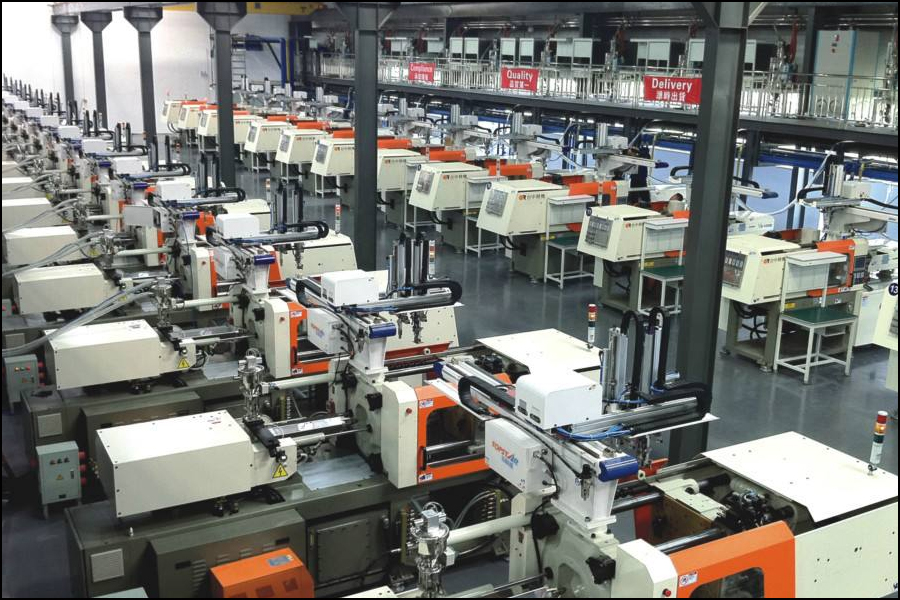
プラスチック射出成形はプラスチック製品の主要な処理方法の一つであり,射出成形品はプラスチック製品の全重量の30 %以上を占めている。プラスチック射出成形は非常に複雑なプロセスです。溶融または可塑化されたプラスチック材料は、最初に型に注入されるかまたは型に圧入される。そして、材料が型空胴の形にコピーされるまで、材料は保持される。プラスチック射出成形金型は、単一のキャビティで構成することができるか、またはいくつかの同一または異なるキャビティで構成することができ、各キャビティは、流路を介して各キャビティ内にフローチャネル、プラスチック射出成形および溶融プラスチック流と接続される。製造方法は単一の生産方法で最も経済的な方法の一つであり,プラスチック射出成形の3つの主要工程は以下の通りである。
- 1 .特定の圧力の下で流れることができる温度にプラスチックを熱してください。この工程を材料の可塑化(可塑化)と呼ぶ。
- 2 .金型における塑性養生射出成形機の射出シリンダからの溶融プラスチックは、様々なフローレーン、プラスチック射出成形を経て金型キャビティに供給され、所望のワークピースはキャビティの端部に形成される。
- 3 .プラスチックの硬化、圧力冷却のステレオタイプは、必要な製品になると、金型を開き、プラスチック部品を削除する加熱を停止します。
プラスチック注入プロセスは循環的なプロセスであり、全体のサイクルをいくつかの主要な段階で要約することができる。
プラスチック射出成形法の主なパラメータと技術条件は,射出圧力,金型温度,成形サイクル,射出成形プラスチックの温度,鋳型内のプラスチックの射出成形成形速度,金型内のプラスチックの溶融粘度と弾性せん断応力,溶融及び流れの制御とプロセス制御を含む。
プラスチック射出成形の効率と品質は主に金型の設計に依存する。射出成形金型の設計においては,まず,射出成形工程において,既存の加工・成形技術と製品形状に従って,設計計画を決定するための種々のプロセス条件を考慮すべきである。
プラスチック射出成形は重要な熱可塑性プラスチック成形方法であり、機械産業、自動車産業、家電産業、航空宇宙産業、生物学的フィールドおよび日常必需品の生産のプラスチック射出成形は広く使用される。他の成形プロセスと比較して、多くの明らかな利点があります:高精度、高複雑さ、美しい外観、低価格、プラスチック射出成形永続的な特性を持つプラスチック部品のその生産。そして、良いアセンブリと互換性の広い範囲に適用可能なプラスチック部品、標準化、シリアル化、標準化を達成しやすい。また、射出成形機は操作が容易であり、金型交換が便利で、製造サイクルが短く、射出工程は自動化、プラスチック製造射出成形は高い生産効率、良好な経済的利点を伴うので、達成することができます。射出成形は最も広く使われているプラスチック成形法となっている。