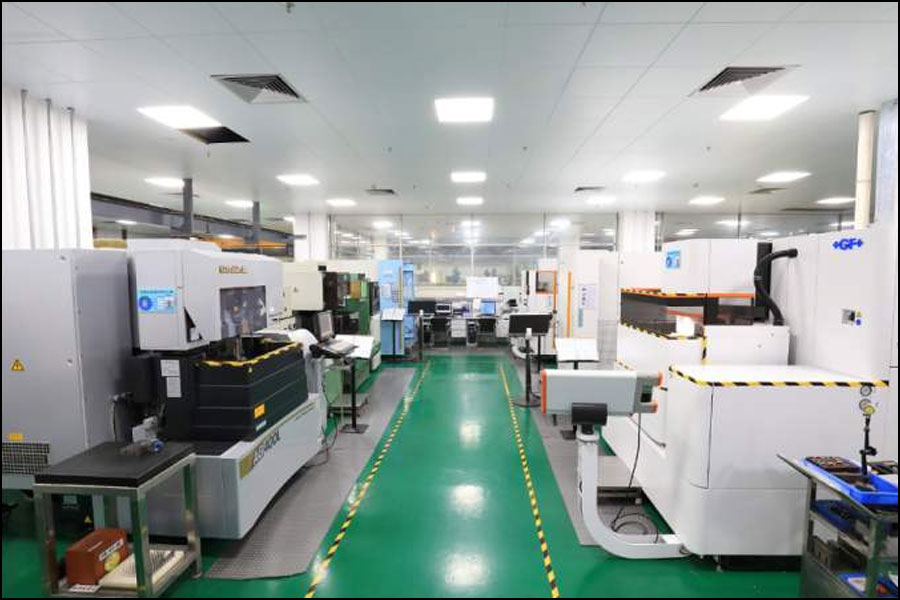
製品の品質は、製造の重要なパフォーマンス指標です。多くのワークショップは、ISO、NADCAP、API、およびその他の品質基準の認定を取得することは、作業の品質を確認することと同等であると考えています。しかし実際には、これらの基準は、適格な完成部品の製造方法に十分な注意を払っていませんが、欠陥部品を拒否するための手順の確立に焦点を合わせています。
製品の品質を真に理解するために、ワークショップの品質管理領域、特に「再チェック」ステッカーまたはラベルが部品に貼られている領域を観察できます。このタイプのラベルが貼付されている場合は、部品が何らかの理由で拒否されたか、再加工のために生産に戻す必要があることを意味します。製造工程が期待に応えられない場合、それはスクラップとやり直しにつながります。一部のプロセス、特に処理は、多くの変動要因の相互作用のために、ある程度不確実で信頼性がありません。製造業者は、不確実性の原因を特定し、これらの問題の解決策を見つける必要があります。ただし、多くの場合、不安定なプロセスは標準的な方法と見なされ、不安定性の原因は無視されます。最後に、不確実性を克服し、スクラップとやり直しを制限することは、製造現場の従業員の知識、知識、および動機によるものです。
不確実性の原因
競争圧力により、製造業者は、材料、工具、および処理時間のチェックのコストを含むコスト削減分析を実施するようになりました。 生産業務で時間を浪費するリンクを特定することは、コストを管理するための重要な機会を提供します。 コスト分析方法には、OEEとリーンプランニングが含まれます。 ただし、このタイプの分析は、製造プロセスが独立した単純なボックスであるという見解に基づいていることがよくあります。
ワークショップでは、原材料または半製品を箱に入れ、加工フローを開始し、一定数のワークを箱から出します。これらのワークは、完成品または半製品のいずれかで、別の箱に移動します。
処理変数を認識する
分析で見落とされがちな点の1つは、実際の生産では、箱から出たすべての製品が適格であるとは限らないということです。標準以下の製品は、手直しまたは廃棄する必要があります。
不適格部品の数は、製造プロセスの変動要因がどの程度制御されているかによって異なります。たとえば、鍛造やその他のプロセスは複雑ではなく、非常に高い精度を必要としません。したがって、これらのプロセスは比較的制御可能で信頼性が高く、期待される数の適格部品を一貫して提供できます。対照的に、製造フローの残りの4分の1には、結果の予測可能性を低下させる複数の変数が含まれます。箱から出てくる適格部品の数を確実に予測することはできません。
すべての処理技術は信頼できないと言っても過言ではありませんが、完全に予測できないと説明するのは非常に正確です。処理には多くの変数が関係しています。これにより、工具とワークピースの材料が強い切削力と高温に耐えることができます。力と温度の組み合わせにより、複雑で変動する状況が発生する可能性があります。工具の硬度が工具の有効切削能力を決定し、硬度は室温と加工中に発生する800℃の温度の間で変化します。熱は、被削材の加工特性にも影響を与えます。変動要因の影響は予測できません。特定のアプリケーションに処理パラメータが指定されていても、処理中の正確な値は不明です。表面品質や寸法の結果が異なると、部品が再加工または廃棄される可能性があります。
パーツが認定されていない場合は、2つの側面を確認する必要があります。 1つの側面はテクノロジーです。メーカーは実際に何が起こっているのかを理解し、予期しない結果につながる変動要因を特定し、問題を解決する方法を決定する必要があります。別の側面は、不適合部品の製造による経済的影響を判断することです。これには、拒否または再加工された部品の予期しないコストの計算と、会社がこれをどのように解釈するかを決定することが含まれます。
大量生産計画では、通常、不適格な部品の数を、全体として生産される数百または数千の部品と比較します。長期的な生産プロセスでは、ワークショップは処理条件を分析し、不適格な部品につながる要因を記録し、処理パラメータを最適化して不確実性を最小限に抑え、信頼性を向上させることができます。
ただし、多種多様な小ロット生産モードでは、ワークショップで不適格な部品をチェックし、処理技術を最適化する時間がほとんどありません。プロダクションランが1つのプロジェクトのみで構成されている場合、課題はさらに大きくなります。ショップが被削材に精通しておらず、最終顧客がすぐに完成品を必要とする場合、状況はさらに複雑になります。単一の部品を含む操作では、不適格な結果が生じる可能性があり、別の部品を処理する必要があり、コストが増加し、顧客を失望させます。
大量生産モードでは、不良部品の除去は比較的簡単です。技術者は、プロセスを確認および変更し、テストして、最終的にソリューションを確認します。実際の大量生産の状況では、不適格な部品の数は総生産量に比べて非常に少なく、コストはごくわずかです。ただし、複数の品種や少量のバッチ、または単一の部品の製造の場合、標準以下の部品のコストは利益率を大幅に低下させ、営業損失を引き起こすことさえあります。メーカーは非常に限られた時間でしか認定部品を製造できません。
隠されたコストまたは無視されたコスト
総生産コストを計算する際に、いくつかの隠れたコストが無視されることがよくあります。たとえば、バリ取りのコスト。処理された表面品質が技術仕様を満たし、そのエッジとジオメトリが青写真の要件を満たしている場合、ワークピースは完成したと見なされます。バリのある部分は未完成です。バリは処理品質の欠陥を表しますが、バリは一般にプロセスの正常な結果と見なされ、許容されます。いずれにせよ、バリは除去する必要があり、バリを除去するコストは高くなる可能性があります。実際の例は、5軸フライス盤を使用した高度に自動化されたワークショップで、手動によるバリ取りが必要な一連の部品が製造されることです。最終的に、バリ取りにかかる時間と工数は、完成品のコストの20%を占めます。
場合によっては、部品のコストと価格は、バリ取りやその他の二次処理のコストを考慮せずに、処理技術に基づいて計算されます。そのような費用は無視できないかもしれません。総製造コストを正確に計算するには、隠れたコストを特定して削減する必要があります。
ツールの選択
適切な生産設備とツールを使用することで、機械加工操作のばらつきを最小限に抑えることができます。大型の剛性機械工具は、ワークピースの寸法に一貫性がない原因となる強力な機械加工力に耐えることができます。ガラススケール、リニアガイド、熱管理システムなどの機械機能により、精度が最大化されます。
ツールの選択は、変動を制限する上で極めて重要な役割を果たします。過去20年から30年の間、ツールの選択方法は継続的に開発されてきました。これまで、ツールの選択は基本的に、最大の出力レートを提供する高性能ツールと最小のユニット部品コストを提供する経済的なツールに分けられていました。ただし、場合によっては、最高のパフォーマンスを発揮するツールは比較的壊れやすいものです。これらのナイフはうまく機能するとうまく機能しますが、取り扱いには注意が必要です。低価格のツールは、高性能ツールの速度と出力機能に匹敵することはできません。価格の利点は、出力の低下を犠牲にしてもたらされます。
今日、ツールを選択する際に、ジオメトリ、速度、フィードを選択する前の主な考慮事項の1つは、ツールのパフォーマンスに対するユーザーの要件です。大量生産作業では、金属除去率を最大化できるツールと、最大のツール寿命を提供できるツールが依然として必要です。精密加工は、工具のコストが高くても、工具の製造寸法、摩耗特性、およびアプリケーションパラメータの開発に非常に高い精度を必要とします。
多種多様な小ロット生産の現状では、部品を初めて加工する際に、完成したワークピースの品質が期待に応えることが非常に重要です。 重要なのは、すべての条件下で使用でき、プロセス開発時間が最短のツールが必要です。 これはまさに汎用ツールのR&Dコンセプトです(注を参照)。 生産エンジニアとオペレーターがツールの機能とその制限を理解していれば、信頼性が高く用途の広いツールが多くの機械加工アプリケーションにとって理想的な選択肢になります。 特定の数の汎用ツールを使用することにより、オペレーターは、さまざまな異なるワークピースの処理に適応しながら、時間の経過に伴うツールのパフォーマンスを学習および理解できます。
汎用ツールの適用を理解することで、不適格なワークピースの生産を最小限に抑えることができ、プロセスの信頼性が向上することで、財務管理部門が真のコストと利益率を正確に理解するのに役立ちます。