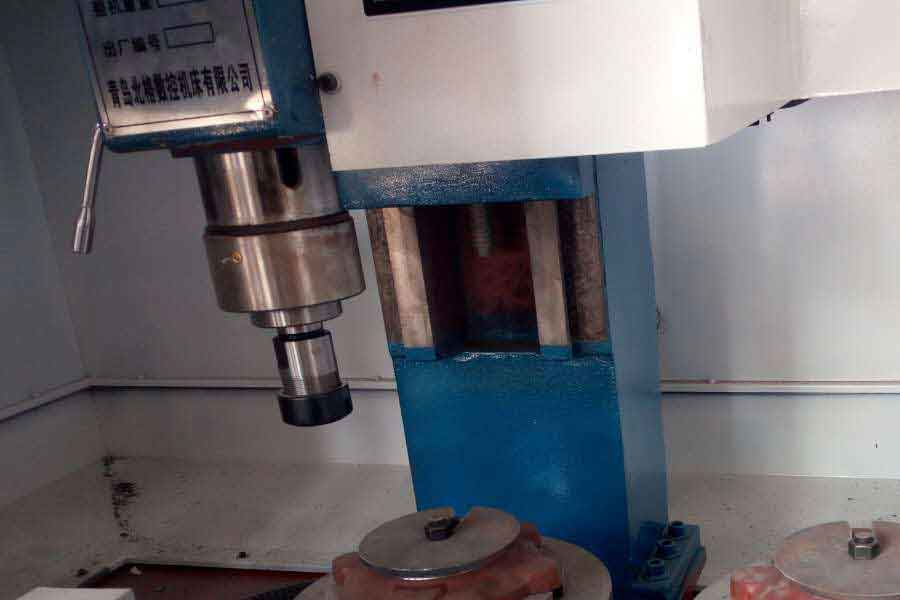
穴加工に使用する工具のサイズは、加工する穴のサイズによって制限され、剛性が低いと曲げ変形や振動が発生しやすくなります。
穴のサイズは、対応する工具のサイズに直接依存することが多く、製造誤差と工具の摩耗が穴の加工精度に直接影響します。
穴を加工する場合、切削領域がワーク内にあり、切りくず除去や放熱条件が悪く、加工精度や表面品質の管理が容易ではありません。
ドリル穴とリーマ穴
1.穴あけ
穴あけは、中実材料の穴を加工する際の最初のステップであり、穴あけ直径は通常80mm未満です。穴あけには2つの方法があります。1つはビット回転、もう1つはワークピースの回転です。上記の2つの穴あけによって発生するエラー方法は同じではありません。ビット回転の穴あけ方法では、刃先の非対称性やビットの剛性不足によりビットがずれると、加工穴の中心線が歪んだり真っ直ぐになったりしますが、基本的にアパーチャは変わりません。逆に、ワーク回転穴あけモードでは、ビットのずれによりアパーチャが変化しますが、穴の中心線は直線のままです。
一般的に使用されるドリルツールは、ツイストドリル、センタードリル、深穴ドリルなどであり、その中で最も一般的に使用されるのはツイストドリルであり、その直径仕様はφ0.1〜φ80mmです。
構造上の制限により、ドリルビットの曲げ剛性とねじり剛性が低く、センタリングが不十分であり、ドリルビットの加工精度が低く、一般にIT13〜IT11にしか到達できません。表面粗さまた、Raは一般的に50〜12.5μmです。穴あけの金属除去率が大きく、切削効率が高いです。主に、ボルト穴、ねじ底穴、オイルなど、品質要件の低い穴の加工に使用されます。穴等加工精度が高く、表面品質が要求される穴は、その後の加工でリーマ加工、リーマ加工、ボーリング加工、研削加工を行うことで実現します。
2.リーマ穴
リーマとは、リーマドリルで穴あけ、鋳造、鍛造を行った穴をさらに加工して、穴を大きくし、加工品質を向上させることです。リーマ加工は、仕上げ前の前処理として使用できます。穴、または要件の低い穴の最終処理として。リーマドリルはツイストドリルに似ていますが、歯が多く、水平ブレードがありません。
穴あけと比較して、リーマは以下の特徴があります:
- (1)リーマドリルより多くの歯(3〜8歯)、良好な導電性、比較的安定した切削;
- (2)リーマドリルはクロスエッジがなく、良好な切削条件;
- (3)加工代が小さく、切りくず保持溝が浅く、穴あけコアが厚くなり、ナイフ本体の強度と剛性が良好です。リーマの精度は一般的にIT11〜IT10、表面粗さRaは12.5です。 〜6.3。
リーマは、直径の小さい穴を処理するためによく使用されます。直径の大きい穴(D≥30mm)をドリルする場合、プレドリルには小さなビット(直径の0.5〜0.7倍)がよく使用されます。次に、対応するサイズの穴あけとリーマ加工により、穴の加工品質と生産効率を向上させることができます。
円筒穴の加工に加えて、さまざまな皿頭座穴と対面スポットフェーシングも、さまざまな特殊形状のざぐりドリル(カウンタービットとも呼ばれます)で加工できます。シェービングドリルのフロントエンドには通常、ガイドコラムが装備されており、ガイド付きです。機械加工された穴によって。
リーマ穴
リーマは、生産で広く使用されている穴の仕上げ方法の1つです。小さな穴の場合、リーマ加工は、内円研削やファインボーリングと比較して、より経済的で実用的な加工方法です。
1.リーマー
リーマは一般的にハンドリーマと機械リーマの2種類に分けられます。ハンドリーマのハンドルは真っ直ぐで、作業部が長く、ガイド機能が優れています。ハンドリーマは一体型と調整可能な外径の2種類の構造になっています。機械リーマはハンドル付きとスリーブ付きの2種類の構造があり、円形の穴はリーマで加工できるだけでなく、テーパーの穴もリーマで加工できます。
2.リーマ加工とその応用
リーマの許容量は、リーマの品質に大きな影響を与えます。許容値が大きすぎ、リーマの負荷が大きすぎ、刃先がすぐに鈍くなり、滑らかな加工面を得るのが難しく、寸法公差を確保するのが容易ではありません。マージンが小さすぎて、上部プロセスによって残されたカットマークを削除できません。これは、当然、穴処理の品質を向上させません。一般的に、粗いヒンジは0.35〜0.15mm、細かいヒンジは01.5〜0.05mmです。
エッジの蓄積を防ぐため、通常、リーマ加工では低速の切削速度(鋼や鋳鉄を加工する場合の高速鋼リーマ、V <8m / min)を使用します。送りの値は、機械の開口部に関連します。開口部が大きいほど送り値が大きくなります。高速鋼リーマを使用して鋼や鋳鉄を加工する場合、送り値は通常0.3〜1mm / rです。
リーマは、切りくずの堆積や適時の切りくず除去を防ぐために、適切な切削液で冷却、潤滑、洗浄する必要があります。研削穴やボーリング穴と比較して、リーマの生産性が高く、穴の精度を簡単に保証できます。リーマ穴は穴軸の位置誤差を補正できないため、前の手順で穴の位置精度を保証する必要があります。リーマ穴は、ステップ穴や止まり穴の加工には適していません。
リーマ精度は一般的にIT9〜IT7であり、表面粗さRaは一般的に3.2〜0.8です。中型および高精度の要件を持つ穴(IT7精密穴など)の場合、ドリルリーマおよびリーマ加工は、生産で一般的に使用される典型的な処理スキームです。
ボアホール
ボーリングは、切削工具でプレハブの穴を拡大する加工方法です。ボーリングは、ボーリングマシンまたは旋盤で行うことができます。
1.退屈なモード
退屈は3つの異なる方法で行うことができます。
旋盤ボーリングにおけるワークの回転、切削工具の送り動作は、主にこのボーリング方法に属します。プロセスの特徴は次のとおりです。加工後の穴の軸線は、ワークの回転軸と一致し、穴の真円度は主に工作機械の主軸の回転精度に依存し、穴の軸方向の幾何学的形状誤差は主にワークの回転軸に対する工具送り方向の精度に依存します。このボーリング方法は、同軸の穴を加工するのに適しています。外側の円の表面に必要です。
工具回転、送り動作中ぐり盤主軸駆動中ぐりカッター回転用ワーク、送り動作用ワークをテーブルドライブします。
このボーリング方法を使用した工具の回転と送り動作ボーリング、吊りボーリングバーの長さの変化、ボーリングバーの変形の変化、開口部のスピンドルボックスの近く、開口部のスピンドルボックスからの距離が小さい、形成テーパー穴。また、ボーリングバーの吊り下げ長さが長くなると、自重による主軸の曲げ変形も大きくなり、それに応じて加工穴の軸が曲がります。このボーリング方法は、より短い場合にのみ適しています。穴。
2.キム・ボーリング王
一般ボーリングに比べ、バックフィードが小さく、送りが小さく、切削速度が速いのが特徴で、高い加工精度(IT7〜IT6)と非常にきれいな表面(Ra0.4〜0.05)が得られます。ダイヤモンドボーリングはもともとダイヤモンドで加工されていました。ボーリング工具ですが、現在では硬質合金、CBN、人工ダイヤモンド工具で加工されるのが一般的です。主に非鉄金属加工品の加工に使用され、鋳鉄や鋼片の加工にも使用できます。
ダイヤモンドボーリングの一般的な切削パラメータは次のとおりです。バックカッティングツールのプレボーリングは0.2〜0.6mm、最終ボーリングは0.1mm、送り量は0.01〜0.14mm / r、切削速度は鋳鉄は100〜250m / min、鋼は150〜300m / min、非鉄金属は300〜2000m / min。
ダイアモンドボーリングがより高い加工精度と表面品質を実現できるようにするために、工作機械(ダイアモンドボーリングマシン)はより高い幾何学的精度と剛性を備えている必要があります。 -高速回転部品は正確にバランスが取れている必要があります。さらに、テーブルがスムーズな低速送り動作を実行できるように、送り機構の動きは非常にスムーズである必要があります。
ダイアモンドボーリングは、加工品質が良く、生産効率が高く、エンジンシリンダー穴、ピストンピン穴、工作機械スピンドルボックスの主軸穴など、多くの生産における精密穴の最終加工に広く使用されています。ただし、ダイヤモンドボーリングで黒色金属製品を加工する場合、ボーリングツールの作成に使用できるのは超硬合金とCBNのみであり、炭素原子の親和性のため、ボーリングツールのダイヤモンドの作成には使用できません。ダイヤモンドの鉄グループ要素、工具寿命は短いです。
3.ボーリングカッター
ボーリング工具は、片刃ボーリング工具と両刃ボーリング工具に分けられます。
4.ボーリングの技術的特徴と適用範囲
穴あけ・リーマ加工に比べ、工具サイズにとらわれず、ボーリングの誤差補正能力が高く、複数回の工具移動で元の穴軸偏位誤差を補正でき、ボーリング面と位置決め面の維持性を高めることができます。位置精度。
ボーリングや旋削に比べて、刃物系の剛性や変形が悪いため、放熱・切りくず除去状態が悪く、ワークや工具の熱変形が比較的大きく、加工品質や生産性が高いボーリングホールの効率は、ターンラウンドほど高くありません。
結論として、上記の分析から、ボーリングは幅広い処理に使用でき、さまざまなサイズと精度レベルの穴に使用できることがわかります。開口部が大きく、サイズや位置精度の要求が高い穴やシステムの場合、ほとんどの場合、ボーリングが唯一の処理方法です。ボーリングの加工精度はIT9〜IT7で、表面粗さRaはです。ボーリングは、ボーリングマシン、旋盤、フライス盤などの工作機械に使用でき、柔軟性のある利点があり、非常に広く使用されています。ボーリングの効率を向上させるために、大量生産ではボーリングダイがよく使用されます。
ホーニングホール
1.ホーニング原理とホーニングヘッド
ホーニングとは、ホーニングロッド(砥石)でホーニングヘッドを使って穴を研磨することです。ホーニングの際は、ワークを固定します。ホーニングヘッドは、工作機械の主軸で駆動され、直線的に回転・往復します。ホーニング時には、一定の圧力でホーニングロッドをワーク表面に塗布し、ワーク表面から非常に薄い材料層を切り落とします。砥粒の動きの繰り返しを避けるために、ホーニングヘッドの1分あたりの回転数とホーニングヘッドの1分あたりの往復移動量が素数である必要があります。
ホーニングトラックの交差角度は、ホーニングヘッドの往復速度と円速度に関係します。角度は、ホーニングプロセスの処理品質と効率に影響します。一般に、ホーニング時間はに設定され、ホーニング時間は細かく設定されます。壊れた砥粒や切りくずの除去を容易にし、切削温度を下げ、加工品質を向上させるために、ホーニングには十分な切削液を使用する必要があります。
加工穴壁を均一に加工するためには、サンドストリップのストロークが穴の両端で一定量を超えている必要があります。ホーニング許容値の均一性を確保し、回転誤差が加工精度に与える影響を低減するために、工作機械主軸、フローティング接続は主にホーニングヘッドと工作機械主軸の間で使用されます。
ホーニングヘッド研削ストリップの半径方向の拡張と調整は、手動、空気圧、および油圧構造で行うことができます。
2.ホーニングの技術的特徴と応用範囲。
ホーニングは、より高い寸法精度と形状精度を実現でき、加工精度はIT7〜IT6です。穴の真円度と円筒度誤差は範囲内で制御できますが、ホーニングでは加工する穴の位置精度を向上させることはできません。
ホーニングの結果、より高い表面品質を得ることができます。表面粗さRaは0.2〜0.025um、表面金属の変成欠陥層の深さは2.5〜25umと非常に小さいです。
ホーニングヘッドの周速は研削速度(vc = 16〜60m / min)に比べて高速ではありませんが、砂片とワークの接触面積が大きく、往復速度が比較的速い(va = 8〜20m /)ためです。 min)、したがって、ホーニングは依然として高い生産性を持っています。
穴ブローチ
1.カッターのブローチと削り取り
ブローチは、特殊なブローチを使用してブローチベッドで行う高生産性の仕上げ方法です。ブローチベッドは、水平ブローチベッドと垂直ブローチベッドの2つに分けられ、水平ブローチベッドが最も一般的です。
ブローチは切削時に低速直線(主な動き)でしか動きません。ブローチが同時に作動する歯の数は、一般的に3本以上である必要があります。そうしないと、ブローチがスムーズに作動せず、環状になりやすくなります。ワークの表面に波紋があります。ブローチを壊すための過度のブローチ力を避けるために、ブローチ作業時に使用するナイフの歯の数は6〜8を超えないようにしてください。
次のように説明されている3つの異なるブローチ方法があります。
層状ブローチ:このブローチ加工は、ブローチが加工代を層ごとに切断するのが特徴です。切りくずを容易にするために、ナイフの歯に切りくず分割スロットがあります。層状ブローチに従って設計されたブローチは、共通ブローチと呼ばれます。 。
スキップステッピング:このブローチ加工方法の特徴は、加工面の各金属層が、同じサイズで互いにインターリーブされたカッター歯のセット(通常は各カッター歯の2〜3個で構成)によって切断されることです.1つだけ各歯から金属の層が切り取られます。ブロックブローチによって設計されたブローチは、ホイールカッティングブローチと呼ばれます。
コンポジットブローチ:この方法は、層状ブローチとセグメントブローチの利点を集約します。歯の粗い部分にはセグメントブローチを採用し、歯の細かい部分には層状ブローチを採用します。このように、ブローチの長さは短縮でき、生産性が向上し、より良い表面品質が得られます。一体型ブローチに従って設計されたブローチは、一体型ブローチと呼ばれます。
穴あけの技術的特徴と適用範囲。
ブローチはマルチブレード工具です.1回のブローチストロークで、穴の荒加工、仕上げ、仕上げを連続して行うことができ、高い生産効率が得られます。
描画精度は主にブローチの精度に依存します。通常の状態では、線引き精度はIT9〜IT7に達し、表面粗さRaは6.3〜1.6umに達する可能性があります。
穴を引っ張るとき、ワークは加工された穴自体によって位置決めされます(ブローチの先端部分はワークの位置決め要素です)。穴と他の表面の相互の位置精度を確保することは容易ではありません。円形の表面の内側と外側に同軸性の要求がある場合、回転体パーツの処理は、通常、最初に穴を描画し、次に穴をローカリゼーションデータとして他の表面を処理します。
ブローチは丸穴だけでなく、成形穴、スプライン穴も加工できます。
ブローチは、形状が複雑で価格が高い固定サイズのカッターで、大きな穴の加工には適していません。大量生産の処理口径が10〜80mmと多く、穴の深さはそれ以上ではありません。中小部品の穴の開口部の5倍以上。