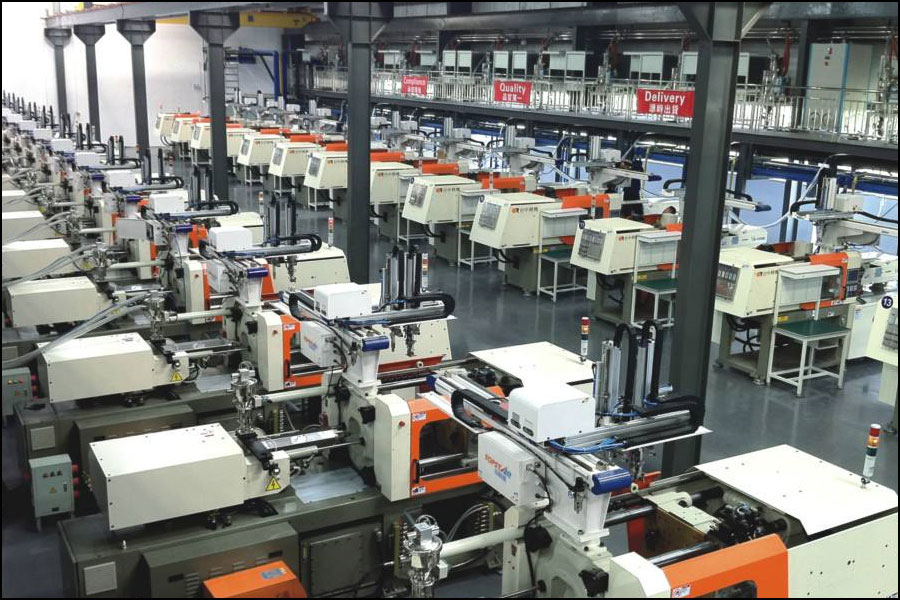
プラスチック射出成形はプラスチック製品の主要な処理方法の一つであり,射出成形品はプラスチック製品の全重量の30 %以上を占めている。プラスチック射出成形は非常に複雑なプロセスです。溶融または可塑化されたプラスチック材料は、最初に型に注入されるかまたは型に圧入される。そして、材料が型空胴の形にコピーされるまで、材料は保持される。プラスチック射出成形は、鋳型が単一のキャビティで構成されてもよく、あるいは、いくつかの同一または異なるキャビティで構成することができ、各キャビティは、流路に接続され、溶融プラスチックはフローチャネルを通って各キャビティ内に流れる。製造方法は単一の生産方法で最も経済的な方法の一つであり,プラスチック射出成形の3つの主要工程は以下の通りである。
- 1 .特定の圧力の下で流れることができる温度にプラスチックを熱してください。この工程を材料の可塑化(可塑化)と呼ぶ。
- 2 .金型における塑性養生射出成形機の射出シリンダからの溶融プラスチックは、様々なフローレーン、プラスチック射出成形を介して金型キャビティに供給され、最後に、必要なワークピースは、キャビティの制限の下で形成される。
- 3 .プラスチックを硬化させるために加熱を止めてください、圧力冷却ステレオタイプは必要な製品になって、型を開けます、プラスチック射出成形はプラスチック部品を取り除きます。
プラスチック注入プロセスは循環的なプロセスであり、全体のサイクルをいくつかの主要な段階で要約することができる。
プラスチック射出成形法の主なパラメータと技術条件は、射出圧力、金型温度、成形サイクル、射出成形プラスチックの射出成形温度、金型内のプラスチックの流動、金型内のプラスチックの溶融粘度および弾性剪断応力を含む。プラスチック射出成形溶融と流れ制御とプロセス制御
プラスチック射出成形の効率と品質は主に金型の設計に依存する。射出成形金型の設計においては、まず射出成形法において一般的に使用される様々なプロセス条件、既存の加工によるプラスチック射出成形、成形技術、及び設計図を決定する製品形状を考慮すべきである