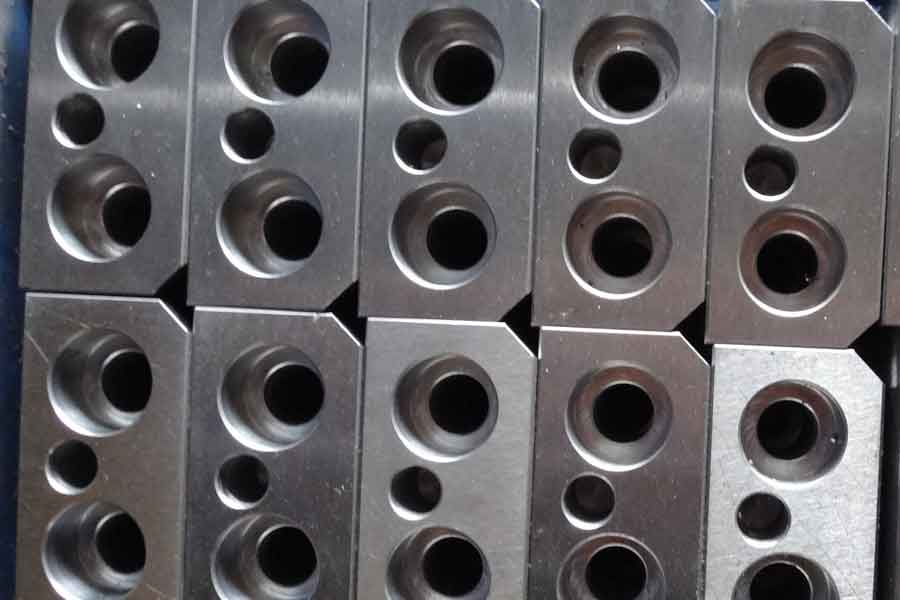
ファスナーのライフサイクル全体の重要な部分として、ねじ付きファスナーの製造は、ライフサイクル全体でのジョイントペアの信頼性を決定するための重要なプロセスです。ねじ付きファスナーの主な製造プロセスには、材料の変更、ブランク成形、ねじ成形、機械加工、熱処理、表面処理、表面後処理、スクリーニングおよびパッケージングが含まれます。
特定のねじ付きファスナーの場合、製造プロセスには必ずしも上記のプロセスのすべてが含まれるわけではなく、上記のプロセスのいくつかの組み合わせが含まれます。
例:Q1841050TF61六角フランジボルトM10X1.5×50グレード10.9シルバーグレークロームフリー亜鉛コーティング。製造工程は、材料改質→冷間圧造成形→ねじ山成形→焼入れ焼戻し熱処理→表面処理→ふるい分け→包装です。
材料の再構築
プロセスとしての材料の再構築は、冷間圧造成形に適した細い線に加工した後の製鉄所の熱間圧延ワイヤの製造です。 (赤いモールディングは、再構築せずにバーから直接カットできます)
材料の再構築の過程で、線材は3つの変更を受けました。
線径は、入口径から冷間圧造工程で必要な径に変化し、真円度を確保します。
ワイヤーの内部構造は、熱間圧延シートパーライト構造から球状パーライト構造に変更され、硬度が低く、可塑性が向上しています。
表面状態は熱間圧延スケール状態からリン鹸化状態に変化し、冷間圧造潤滑に適しています。
上記の3つの目的を達成するために、材料の改質は一般に3つの別々のプロセスで構成されます:酸洗リン鹸化、伸線、球状化焼鈍/再結晶焼鈍。
酸洗いは、ディスクサークルの表面の酸化物スケール/錆を酸で洗浄することです。リン酸塩処理は、ディスクマトリックスの表面に多孔質リン酸塩コーティングを形成することです。鹸化は、リン酸化ディスクサークルに付着した鹸化潤滑剤の層であり、ディスクサークル表面で一緒にリン酸化および鹸化して潤滑層を形成し、延伸または冷間圧造潤滑を行います。これらの3つのプロセスは、酸洗いリン鹸化成長ラインで実行されます。
線引きとは、リン光鹸化ディスクの直径を線引きダイから必要な直径の線材まで縮小し、線引き機で処理する工程です。
火は、ディスクサークルをその材料のAc1温度より20〜30℃高くし、ゆっくりと冷却した後しばらく保持して、フェライトマトリックス上に均一に分布した球状または粒状の炭化物の構造を得ることです。球状化された焼きなまし材料は、優れた可塑性を持ち、冷間圧造しやすい。再結晶焼鈍とは、粗伸線した線を再度焼鈍して冷間硬化をなくし、再度適切な線径に細線引きすることです。
ある種のワイヤーのリフォームを完了するには、多くの場合、上記の3つの作業手順が何度も組み合わされて必要になります。プロセスの組み合わせの1ボール1ストローク、1ボール2ストローク、2ショット2ストロークなどのフォーム。
たとえば、φ25SCM435材料の場合、φ24細線を2ボール2引き抜いた後、その再形成ルートは次のようになります。酸洗い→球状化→酸洗いリン鹸化φ→粗抽出φ24.49→再結晶焼鈍→酸洗いリン鹸化→微細抽出φ24。
1.冷間圧造成形
冷間圧造成形とは、冷間圧造機を使用して細線ダイを部品ブランクに冷間圧造することを指し、特殊なサイズ(細いロッド、大きな面取りなど)とねじ山に加えて、部品のすべての寸法がこれで得られます処理する。
冷間圧造金型は2つの部分に分かれており、1つの部分は主にメインダイと呼ばれるスクリューロッドを形成するために使用されます。成形されたボルトヘッドの一部はダイと呼ばれます。ボルトファスナーの頭は、通常、形成するために数回変形する必要がありますが、ねじ付きロッドは必ずしもそうではありません。
成形部品の複雑さに応じて、冷間圧造機はメインダイダイの数に応じてさまざまなモデルに分けられます:1ダイ2パンチ、2ダイ4パンチ、3ダイ3パンチ、4ダイ4パンチ、ファイブダイファイブパンチ。ボルトやネジの部品には、一般的に上記の装置で十分です。非標準部品を形成するために、より複雑な装置が一般的に使用されます。
成形部品のサイズに応じて、機器はいくつかのモデルに分けられます。装置モデルは通常、成形能力を表すコードと、10B4Sなどのキャビティの数を表すコードで構成されます。
冷間圧造ダイは、4つの4つの衝撃成形ダイのセットなどの複数のコンポーネントの組み合わせであり、4つの成形ステップで構成され、各作業ステップはメインモールドに戻り、再びダイになります。マスターモールドとダイとモールド、ダイ、金型、鈍針、指ぬき、ばねなど、一部の部品は一般的であり、一部の部品(サイズ部品を含む)は特殊部品に基づいています。
金型設計に従って最初に必要な部品の冷間圧造成形処理では、金型の組み合わせを組み立ててから、冷間圧造機に組み込む必要があります。次に、装置への線径細線の設計には、切断ダイがあり、設計の長さを切断します。次に、各ステップのアプセット成形を通じて、次のような最終的な成形部品のサイズに応じて各ステップを調整する必要があります。カッティングの長さを増減したり、シンブルの位置を調整したりします。適格な部品が冷たく動揺するまで。複雑な製品の場合、このプロセスには数時間または数日かかることがよくあります(新製品、新しい金型、新しいプロセス、初期デバッグ)。これは、コールドヘディング全体の生産性を制限する重要なプロセスでもあります。
2.機械加工
機械加工は、大きな面取りや放射状の穴など、冷間圧造できない特殊なサイズの部品を成形するために使用されます。ボルト面取り機などの特殊なものだけでなく、一般的なCNC旋盤、穴あけ機、その他の機器。以下は、一般的なファスナー加工の簡単な紹介です。
面取り:主にボルトテール面取りに使用されます。特に円錐台の端などのねじガイド端、テール面取りのテーパー端は成形のために機械加工する必要があります。このようなテール面取りは、自動面取り機で迅速に処理できます。
旋盤:ロッドの特別なサイズへのCNC旋盤の使用、ヘッド処理を指します。細かいミドルスムースロッド、ロッドの溝、ボールヘッド、大型シャフトショルダーは、一般的に旋削加工が必要です。旋削加工は、適切な固定具を使用してのみ完了することができます。
穴あけ:ワイヤーを通るボルトヘッドの穴、中空ボルトの中央の穴と放射状の穴(オイルボルトを通るブレーキキャリパーなど)は、ボール盤で穴を開ける必要があります
矯正:アスペクト比が大きい(通常10以上)ボルトの場合、熱処理や表面処理などの加工工程で曲げが発生しやすくなります。製品の特性に応じて、熱処理後または梱包前に部品を矯正する必要があります。矯正の前後に、資格を確実にするために完全な選択のために真直度チェックツールを使用することが一般的に必要です。
研削:高精度グレードの必要なスクリュー直径と高精度のはめあい要件のあるボルトロッドの場合、サイズの進行を確実にするためにグラインダーを使用して処理する必要があります。
テールカット:テールカット溝のあるボルトは、専用のテールカット機で加工する必要があります。直接成形されたコールドアプセットにも役立ちますが、溝部分を削るこの方法は円弧であり、塗料や異物を削るのに役立ちません。
3.ねじ山形成
ねじ山形成は、ねじ山を処理するプロセスです。現在、ねじ山は押し出し成形されています。成形力の大きさに応じて、図1に示すように、ねじりねじと圧延ねじに分けられます。
ねじをこすることは、ねじ板を2つの平らにこすること、往復運動、静的、ねじ押し出し成形を完了するプロセスでねじ板をこすることです。次に、スレッドが開始点までこすり戻され、送り機構が新しいブランクを再び送り、新しいサイクルを開始します。
モーターの往復力によるねじ転造押出し、ボルト強度が大きい場合は、ねじ転造を使用する必要があります。転がりは、2つのねじ転がりホイールを使用することです。ホイール、次に油圧押出側スクリューローリングホイールを使用して、設定された押出端に到達し、ねじ部品の処理が完了します。ラージサイズ(上記M18)およびワイヤーローリングを使用した熱処理ねじ成形後の部品の一部に。特殊な形状がいくつかありますが、スクリューマシンは送り部品としては良くなく、圧延線加工にも役立ちます。ローリングワイヤーは一般的に人工送りを使用し、加工効率はツイストワイヤーよりも低くなります。
糸成形は、摩擦線前の高温と摩擦線後の高温、熱処理前の糸成形を指す前の高温に分けられます。このとき、ボルト材料の硬度は低く、加工が容易で、摩擦線板の寿命があります。も高いです。摩擦後の熱間ねじは、熱処理後のねじ山形成を指します。熱間ねじ山形成は、成形時にねじ山の表面の圧縮応力を保持でき、ねじ山の耐疲労性が向上し、交互荷重下のエンジンやその他の部品に使用されます。しかし、ねじ板寿命のねじ山をこすった後の熱ねじは低く、コストが高くなります。
4.熱処理
熱処理は、プロセスの必要な機械的特性を達成するために、必要なボルト材料構造を得るために加熱と冷却を組み合わせることによって行われます。ファスナーの主な熱処理は、焼入れと焼戻し、浸炭(焼入れと焼戻しと同時に実行可能)、誘導焼入れの3つです。
焼入れ焼戻し熱処理は、焼入れ+高温焼戻しで焼戻しマルテンサイト(ソテンサイト)を得る熱処理工程であり、熱処理工程で完成します。ファスナーの典型的な焼入れおよび焼戻し熱処理ラインについては、図2を参照してください。
ボルトは供給され、洗浄され、角度が付けられ(現在、脱リン酸化は通常、オンライン脱リン酸化と呼ばれるこのステップに統合されています)、その後、急冷および加熱炉に入ります。オーステナイト化温度で一定時間保持した後、ボルトは急冷オイルタンクに落下して急冷を完了します。マルテンサイト構造の部分を焼入れした後、硬度は高いが脆性も大きく、焼戻し炉に油を除去した後、高温焼戻し、ソステナイトへの組成、硬度が低下し、塑性靭性も向上し、総合的に優れた機械的プロパティ。
処理プロセス全体でのファスナー材料の微細構造の変化。 (a)は熱間圧延板の大きな層状パーライト+フェライト構造です。球状化焼鈍後、炭化物は(b)になります。これは、フェライト上に均一に分布した球状粒子であり、良好な塑性を持ち、冷間圧造を助長します。焼入れ後、(c)マルテンサイト構造になります。高温で焼き戻した後、組織は(d)ソステナイトになります。
焼入れ・加熱の過程で、ボルト表面が脱炭素化しないようにするには、炉内の炭素ポテンシャルを制御して、材料表面での炭素拡散のバランスをとる必要があります。一般に、炭素ポテンシャルはボルト材料の炭素含有量と同じかわずかに高くなります。
ST歯タッピンねじなど、表面硬度を上げるために表面浸炭が必要な部品は、浸炭目的を達成するために焼入れ・加熱時に炉内の炭素ポテンシャルを上げる必要があり、それ以外は焼入れと同じです。焼入れ処理。
一部の特殊ボルトは、トラックプレートボルトの頭を補強したり、三角形の歯ボルトの貫通歯を補強したりするなど、局所的な表面硬度を上げる必要があります。この場合、プロセスを完了するために誘導焼入れが必要です。誘導焼入れは焼入れ焼戻し熱処理終了後に行い、ボルト材料の表面が脱炭素化されていないことを確認する必要があります。
5.表面処理
ファスナーの表面処理は、主に、保管や機能的な腐食保護を含む部品の腐食保護、および摩擦係数、導電率、外観などの特定の表面要件を取得するためのものです。
一般的な保護表面処理は、短期間の低品位防錆、黒化油、リン酸塩油に分けられます。中程度の防錆、電気亜鉛メッキ;高品質の防食、電気亜鉛めっき合金、およびクロムフリーの亜鉛コーティング。あまり一般的に使用されていないのは、電気泳動と溶融亜鉛です。その他の機能または表面処理には、亜鉛-スズ合金、銅メッキ、クロムメッキが含まれます。
黒化油:黒化は、部品の表面の強力な酸化剤を介して酸化鉄膜の層を形成し、腐食防止、高温での従来の黒化、強アルカリ溶液浸漬黒化、汚染、高エネルギー消費の目的を達成します。現在、焼戻し炉に特殊ガスを注入して黒化するガス黒化法と、焼戻しの残留温度を利用して焼戻し冷却槽に黒化剤を添加する液体黒化法もあります。ただし、後者の2つの黒化方法では、部品の表面に緻密な酸化第二鉄膜が形成されず、液体黒化は部品の表面に付着した黒色樹脂の層であることに注意してください。腐食を改善する効果もありますが、表面の摩擦性能は異なります。
リン酸塩油:化学反応により部品の表面をリン酸塩化してリン酸塩堆積物の層を形成し、次に油の隙間を埋めて腐食防止の目的を達成し、リン酸塩層が緩んで滑りやすく、良好な潤滑、表面摩擦係数は安定しています。亜鉛、マンガン、亜鉛カルシウム系などの異なる部分によってリン酸化すると、形成されるリン酸結晶の構造が異なるため、腐食係数と摩擦係数に違いがあります。
電気亜鉛めっき:電気亜鉛めっきは、鉄鋼部品に最も一般的に使用されている防食対策であり、外観が良好です。ファスナーにも広く使用されています。
電気亜鉛めっきのプロセスは次のとおりです:石油生産→錆の除去→亜鉛めっき→不動態化→シーリング。まず、油や錆を取り除いてきれいな表面を作り、電気化学反応で部品の表面に亜鉛層をめっきし、亜鉛表面にパッシベーション剤でクロメートパッシベーション膜を形成し、最後にパッシベーション膜の亀裂にシール剤を充填します。 。
亜鉛メッキタンクの液体酸とアルカリの式によると、亜鉛メッキは酸亜鉛メッキとアルカリ亜鉛メッキに分けられ、不動態化溶液に六価クロムが含まれているかどうかに応じて、三価亜鉛メッキと六価亜鉛メッキに分けられます。六価クロムは毒性の高いめっき廃水処理です。難しいので、六価クロムの不動態化を段階的に廃止します。亜鉛メッキの表面摩擦係数を制御するために、摩擦制御潤滑剤が一般にシール剤に添加されます。
クラス8.8以下の留め具には、一般的に電気亜鉛めっきが推奨されます。クラス10.9のボルトには、水素のエンブリッタビリティのリスクがあるため、電気亜鉛めっきは推奨されません。使用する場合は、水素フラッディングを追加する必要があります。 12.9重要な部品の亜鉛メッキボルトは禁止されています。
ご了承ください:
- A.アルカリ性、酸性の亜鉛メッキに関係なく、めっき液は水素イオンを含む水溶液であるため、水素脆化の恐れがあります。
- B.水素フラッディングは、水素脆化のリスクを減らすことはできますが、完全になくすことはできません。
- C.水素脆化の平行支持面のテストに合格しても、水素脆化の可能性が完全に排除されるわけではありません。
- D.水素イオンは主に電気めっきプロセスで鋼マトリックスに入り、酸洗いプロセス時間は短く、低温です。水素脆化への寄与:電気めっき>リン酸塩>酸洗い。
電気亜鉛めっき層が外界によって腐食されると、最初に外側の不動態化シーリング層が破壊され、亜鉛層が水と酸素と反応して白い錆を形成します。その後、腐食が続きます。亜鉛層が金属マトリックスに浸透した後、酸化鉄の赤い錆が発生します。これは、塩水噴霧試験における白錆時間と赤錆時間です。シーリングを増やすと白錆の時間が長くなり、亜鉛層の厚さを増やすと白錆から赤錆までの時間が長くなる可能性があります。黒化およびリン酸塩化には亜鉛層がないため、白錆時間はなく、赤錆時間のみです。
電気亜鉛めっき合金(zn-ni合金、zn-fe合金):通常、電気亜鉛めっきを密封した後でも、その防食塩の噴霧レベルはわずか200〜300時間です。亜鉛層に合金を添加すると、亜鉛層、一般的に使用される亜鉛合金亜鉛ニッケル合金および亜鉛鉄合金の耐食性を向上させることができます。塩水噴霧は700時間から800時間続きます。 (現在、樹脂シーラント(通常は黒亜鉛)を添加することで耐食性を大幅に向上させる亜鉛メッキ方法があります。原理は、従来のコーティングの外側の樹脂保護層を増やし、樹脂の耐食性を使用して白錆時間を延長することです、耐食性を向上させるため)
電気亜鉛めっきと同様に、電気亜鉛めっき合金にも水素脆化のリスクがあり、部品の強度レベルが高いほど、リスクが高くなります。
クロムフリーのzn-alコーティング:クロムフリーのzn-alコーティングは、環境保護ダクロとしても知られています。ダクロの関係は、xiaobianの以前の記事「ダクロコーティングスリーライフスリーライフ」で見ることができます。環境保護(重金属を含む廃水残留物がない)、水素脆化のリスクがなく、強力な耐食性という利点があります。これは、高強度および高腐食保護要件のあるファスナーで広く使用されています。無クロム亜鉛アルミニウムコーティングは、底部コーティングと表面コーティングに分けられ、底部コーティングは主に亜鉛シートとアルミニウムシートと接着剤で構成され、腐食防止の目的で、表面コーティングは一般に摩擦係数安定剤を含み、摩擦係数を制御できます、また、耐食性を向上させ、特別な外観を得ることができます。
電気めっきと比較して、クロムフリー亜鉛コーティングの唯一の欠点は、コーティングと基板の間の結合力がコーティングの結合力よりも弱いことであり、特定の条件下で局所的な脱落が発生し、耐食性に影響を与える可能性があります。
摩擦係数の安定性とさまざまな表面への適応性から、電気めっきによるクロムフリーのzn-Alコーティング。
電気泳動:電気泳動は、腐食を防ぐために電気化学的方法によって金属の表面に高分子樹脂を堆積させることです。水素脆化のリスクは小さいですが、使用率は高くなく、一部の内部ファスナーにのみ適用されます。
ホットディップ亜鉛:ホットディップ亜鉛ファスナーは溶融亜鉛溶液に浸され、亜鉛層の厚さは非常に厚く、最大50umを超え、自動車用ファスナーはめったに使用されません。ねじ工学は6AZグレードを選択する必要があり、ねじ強度が低下し、環境保護ではなく高エネルギー消費になります。
亜鉛-スズ合金:電気システムで使用されるファスナーは、導電性のために亜鉛-スズ合金で電気メッキされています。
銅メッキ:溶接ボルトには、導電性を向上させるために銅メッキを使用します。高温環境で使用されるボルトやナットの中には、銅メッキが使用されているものもあります。銅メッキファスナーの全体的な用途は少なくなります。
クローム:露出したホイールナットは、外観を確保するためにクロームメッキされます
6.テーブルの後処理
表面処理は、外観と摩擦係数の制御要件を考慮して、主にファスナーの腐食保護要件のためのものです。その他の特別な要件については、表面処理後に処理する必要があります。一般的に使用されるファスナーは、接着剤、スミアワックス、粘着防止剤で処理した後にテーブルに使用されます。
接着:接着の主な目的の1つは、回転による緩みを防ぐボルトの能力を高めることです。その原理によれば、それは化学接着剤とニノン接着剤に分けられます。他の種類の接着剤は、シーリングを目的としています。
ケミカルグルーは接着剤で、ボルト噛み合いネジでプレコートされ、取り付け後の接着反応、ボルトナットは緩みを防ぐために接着されています。化学接着剤は、AB接着剤と嫌気性接着剤に分類されます。 AB接着剤にはマイクロカプセルの2つの成分があります。マイクロカプセルはボルトの取り付けにより破砕され、2つの成分が固化して反応により結合します。嫌気性接着剤の成分のマイクロカプセルは、破壊後、酸素の非存在下で固化および結合された。化学接着剤が硬化した後、分解すると結合が破壊されるため、修理では新しいボルトを交換する必要があります。
ナイロン接着剤は、糸の表面に硬質ナイロンの層でコーティングされています。取り付け後は、ナイロンの埋め込み圧力に依存して緩みを防ぎます。加工時には、最初に誘導加熱でボルトを加熱し、次にボルトの加熱面にナイロン粉末を吹き付け、ナイロン粉末を溶かして接着し、コーティングを完了します。
特定の降伏点で組み立てられたボルトも、最大の軸方向予圧のためにワックスで塗られます。
粘着防止剤:テフロン、溶接ボルト、溶接ナット、その他のボディ電気泳動付きファスナーなどの代表的なものが使用されます。ボルトが溶接スラグにくっつくのを防ぎ、身体の電気泳動中にファスナーが電気泳動塗料を蓄積するのを防ぐことができます。
7.ふるい分け
完成したボルトは、梱包する前に、欠陥のある部品や混合物を見つけるためにふるいにかける必要があります。現在のスクリーニングには、光学スクリーニング、レーザースクリーニング、および渦電流スクリーニングがあります。スクリーニングは一般に比較方法の使用であり、光学スクリーニングとレーザースクリーニングは混合とサイズの欠陥(ねじ山がない、ねじ山が不完全、ガスケットの漏れなど)をスクリーニングできます。光学スクリーニングは液体の溝でスクリーニングすることもできます。渦電流スクリーニングは、大きな硬度偏差、材料エラーの混合、および熱処理部品の異常をスクリーニングできます。
当社の製品にご興味がおありでしたら、図面と一緒にご要望をメールでお送りください。私たちはあなたに最も有利な見積もりを与えることを非常に嬉しく思います。もしそうなら、私たちの電子メールは次のとおりです:[email protected]、私たちに迅速かつ簡単に電子メールを送信するには、左側の電子メールアドレスをクリックしてください