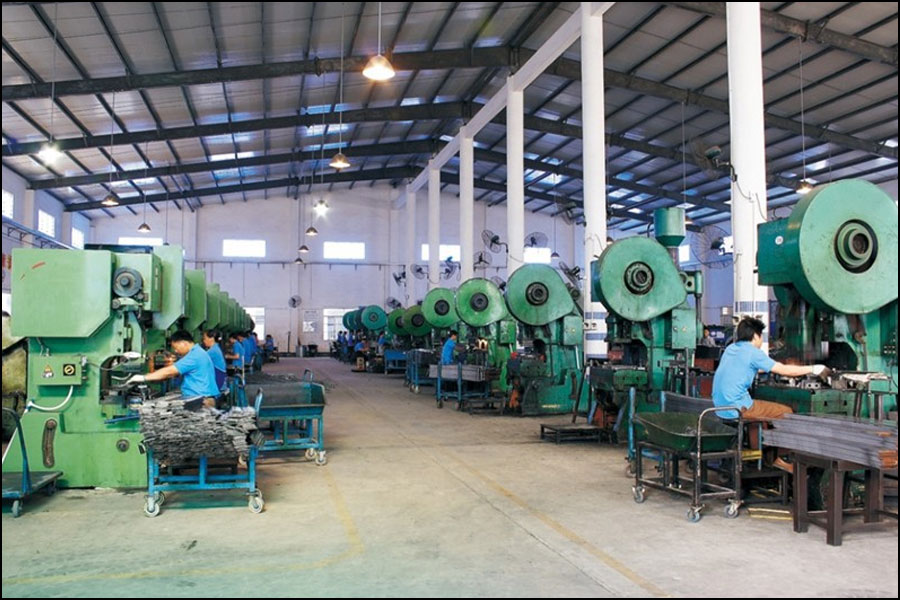
1.描画深度の影響
図面の深さでのダイオリフィス分布に沿った材料の流動抵抗の間には直接的な関係があります。凹曲線と凸曲線の位置では、絞り深さが大きすぎると変形抵抗の分布が不均一になる可能性があるため、しわを避ける必要があります。
2.ブランキング力の大きさを調整します
ワークの周囲に均一にシワが発生している場合は、押圧力が不足していると判断し、徐々にプレス力を上げてシワを解消してください。円錐と半球の部材を描画すると、描画の開始時にほとんどのマテリアルが吊り下げられた状態になります。側壁のしわが発生しやすいです。したがって、深絞り部品のエッジでのブランキング力を増やすことを除いて、パネルの半径方向の引張応力も増やして、しわをなくす必要があります。
3.スタンピング部品のメスブロック半径の影響
雌型プレスダイの半径が大きすぎ、ダイの半径を通ってダイに入るブランクの流れは、曲げ変形を小さくする曲げ抵抗です。曲げ抵抗が小さいほど、シワになりやすくなります。曲げ変形の小さい凹型ダイの曲げ抵抗が大きいほど、しわが寄りにくくなりますが、ワークにひび割れや引っ張りが発生しやすくなります。数多くの生産慣行と経験の蓄積により、スタンピング部品のしわの主な理由は、伸線プロセス中の材料の蓄積と局所的な材料の移動の過度の速度に起因します。
解決策については、上記の側面を考慮し、金型の対応するメカニズムを調整する必要があります。これにより、良好な結果が得られます。
スタンピング部品のしわを防ぐための対策は、金属スタンピング部品が適度なシートフロー速度で伸線プロセス中に材料を押すことができることを保証することです。スタンピング部分の伸びが速すぎると、シート材にしわが寄る場合があります。一方、シート材料の流れが遅すぎると、スタンピング部分にひびが入る可能性があります。
- (1)合理的なプレス装置の使用:プレス装置を使用する場合、プレス装置はブランクの変形部分をしっかりと押し付け、押し付け力に作用してフランジ部分のアーチやシワの発生を防ぎます。押す力の大きさは適切でなければなりません。プレス装置は、弾性プレス材料と剛性プレス材料の2種類に分けられます。弾性装置は浅絞りに適しており、剛性装置は深絞りに適しています。
- (2)ドロービーズの合理的な使用:プレス面のドロービードの設計は、変形抵抗を調整するための効果的な方法です。ドロービードは、材料の流れをうまく調整できるため、引き抜きプロセス中の各部品の材料の流れ抵抗が均一になり、キャビティに流入する材料の量がワークピースのニーズに適しており、しわが増えるのを防ぎます。ひび割れが少なくなります。現象。複雑な形状の湾曲したジョイント、特にフランジが小さいものの場合、しわを制御するためにドロービードを提供する必要があります。ドロービードの位置は放射状に引っ張られます。応力が小さい部分、つまりシートが流れやすい部分。フランジの小さい部品の場合、ドロービードをセットするために、必要に応じて一部の材料(プロセスサプリメント)を追加し、トリミング時にこの部品を削除します。深絞り部の深さが深い場合は、送りが少ない場所にドロービードを配置し、キャビティ内に組織化する材料が多すぎてシワを防止する必要があります。
4.製図部品のしわの原因の分析
伸線工程中の引張部材のしわには多くの理由があります。主な理由は次のとおりです。
- (1)スタンピング部の絞り深さが深すぎるため、送り加工時にシート材の流動が速すぎてシワになります。
- (2)伸線工程でダイのR角が大きすぎるため、延伸工程でパンチが材料を圧迫できず、シートの流れが速すぎてしわが発生します。
- (3)プレス部品のプレス材が不合理で、プレス材リブが小さすぎて位置が正しくないため、シート材の流れが速すぎてシワが発生するのを効果的に防ぐことができません。
- (4)エジェクタピンの圧力が小さすぎるため、プレス部品が完全に形成されず、シワが発生します。
- (5)金型の位置決め設計が不合理であるため、スタンピング部品の延伸工程で材料をプレスできないか、プレス材料の側面が小さすぎて、延伸プロセスで材料をプレスできません。しわを引き起こします。
- (6)凸型と凹型の隙間が大きすぎると、延伸時に材料をプレスできなくなり、シワが発生します。 上記は、金属プレス部品の延伸工程でのしわの一般的な原因であり、特定の問題については特定の分析が必要です。 スタンピングの特定の条件に基づいて特定の理由を見つけます。