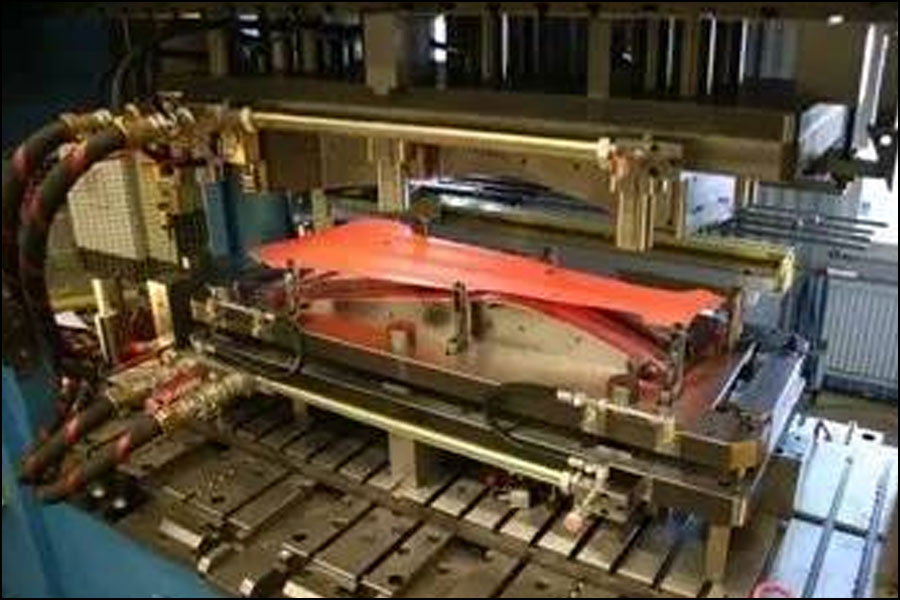
深絞りは、板金をカップやボックスに成形するための構造として広く使用されている製造方法です。板金深絞り製品には、調理鍋やフライパン、容器、流し台、パネルやガスタンクなどの自動車部品があります。この方法は描画と呼ばれることもあり、変形の大きなフェーズと混同しないでください。
深絞りプロセス
深い板金引抜はパンチとダイで行われます。パンチは、一度描画されると、パーツに必要な基本形状です。ダイキャビティはパンチと一致し、少し広く、通過できるようにクリアランスがあります。この構成は、板金切断のアクティビティに相当します。ダイトップとパンチ面の間の横方向の距離は、切削の場合と同様にクリアランスです。板金ジョブピースは、ブランクと呼ばれるダイ開口部の上に配置されます。パンチを囲むブランクホルダーは、ブランクの表面全体(顕微鏡下の領域を除く)に圧力をかけ、板金ジョブをダイに対して平らに保持します。パンチがブランクに移動しています。パンチは、ジョブに接触した後、板金をダイキャビティに押し込み、その形状を形成します。
機器は、板金の深遠な描画手順のために、ブランクホルダー用とパンチ用の2つのアクションを必要とします。生産部門では、機械プレスと油圧プレスの両方が使用されています。通常、ブランクホルダーとパンチの動作は油圧プレスによって個別に制御できますが、機械プレスは高速です。パンチとダイの材料は、一般に、深遠な伸線用の工具鋼と鉄です。ただし、パンチおよびダイ製品の種類は、プラスチックから炭化物までさまざまです。パーツは通常、毎秒4〜12インチの速度で描画されます。
深絞り練習
深絞りは、材料の流れと力の複雑な分布を伴う板金成形のプロセスです。上記のように、パンチとダイの構成は、パンチングやブランキングなどの板金切断手順にいくらか匹敵します。深絞りのパンチにより、2つの主要な変数が、金属をせん断する代わりにダイキャビティに引き込みます。
ダイコーナー半径とパンチコーナー半径は、深絞りの重要な要素です。板金を切断するとき、パンチとダイのコーナーに半径はありません。パンチでは、鋭いエッジと死ぬことでそれがカットされます。エッジの半径により、力の分布が変化し、金属が半径を通ってダイキャビティに流れ込みます。パンチが板金を引き抜いて切断しない原因となる他の重要な要因は、クリアランス量です。切削加工のクリアランスは比較的低く、一般に板金の厚さの3%から8%です。深遠な図面の作成では、クリアランスが小さすぎると、半径に関係なくシートがスライスまたは貫通される(うまくいかない)場合があります。深絞りクリアランスはシートの厚さよりも高く、通常、クリアランス値はシートの厚さの107%から115%です。
板金の厚さは、多くの計算で連続していると想定されています。ただし、関係する力により、一部のフィールドでは密度に変化があります。成形品の側壁を成形するには、材料がブランクの外周からダイコーナー半径を通って流れ、次にパンチ方向に直接流れる必要があります。真っ直ぐな壁を形成する材料は引張応力を受け、自然に薄くなります。薄化を緩和するために、深絞りプロセス変数が規制されていますが、一部の板金薄化は避けられません。おそらく、最大の薄化は、パーツのベース近くの側壁で発生します。一部の分野では、適切に描画された部分の厚さが最大25%減少する場合があります。
深絞り比
板金ブランクに搭載された図面の量を定量化することが可能です。描画比率はこれを行うことができます。絞り比が大きいほど、深絞り量が多くなります。ワークの形状、力、金属の流れ、および材料特性により、1回の操作で板金ブランクに対して実行できる深絞りの量には制限があります。絞り比は、深絞りの可能な最大量を決定するのに役立ちます。絞り比は、おおよそDR = Db / Dpとして計算されます。
Dbはブランクの直径、Dpはパンチの直径です。非円形の場合は最大径を使用することもあれば、表面領域を使用して絞り比を計算することもあります。操作の場合、描画率の制限は通常2以下です。また、図面の深さ、パンチ半径、ダイ半径、シートの異方性、およびブランクの材質にも依存します。
深絞りの削減
減少(r)は、描画パーセンテージを表す別の方法です。削減は、描画の割合と同じ要素で評価されます。 R =(Db-Dp)/(Db)を使用して削減量を計算できます。
DbとDpは、ブランクの直径とパンチの直径です。 .5以下の削減があるはずです。減少率r =(Db-Dp)/(Db)Xは、多くの場合100%として表示されます。この状況では、減少は50%以下である必要があります。
板金の再描画
板金の削減が50%を超える必要がある場合は、さまざまなアクティビティでコンポーネントを作成する必要があります。再描画は、すでに深絞りのプロセスを経たジョブの後続の深絞りです。複数の手順を使用することで、より深い描画を実現できます。
マルチ深絞り操作プロセス
中間形状の設計は不可欠であり、各中間ステップには、独自のツールと構成が必要になります。各手順は次の手順に影響を与え、各段階を分析する必要があります。中間形状を設計するときは、板金の削減を考慮する必要があります。ほとんどの場合、ブランクの表面積、中間形状、および部品は同じであると見なすことができます。
コンポーネントを再描画するために、シートの逆描画または逆描画が使用されることがあります。次の操作のためにダイに配置される前に、中間部分は逆再描画で裏返されます。これにより、シートメタルが逆方向の最初のドローとしてドローされます。
深絞り板金力
板金の深遠な線引き手順を実行するために使用される力は、シートの変形、適切な金属の流れを確保し、プロセス中の摩擦を克服するのに十分でなければなりません。力の大きさを上げすぎたり、誤って加えたりしないでください。そうしないと、板金が裂ける可能性があります。パンチとブランクホルダーは別々の力を発揮するため、両方の力の分析を行う必要があります。
生産段階でのマテリアルフローを理解することは、ジョブに作用する力を理解するために重要です。丸いカップに一枚の紙を平らに置くことを想像してみてください。これは、丸型のキャビティ上の板金のようなものです。これで、パンチアクションを模倣することにより、紙がカップに押し込まれ、カップの円筒形になります。その過程で紙の折り目やしわが発生します。深絞り手順では、これは板金ワークピースの動作方法ではありません。一つの理由は、紙とは異なり、金属材料が流れる可能性があることです。紙の代わりにアルミホイルをカップに置きます。アルミホイルは金属製ですが、カップに押し込むとまだしわが寄っています。カップに押し込むと、アルミホイルのしわが発生するのは、ホイルの密度が不十分なためです。
ここで、空白の金属シートが丸い円筒形の部分に深く引き込まれていると想像してみてください。パンチの下の材料はキャビティに押し込まれて部分の壁を形成し、材料を引き寄せます。ある量の板金材料が深絞りでダイに引き込まれず、完成部品の周りにフランジを形成することがあります。ただし、ダイの半径を超えてダイキャビティ内にまだ描画されていないすべての材料は、深絞り手順ではフランジと呼ばれることがよくあります。フランジからの材料は、継続プロセス中に継続的にダイに押し込まれます。ダイキャビティの直径は板金ブランクよりも小さく、金属は外周から内側に流れます。
深絞りにおける金属の流れ
直径の小さい領域に押し込まれた材料(誇張)
次の図では、金属の流れがわかります。深部延伸が進むにつれて領域Aからの金属が領域Bに押し込まれると、領域Bからの金属は領域Cに押し込まれ、領域Cからの金属はダイチャンバーに押し込まれます。これは、最終的に、領域Aの材料でさえキャビティに押し込まれるまで続きます(最終製品にフランジが与えられません)。スペースの収縮により、材料は圧縮力で動作します。金属がダイに引き込まれるため、フランジにも引張力が発生します。
深絞り中にフランジの材料要素に作用を強制します
ストレス下での金属豆の座屈
深絞り時のシワ
金属ビームへの圧力が座屈を防ぎます
板金の深遠な絞り加工では、力と材料の流れの分布にコーナー半径とパンチコーナー半径が不可欠です。
深絞りのコーナー半径
低いコーナー半径によって引き起こされる板金のテラニング
パーツ壁の作成に力を加えることも不可欠です–深絞りでの壁の形成
パンチが進むにつれて、フランジからダイキャビティに材料が運ばれ、成形品の壁の長さが長くなります。パーツの壁を形成する金属には張力がかかっています。フランジ領域から材料を絶えず引き出して、増加する成形品の壁に供給しますが、引張力によって薄肉化の影響が生じる傾向があります。間引きは、通常、パーツのベースに近い最大のものです。深絞り部品の壁で発生する密度の低下は、プロセスパラメータ制御によって軽減されます。通常、ある程度の間伐は避けられません。アイロンがけの製造方法は、夜間の壁の厚さによって深く描かれたコンポーネントを完成させるためによく使用されます。
特定の板金深絞り手順を開発するときは、パンチ力とブランクホルダー力を決定する必要があります。手順全体を通して、パンチ力は異なります。パンチ力は通常、ストロークの約1/3でピークに達します。パンチの強度とブランクホルダーの力の両方は、パンチとダイの形状、パンチとダイの半径、ブランクの形状、ブランクのサイズ、ブランクの材料、および摩擦に依存します。変動しますが、最大パンチ力の約30%から40%がブランクホルダー力の一般的な値です。これらの変数に基づいて、これらの力を計算するための参照が利用可能です。