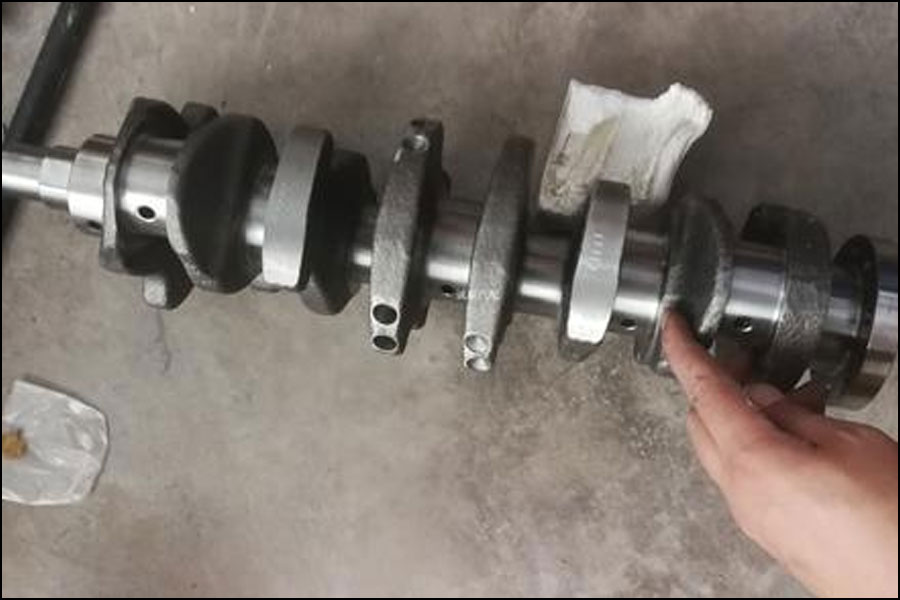
自動車の製造には、精度の向上、コストの削減、効率の向上が求められており、クランクシャフトなどの非常に複雑なワークピースの製造にも影響を及ぼします。さらに、高度に統合されたエンジンの出力特性がますます増大するため、高圧縮エンジンの比出力は増加し続けており、多くのメーカーはそのようなコンポーネントをより安定して正確に製造する必要があります。このエンジンのコアコンポーネントは、理論的にはどこでも完璧な表面を持っています。しかし、これは高い引張強度を備えたクランクシャフトにとって非常に厳しい要件です。
全体的な処理技術のペースを改善しました
ワークピースは内部応力を解放し、加工プロセス中にワークピースのサイズを変化させるため、この包括的な研削プロセスは依然として非常に時間がかかります。通常、この種の処理は粗粉砕と微粉砕に分ける必要があります。従来の研削方法では、フィレットとショルダーの間の移行部分が激しい工具負荷を引き起こすため、砥石の摩耗が大きくなります。
新しいソリューションを使用して、深刻な砥石の摩耗の問題を改善し、プロセスの分割によって引き起こされるサイクル時間の延長の問題を最適化するにはどうすればよいですか? PTJの研削専門家によって提案された斜め研削法は、メインジャーナルとクランクシャフトの接続ロッドネックでの困難な研削作業をより迅速かつ費用効果の高い方法で完了することができる適切なソリューションです。メインジャーナルは、多段階の機械加工ステップ(粗加工、仕上げから超仕上げ、滑らかな研削まで)を通じて完全な平行面を得ることができますが、粗肩加工ははるかに少ない加工ステップで済みます。
最も重要なことは、加工中にワークピースが特定の方法で変形し、それが研削中に発生する力に影響を与えることです。具体的には、ジャーナルに丸角加工を施すことで、シャフトの変形を防ぎ、研削力を大幅に低減します。一方、肩の加工工程では、軸方向の変形はごくわずかです。逆に、接触圧力が高いと過熱する傾向があるため、砥石の摩耗が早くなります。
速度と動きの正確な制御
さまざまな加工条件に対応するため、斜め研削に新しい総合研削工程を採用しています。研削速度と軸の動きは互いに独立して制御され、各サブルーチンは正確に制御されます。一方、研削の専門家はついにクランクシャフトの加工時間を大幅に短縮することに成功しました。
たとえば、ロッドジャーナル、メインジャーナル、スラストベアリングを接続するための事前研削時間は、現在頻繁に使用されている2カット研削法よりも約3分の1速くなります。 7つのジャーナルを備えたクランクシャフトの研削プロセスは35分かかりましたが、現在は20分しかかかりません。一方、砥石の丸い角の装填方法が異なるため、工具コストも削減されました。各部品を加工する際の工具損失は約3分の1に減少します。
自動車生産のモデル
PTJのイノベーションは現在、主に商用車や貨物車の生産に使用されており、この分野ではクランクシャフトの品質要件が特に高くなっています。トラックエンジンは非常に長く動作するため、クランクシャフトは非常に安定している必要があります。
しかし、乗用車の場合、ジャーナル表面とフィレットを組み合わせて研磨することもますます重要になっています。多くの高性能エンジンでは、クランクシャフトに作用する力も増加しています。この場合、細部に至るまで包括的な粉砕プロセスを使用する必要があります。この斜め研削に基づいて、PTJはすでにこの効率的な技術を今日適用することができます。 PTJエンジニアは、この競争上の優位性を他のコンポーネントにも適用したいと考えています。たとえば、カムシャフトとギアシャフトも同様の方法で斜め研削プロセスの恩恵を受けることができます。