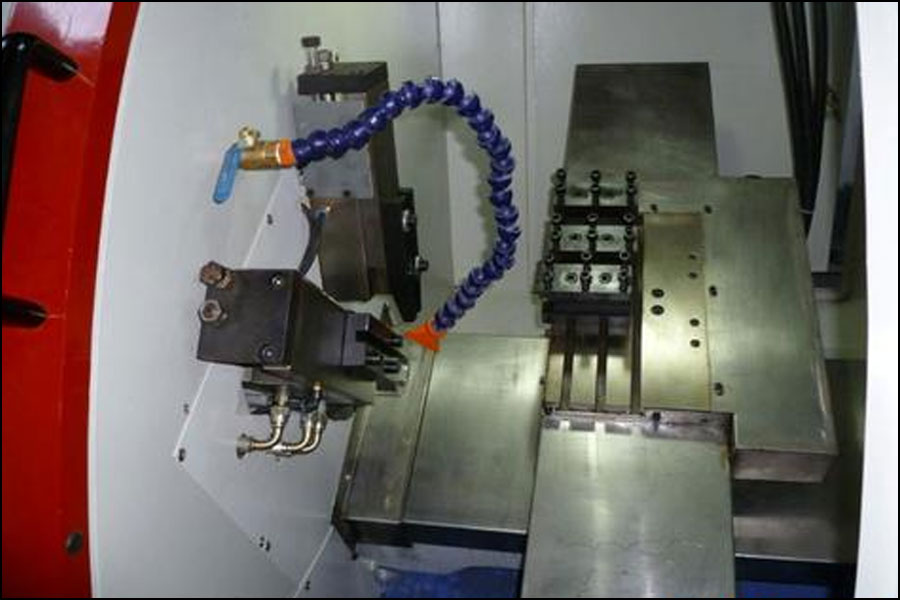
工作機械の精度を向上させる方法は2つあります。 1つは、エラー防止と呼ばれる、部品の設計、製造、および組み立てのレベルを改善することにより、考えられるエラーの原因を排除することです。この方法は、主に加工母機の精度に制約される一方で、部品の品質向上により加工コストが増大し、使用が制限されます。もう1つはエラー補正と呼ばれ、通常、マシンツールの加工命令を変更して、マシンツールでエラー補正を実行し、理想的なモーション軌道を実現し、マシンツールの精度のソフトアップグレードを実現します。研究によると、幾何学的誤差と温度によって引き起こされる誤差は、機械工具の全体的な誤差の約70%を占めています。幾何学的誤差は比較的安定しており、簡単に補正できます。 CNC機械工具の幾何学的誤差の補償は、機械産業全体の処理レベルを向上させることができ、科学技術の進歩を促進し、中国の国防能力を向上させ、中国の包括的な国力を大幅に強化するために非常に重要です。
1幾何学的誤差の原因
CNC機械工具の幾何学的誤差は以下の理由で引き起こされると一般に考えられています。
1.1工作機械の元の製造エラー
は、機械工具の各部品の作業面の幾何学的形状、表面品質、および相互位置誤差によって引き起こされる機械工具の運動誤差を指します。これが、CNC機械工具の幾何学的誤差の主な理由です。
1.2工作機械の制御システムのエラー
工作機械軸系のサーボ誤差(輪郭追従誤差)と数値制御補間アルゴリズムの誤差を含みます。
1.3熱変形誤差
工作機械の内部熱源による工作機械構造の熱変形と環境熱擾乱による誤差。
1.4切削荷重によるプロセスシステムの変形によるエラー
には、工作機械、工具、ワークピース、固定具の変形による誤差が含まれます。この種のエラーは「ナイフ」とも呼ばれ、特に薄肉のワークピースを処理する場合や細いツールを使用する場合に、処理されるパーツの形状の歪みを引き起こします。このエラーはより深刻です。
1.5工作機械の振動誤差
切断工程中は、工程の柔軟性と工程のばらつきにより、CNC工作機械の運転状態が不安定な領域に陥りやすく、チャタリングが激しくなります。これは、処理されたワークピースの表面品質の劣化と幾何学的エラーにつながります。
1.6検出システムのテストエラー
には次の側面が含まれます
- (1)測定センサーの製造エラーおよび工作機械への取り付けエラーに起因する測定センサーフィードバックシステム自体のエラー。
- (2)機械工具部品および機構のエラーと使用中の変形による測定センサーのエラー。
1.7外部干渉エラー
環境や動作条件の変化によるランダムエラー。
1.8その他のエラー
プログラミングエラーや操作エラーなどによるエラー。
上記のエラーは、エラーの特性と性質に応じて、系統的エラーとランダムエラーの2つのカテゴリに分類できます。
CNCマシンツールの系統的エラーは、マシンツールに固有のエラーであり、繰り返し可能です。 CNC工作機械の幾何学的誤差がその主要な構成要素であり、再現性もあります。この機能を使用すると、「オフライン測定」が可能になり、「オフライン検出-開ループ補正」テクノロジーを使用して、修正および補正を行い、それを削減して、工作機械の精度を高める目的を達成できます。
ランダム誤差はランダムであり、機械工具の加工精度へのランダム誤差の影響を排除するために「オンライン検出閉ループ補正」の方法を使用する必要があります。この方法は、測定機器や測定環境に厳しい要件があり、推進が困難です。
2幾何学的誤差補償技術
エラーの種類に応じて、エラー補正の実装は2つのカテゴリに分類できます。ランダム誤差補正には「オンライン測定」が必要です。誤差検出装置は工作機械に直接取り付けられています。工作機械の動作中に、対応する位置の誤差値をリアルタイムで測定し、この誤差値で処理指示をリアルタイムで補正します。ランダムエラー補正は、マシンツールエラーの性質を必要とせず、マシンツールのランダムエラーとシステムエラーを同時に補正できます。ただし、高精度の測定装置やその他の関連機器一式が必要であり、コストも経済的にも良くありません。文献[4]はオンラインで温度測定と補正を行ったが、実用化には至らなかった。システムエラー補正は、対応する機器を使用して事前に工作機械を検出すること、つまり「オフライン測定」により工作機械の作業スペースコマンド位置の誤差値を取得し、工作機械の座標の関数として使用することです。工作機械が作動しているときは、処理ポイントの座標に従って、対応するエラー値を呼び出して修正します。修正を容易にするために、工作機械の誤差の確実性を確保するためには、工作機械の安定性が必要です。補正後の工作機械の精度は、工作機械の再現性と環境条件の変化に依存します。通常の状況では、CNC工作機械の繰り返し精度は、その空間的包括誤差よりもはるかに高いため、システム誤差を補正することで、工作機械の精度、さらには工作機械の精度レベルを効果的に向上させることができます。これまでのところ、国内外のシステムエラーに対する多くの補償方法があり、次の方法に分けることができます。
2.1単一誤差合成補正法
このような補正方法は、誤差合成式に基づいており、まず、機械工具の個々の元の誤差値を直接測定法で測定し、誤差合成式で補正点の誤差成分を計算して、機械工具の誤差補正を実現します。 3座標測定機の位置誤差測定はリーテであり、三角形の幾何学的関係を用いて、回転角度の影響を考慮せずに、工作機械の各座標軸の誤差を表現する方法を推定します。最も早い誤差補正はホッケン教授である必要があります。モデルMoore5-Z(1)のCMMについては、16時間以内に、作業スペース内の多数の点の誤差が測定され、その過程で温度の影響が考慮されました。 、および最小二乗法を使用してエラーモデルパラメータを特定しました。工作機械の動きの位置信号はレーザー干渉計から直接得られるので、角度・真直度誤差の影響を考慮し、満足のいく結果が得られます。 1985年、G。Zhangは座標測定機でエラー補正を実行することに成功しました。作業台の端の値がわずかに大きく、その他の値が1μmを超えないことを除いて、作業台の平坦度誤差を測定しました。これにより、剛体仮説の信頼性が検証されました。レーザー干渉計とレベルメーターで測定された21個の誤差は、線形座標変換によって結合され、誤差補正が実装されます。 X-Y平面での測定実験では、補正前は全測定点の20%が20μmを超える誤差値を示し、補正後は20%以下の誤差が2μmを超えており、精度が10倍近く向上していることがわかります。
座標測定機の誤差補正に加えて、CNC工作機械の誤差補正に関する研究も一定の成果を上げています。 1977年、シュルツチク教授はベクトル図の方法を使用して、機械工具のさまざまな部分の誤差とその幾何学的精度への影響を分析し、機械工具の幾何学的誤差に関するさらなる研究の基礎を築きました。フェレイラと彼の共同研究者もこの方法の研究を行い、機械工具の幾何学的誤差の一般的なモデルを取得しました。これは、単一誤差の合成補償法に貢献しました。 J.Nietalはさらにこの方法をオンラインエラー補正に適用し、比較的理想的な結果を得ました。 Chenetalは、32項目のエラーモデルを確立しました。そのうち11項目は、温度と機械原点エラーパラメータに関連しています。水平マシニングセンターでの補正テストでは、精度が10倍に向上していることが示されています。 Eung-SukLeaetalは、G.Zhangとほぼ同じ測定方法を使用して3座標ブリッジポートミリングマシンの21のエラーを測定し、エラー合成方法を使用してエラーモデルを取得します。補正された結果は、それぞれレーザー干渉計とレニショーのDBBによって使用されます。システムは、工作機械の精度が向上したことを証明するためにテストされています。
2.2エラー直接補正方式
この方法では、工作機械空間のベクトル誤差を正確に測定する必要があります。補正精度が高いほど、測定精度と点数が高くなりますが、測定空間内のどの点の誤差も詳細に知ることはできません。補間法を使用してください。補正点の誤差成分を求めて誤差補正を行います。この方法では、補正と整合性のある絶対測定座標系を確立する必要があります。
1981年、DufourとGroppettiは、さまざまな負荷と温度の条件下で機械工具の作業スペースポイントの誤差を測定し、機械工具の誤差情報を取得するための誤差ベクトルマトリックスを作成しました。エラー補正のために、エラーマトリックスをコンピューターに保存します。同様の研究は主にACOkaforetalを含み、工作機械の作業空間における標準基準部の複数点の相対誤差を測定することにより、最初の点を基準点とし、絶対座標誤差に変換し、補間により誤差補正を行います。精度が2〜4倍になっていることを示しています。 Hoomanは、3次元線形(LVTDS)測定装置を使用して、機械工具空間の27ポイントの誤差(分解能0.25μm、再現性1μm)を取得し、同様の作業を実行しました。温度の影響を考慮して、1.2時間ごとに測定を行い、合計8回の測定を行い、誤差補正結果の温度係数を補正しています。この方法の欠点は、測定ワークロードが大きく、保存されるデータが大きいことです。現在、完全に適切な機器はなく、この方法のさらなる適用と開発も制限されています。
2.3相対誤差分解、複合補正法
ほとんどの誤差測定方法は、相対的な包括的な誤差を取得するだけであり、それに従って、工作機械の個々の誤差を分解することができます。マシンツールのエラーを補正するために、エラー合成をさらに利用することは可能です。現在、この分野での国内外の研究も一定の進展を遂げています。
2000年、ミシガン大学のJunNi教授の指導の下、博士課程の学生であるChen Guiquanがそのような試みを行い、ボールバー(TBB)を使用して、さまざまな温度で3軸CNC工作機械の幾何学的誤差を測定し、迅速な温度予測と誤差補正モデルを確立しました。 、エラー補正を実行します。クリストファーは、レーザーボールバー(LBB)を使用して、30分以内に工作機械のエラー情報を取得し、エラーモデルを確立しました。9か月の間隔内で、エラー補正の結果を5回評価しました。結果は、ソフトウェアが誤差補正方式は、工作機械の精度を向上させ、長期間にわたって精度を変化させないようにすることができます。
誤差合成法は、工作機械の各軸の元の誤差を測定する必要がありますが、より成熟した測定法は、測定精度の高いレーザー干渉計です。デュアル周波数レーザー干渉計を使用したエラー測定には時間がかかり、オペレーターの高度なデバッグが必要です。さらに重要なことに、エラー測定環境に対する要件が高く、3座標測定機の検出によく使用され、生産現場の運用には適していません。相対誤差分解・合成補正法は比較的簡単で、全周のデータ情報を1回の測定で取得でき、工作機械の精度や工作機械の評価に対応できます。現在、誤差分解法は数多くありますが、工作機械の条件が異なるため、誤差分解に適した一般的な数学モデルを見つけることが難しく、測定結果に同じ影響を与える元の誤差項を分解することができず、普及・適用が困難です。直接誤差補正法は、一般に標準部品を制御して空間ベクトル誤差を求め、直接補正を行うことで中間リンクをなくし、工作機械の実際の状況に近づけます。ただし、大量の情報を取得するためには異なる標準部品が必要であり、達成が困難であるため、補正精度に限界があります。