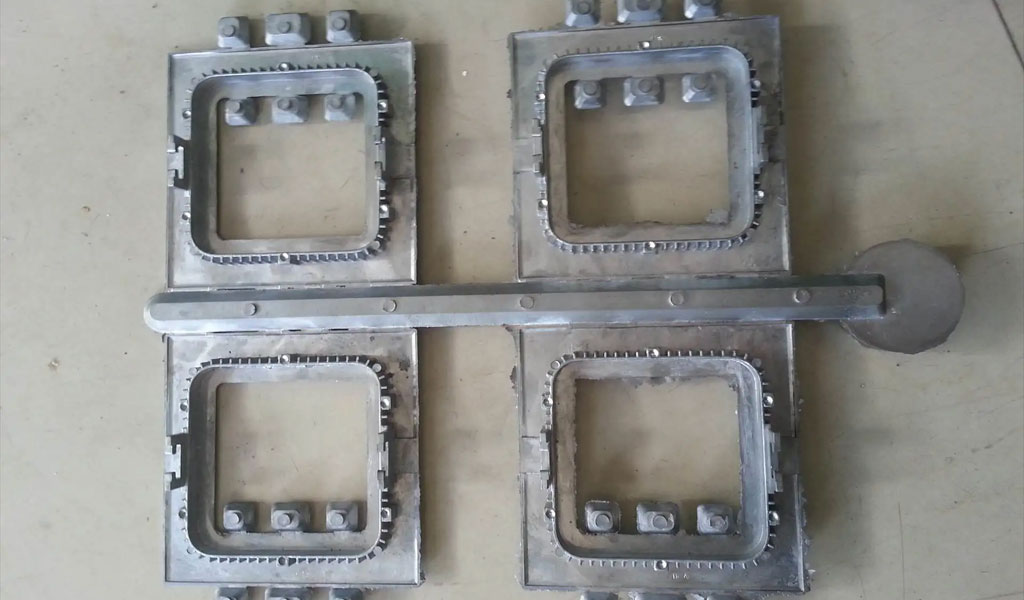
携帯電話、蛇口、カミソリのハンドル、ドアノブ、眼鏡フレーム、電動工具、サッカー シューズ、ゴルフ クラブなど、私たちが日常生活で使用する消費財の多くは、ダイカスト プロセスを経ています。自動車、航空宇宙、コンピュータ、HVAC、その他多くの分野を含むさまざまな業界が、ますます普及しているこの製造プロセスに依存しています。ダイカストは、完成した部品を表すために使用される用語で、高圧を使用して溶融金属を再利用可能な金型キャビティに押し込むことにより、金属部品の大量生産を可能にする製造技術を指します。
1830 年代後半から存在するダイカストには、長い成功の歴史があります。過去には、このプロセスは高価な機械と金型、長いセットアップ時間、高いスクラップ コストで有名でした。優れたものから劣悪なものまで、鋳物の品質は、メーカーが同じ機械と同じオペレーターを採用しているかどうかに依存していました。したがって、再現性の高い品質も問題でした。
今日、技術の進歩、より優れた材料科学、改善された製造プロセス、よりクリーンで効率的な機械が組み合わさって、ダイカストはより正確な科学になっています。さらに、より優れた金型設計と最先端のソフトウェアにより、金型製造の高速化、パフォーマンスの向上、無駄の削減が可能になります。これらすべては、継続的なコンピュータ化されたプロセス監視と自動化とともに、製造プロセス全体を改善し、材料の無駄を減らし、品質のばらつきを減らしました.
ダイカストのお客様は、優れた再現性のある品質、高い生産率、および低コストを備えた、より強く、より耐久性があり、密度の高い部品を期待できるようになりました。
ダイカストマシンとプロセス
メーカーは、ホットチャンバーとコールドチャンバーの両方のダイカストマシンを、それらが提供する型締力のトン数で分類しています。ダイカストマシンのサイズは400トンから4,000トンまであります。機械のサイズやダイカスト プロセスに関係なく、射出された溶融金属を使用して部品を鋳造するという基本的な目的はすべて同じです。プロセスには次の 2 種類があります。
ホットチャンバーダイカスト
本機は、溶融金属プールに浸漬する射出方式を採用しています。炉は、金属供給システムまたはグースネックを介して機械に接続します。サイクルの開始時に、ピストンが後退し、溶融金属が射出シリンダーのポートからグースネックを満たすことができます。プランジャーの下向きの動作により、ポートが密閉され、溶融金属がダイのグースネックとノズルに押し出されます。凝固後、プランジャーは上向きに引っ張ります。金型が開き、部品システムが部品を排出します。
ホットチャンバーダイカストでは、別の炉から金属を移す必要がありません。ただし、このプロセスは、銅、亜鉛、鉛、マグネシウムなど、射出シリンダーを損傷しない低融点合金に対してのみ実行可能です。
コールドチャンバーダイカスト
このマシンは、取鍋を使用して、溶融金属を保持炉から非加熱の射出シリンダーまたはショット チャンバーに移動します。このシステムは、油圧ピストンに依存してショットをダイに送り込みます。ホットチャンバー鋳造法と比較して、コールドチャンバー鋳造法はゆっくりとしたプロセスです。それにもかかわらず、それはアルミニウム部品の製造に最適です。ただし、溶融アルミニウム合金は、金属シリンダー、プランジャーを攻撃して損傷し、金型の寿命を縮める可能性があります。
ダイカスト マシンを選択する際に考慮すべき最も重要な要素は、型締力に関連するマシンのパフォーマンスです。機械の次の寸法上の制約も重要です。
- ショットボリューム容量
- 型開きストローク長
- プラテンエリア
金型内の部品の投影面積と、溶融金属の射出に必要な圧力によって、必要な型締力が決まります。より大きな部品には、より大きなクランプ力が必要です。型締力は、金型が分離しないようにするために、射出中に金型にかかる溶融金属の分離力よりも大きくする必要があります。
マシンのショット量容量を決定するには、まず総ショット量を計算する必要があります。これは、キャビティの容積、オーバーフロー ウェルの容積、およびフィード システムの容積を合計することで確認できます。成形機のダイスの最大開口部が十分に広く、障害なくパーツを取り出せることを確認してください。プラテン エリアまたはクランプ ユニットのコーナー バー間のスペースも、必要なダイに十分なスペースが必要です。
2 つの鋳造プロセスのバリエーションには、低圧ダイカストが含まれます。これは通常、回転軸を中心に対称性を必要とする車両ホイールなどのアルミニウム部品の製造に使用されます。スクイーズダイカストは、流動性の低い金属や合金の場合に使用されます。メーカーは、最小の気孔率、最大の密度、および高い精度が要求される仕様の部品にセミソリッド ダイ カスト法を使用します。鋳造後の処理を必要とする一部の製品は、真空ダイカストと呼ばれる比較的新しいプロセスの恩恵を受けることができます。これにより、強度が向上し、気孔率が最小限に抑えられます。
金型の種類
ダイ メーカーは、これらのツールをシングル キャビティ、マルチ キャビティ、コンビネーション、およびユニット ダイとして分類します。金型メーカーは、合金工具鋼からダイカスト工具を製造します。金型は、固定金型 (カバー ハーフ) とエジェクタ金型の 2 つのセクションで構成され、鋳物を取り出すことができます。多くの最新の金型には、可動スライド、コア、またはその他のセクションがあり、鋳物にねじ山、穴、およびその他の機能を生成します。亜鉛ダイの場合、溶融金属はダイに入り、固定ダイのスプルー穴からキャビティを満たします。通常、金型の半分のエジェクタには、溶融金属をキャビティに送るランナーとゲートが含まれています。ダイには、2 つの半分をしっかりと固定するためのロック ピンが含まれています。このツールには、鋳物を取り外し、潤滑剤と冷却剤を排出するのに役立つエジェクタ ピンもあります。
ダイカスト プロセス中、マシンの油圧によって 2 つのダイ ハーフが所定の位置にロックされます。ダイの 2 つの半分が交わる表面積は、「ダイ パーティング ライン」と呼ばれます。型のパーティング ラインから鋳造品の総投影表面積を測定できます。金型キャビティに金属を射出するために必要な機械の圧力は、機械の型締力と相関します。
複数のキャビティ金型は、複数の同一のキャビティで構成されています。 「ファミリー ダイ」と呼ばれることもあるコンビネーション ダイには、さまざまな形状のキャビティがあり、アセンブリ用の複数の部品を製造できます。ユニット金型は、アセンブリ用またはさまざまな顧客用に多数の部品を作成できます。
ランナーは、溶融金属を成形品のキャビティに送ります。金型に組み込まれており、コールドチャンバー機とホットチャンバー機では流路が異なります。コールド チャンバー マシンでは、ホット チャンバー マシンのスプルー ブッシュとは異なり、材料は射出スリーブを通って入ります。金型に入った後 (両方のマシンで)、溶融金属は一連のランナーを通って流れ、ゲートを通ってキャビティに入ります。
キャビティ内のオーバーフロー ウェルは、凝固中に追加の溶融金属を提供します。これらのウェルは、部品が冷えた後に溶融金属が収縮するため、必要な追加の材料を提供します。キャビティから金型の外側に伸びる小さなチャネルは、キャビティから空気を逃がすための通気孔として機能します。別のタイプのチャネルでは、オイルまたは水がダイに流れ、熱が除去されます。
金型設計に関しては、次のようなさまざまな要因を考慮する必要があります。
- 全てのキャビティに溶け込みやすい金型を作る
- 金型からの固化部分の除去(抜き勾配)
- アンダーカットなどの複雑な設計機能の調整
評判の良いダイカスト工場では、認定された高品質の工具鋼のみを使用し、北米ダイカスト協会によって設定された厳格な仕様に準拠していることをお客様は認識する必要があります。アルミニウム ダイは、顧客からの品質基準、部品の設計、指定された合金、および表面仕上げが重要かどうかなど、さまざまな要因に応じて、最大 150,000 ショットに耐えることができます。現在、ダイの寿命を延ばすことができるダイ コーティングも追加料金で利用できます。
ダイカストプロセス
製品の複雑さに応じて、合計サイクル時間は 2 秒から 1 分間続く場合があります。 ダイカスト部品のサイクル プロセスは、クランプ、射出、冷却、取り出し、トリミングの 5 つの主要な段階で構成されます。
- クランプ。プロセスの初期段階では、金型の 2 つの半分の準備とクランプが行われます。オペレーターは、最初に前回の射出で金型に残った金属を取り除き、次に金型を潤滑して次の部品の射出を容易にします。使用する材料によっては、各サイクルの後に潤滑が必要ない場合もありますが、通常は 2 ~ 3 サイクル後に潤滑が必要です。金型の潤滑にかかる時間は、部品のサイズ、キャビティおよびサイド コアの数によって異なります。ダイカストマシン内に固定された2つの金型部品は、注油後、クランプされます。機械は、金属の射出中に金型をしっかりと閉じた状態に保つために十分な圧力を加える必要があります。機械が大きくなるほど、金型を閉じてクランプするのに必要な時間が長くなります。
- 注射。炉内で設定温度に保たれた溶融金属は、チャンバーに移送され、金型に注入されます。溶融金属を移送するために使用される技術は、オペレーターがホット チャンバーまたはコールド チャンバーのどちらのマシンを使用するかによって異なります。移送後、溶融金属 (ショットと呼ばれる) が 1000 ~ 20,000 psi の圧力で金型に射出されます。材料が凝固するまで、圧力によって溶融金属が金型内に保持されます。射出時間は、溶融金属が金型内のすべてのチャネルとキャビティに流れ込むのにかかる時間を示します。 0.1秒未満という非常に短い時間により、金属の一部が早期に固化するのを防ぎます。適切な射出時間を決定するには、メーカーは材料の熱力学的特性と鋳造品の肉厚を考慮する必要があります。壁が厚いほど、射出時間が長くなります。コールド チャンバー ダイカスト マシンの場合、射出時間には、手動で溶融金属をチャンバーに取り込むのに必要な時間を含める必要があります。
- 冷却。溶融金属が金型キャビティに入ると、冷却と凝固が始まります。溶融金属がキャビティ全体を満たした後、凝固が起こり、鋳造品が最終的な形状になります。冷却時間が経過し、鋳物が凝固するまで、オペレーターは金型を開くことができません。金型の複雑さ、材料の熱力学的特性、および壁の厚さによって、冷却時間が決まります。
- 排出。冷却期間が経過した後、オペレーターは 2 つのダイの半分を開くことができます。排出機構が鋳物を金型キャビティから押し出します。マシンの乾燥サイクル時間と排出時間は、キャスティング エンベロープによって異なります。また、鋳造物が型から取り除かれるのに必要な時間を追加する必要があります。冷却プロセス中に、コンポーネントは収縮して金型に付着します。これには、鋳造品を取り出すのに十分な力が必要です。射出後、オペレータは金型をクランプして閉じ、次の射出に備えることができます。
- トリミング。冷却期間中に、チャネル内の金属材料が凝固し、鋳物に付着します。手動プロセス (ソーイングまたはカッティング) またはトリミング プレスを使用して、余分な材料とバリを鋳物からトリミングする必要があります。余分な材料をトリミングするのに必要な時間を決定するには、キャスティング エンベロープのサイズを調べます。このタスクからスクラップを破棄するか、後で使用するためにリサイクルできます。
ダイカストの最も一般的な材料は、アルミニウム、銅、マグネシウム、亜鉛などの非鉄合金です。それぞれの素材には独自の特性と長所と短所があり、お客様はそれらを慎重に検討する必要があります。材料を選択する際に考慮しなければならない要素には、密度、融点、強度、耐食性、およびコストが含まれます。
ダイカスト対。 その他のプロセス
最新のダイカスト プロセスは高圧下で行われるため、優れた表面仕上げと高い完全性を備えたコンポーネントが得られます。 ダイカストは、10,000 個を超える生産工程の実行可能な代替手段を提供します。 製造プロセスの一部は次のとおりです。
- プラスチック射出成形。ダイカストは、プラスチック射出成形で製造された部品よりも強く、剛性が高く、寸法的に安定した部品を提供します。ダイカストはまた、より耐熱性が高く、特性/コストベースでプラスチックの性能を超え、荷重下での高度な耐久性を備えたアイテムを提供します。これらの部品は、風化、応力亀裂、紫外線に耐性があります。プラスチック部品は、単位体積ベースでは安価であり、固有の色特性が優れているため仕上げの必要がありませんが、ダイカストで製造された部品の製造サイクルはより高速です。プラスチック部品も温度に敏感で、優れた電気絶縁体です。
- 鍛造品。ダイカストは複雑な形状にも柔軟に対応でき、鍛造できない形状を提供します。ダイカストは、鍛造プロセスでは不可能な薄い部分を持つことができます。鍛造は、より高密度で強力な部品を製造することを提供します。鍛造品には、鍛造合金の特性もあります。このプロセスでは、鉄やその他の金属を使用できます。
- スタンピング。このプロセスでは、組み立て作業が少なくて済む 1 つのダイカストと比較して、複数の部品が必要になる場合があります。ダイカストは、複雑さとより多くの形状のバリエーションを提供します。寸法限界が近いほど、切片の厚みにほぼすべてのバリエーションがあり、無駄が少なくなります。逆に、スタンピングは錬鉄金属と同様の特性を持ち、ダイカストには適さない鋼や合金からの製造を可能にします。通常、単純なスタンピング製品は軽量で、生産サイクルが短くなります。
- 砂の鋳物。ダイカストは、より厳しい寸法制限に耐えることができるより薄い壁と、より滑らかな表面を備えています。また、サイズに合わせてほぼすべてまたはほとんどの穴があります。ダイカストは、数千の部品を交換する必要なく製造する金型のサイクル タイムを短縮します。鋳造ごとに新しいコアを必要とせず、表面が滑らかで、鋳造ごとの労働コストが低くなります。鉄金属や、ダイカストでは実現できない多くの非鉄合金から砂型鋳造品を製造できます。砂型鋳造では、形状の可能性が広がり、最大サイズも大きくなります。機械のコストが低く、少量生産の経済性が向上します。ただし、砂型鋳造の機械加工量は常にダイカストよりも多くなります。
- スクリューマシン製品。ダイカストは、スクリューマシンプロセスよりも高速です。また、無駄が少なく、形状のバリエーションが豊富です。ただし、スクリューマシン製品は、ダイカストでは実現できない鋼や合金から製造できます。それらは鍛造金属の特性を持ち、工具のコストが低くなります。
全体として、ダイカストは、複雑な形状、滑らかな、またはテクスチャーのある表面、および高度の精度と再現性を備えた部品を製造する多用途のプロセスを製造業者に提供します。このプロセスにより、さまざまな魅力的で実用的な仕上げが可能になります。
ダイカスト会社の調達と見積もりの評価
プロジェクトの生産に適したダイカスターを選択することは、非常に困難な場合があります。 プロジェクトがアルミニウム、マグネシウム、亜鉛のいずれの材料を必要とする場合でも、ダイカストの金型と製造のコストを考慮する必要があります。 最初のエンジニアリング コンサルテーション中、および金型の構築を開始する前に、ダイカスターは最新のプロセス シミュレーション ソフトウェアと CAD ファイルを使用して、ダイカスト プロセスに不可欠な次のような多くの重要な要素を予測および最適化する必要があります。
- メタルフロー
- 空気の閉じ込め
- メタル速度
- 熱収支
- ホットスポット
- その他の要素
ダイカスト エンジニアは、品質の問題を回避するために、プロジェクトに関連するすべての変数を最初から最後まで理解しなければなりません。ダイカスターは、生産に使用する正しい金属について、経験と偏りのない意見を持っている必要があります。製品に後仕上げステップが伴う場合、選択する合金は希望する仕上げのタイプで機能する必要があるため、材料の選択はさらに重要になります。知識の豊富なダイカスターは、仕上げを完全に理解し、適切な推奨事項を作成できます。事前計画と分析の段階には、プロジェクトの全期間にわたって費用のかかるミスを回避するためのコスト削減策と方法に関する推奨事項が含まれている必要があります。
ダイ キャスターに製品設計用の金型の製造を許可する前に、設計とエンジニアリングの相談に関する包括的な説明を受けてください。ダイカスト エンジニアは、最終製品の品質、機能、性能要件を確保するために必要な設計コンセプトとすべてのコンポーネントを明確かつ完全に理解している必要があります。
当然のことながら、最も競争力のある価格を求める必要がありますが、会社が見積もりにどのようなサービスを含めているかを検討してください。追加のサービスをカバーする見積もりは、初期費用が高くなる可能性がありますが、製品の寿命全体で数千ドルを節約できる可能性があることに注意してください.
Be-cu.com は家族経営の企業で、30 年以上にわたってさまざまな業界にダイカスト サービスを提供してきました。当社は中国に拠点を置き、中国ダイカスト協会のメンバーであり、ISO 9001:2015 の認証を受けています。機械加工、金属仕上げ、組立を提供しており、アルミダイカスト製品を専門としています。ダイカスト サービスの詳細や見積もりについては、営業担当者にお問い合わせください。