野工作機械の専用曲げガイドには、ターボエンジン穴以外の加工にも役立つ機能があります。したがって、これらのアプリケーションでは両方のプロセスが一席の場所を占めています。どの穴が与えられた仕事に最適なのかはメーカーによって決定されます。両方を一つのユニットに結合することにより、二つのプロセスの作動負荷をバランスさせ、それによって品質と生産性を任意の孤立システムのレベルを超えて向上させることができる。
レーザは航空製造においてますます重要な位置を占めており,レーザ水噴流プロセスはさらにこの点を説明した。レーザ水噴流はセラミックベースの複合材料と炭素繊維複合材料の加工効率と完成品品質を向上させることができる。積層ファイバ構造の存在により,金属切削や穴あけにしばしば存在するバリよりも,これらの複合材料を加工する熱影響は,より複雑な層状と欠陥をもたらすことが多い。炭素繊維-チタン合金の積層ドリルにおいては、軌道加工が大幅に応用されており、現在はCMCとCFRPの穴あけにおいてもレーザー水噴流がステージに登場しており、航空複合材料応用の拡大に伴い、今後も同様の技術が続々と出現していくと信じています。