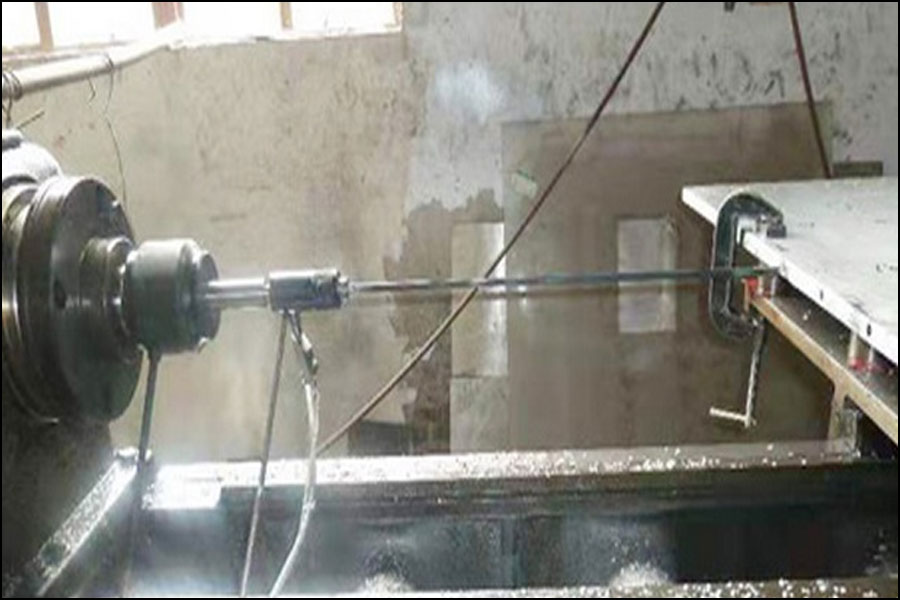
金属切削工程全体を最適化することにより、加工において最高の生産性と収益性を実現することができます。この作業の基本は、工作機械の加工能力を最大限に活用しながら、工具切削パラメータを賢く使用することです。
金属切削工程全体を最適化することにより、加工において最高の生産性と収益性を実現することができます。この作業の基本は、工作機械の加工能力を最大限に活用しながら、工具切削パラメータを賢く使用することです。機械工具の効果的な利用を実現するには、2つの重要な要素があります。
1つは、マシンが金属を切断するために使用できる時間を最大化する方法を見つけることです。2つ目は、この時間を最も生産的にすることであり、2つ目は、最も生産的で、信頼性が高く、収益性の高い方法で使用することです。 。
利用可能な時間を最大化する
工作機械を最大限に活用するには、金属の切断に使用できる時間を最大化することから始める必要があります。マシンが1年365日ワークショップにある場合でも、その生産の可用性。週5日、毎日1シフトの場合、休日などを除いて、生産に利用できる時間は、年間約1,300または1,400マシン時間です。それでも、すべてのマシンがこれらの時間帯に金属を切断しているわけではありません。プログラミングと設定には時間がかかります。非生産時間を可能な限り短くするために、メーカーはオフラインプログラミングとモジュラー設計方法を含む戦略を採用する必要があります。ツールマガジンと自動ツールチェンジャーは、ツール処理の別の時間のかかるイベントをスピードアップします。ロボット化された作業処理と交換テーブルは、元の部品のロードと完成した部品のアンロードに必要な時間を短縮するのに役立ちます。プログラミング速度の向上、設定方法の高速化、工具や作業の簡素化により節約された時間は、部品の加工に使用できます。
時間を効率的に使う
金属の切断に利用できる時間を最大化する戦略を実行した後、メーカーが直面する問題は、この時間を効率的に使用して、可能な限り低いコストで可能な限り多くの製品を生産する方法です。重要なのは、刃先が被削材に接触しているときに、機械の機能を最大限に活用することです。さらに、工作機械の機能制限を理解することも非常に重要です。
利用可能な時間を最も効果的に使用する計画を立てるとき、プロセスの特定の要素を変更できないことは明らかです。機械加工されたワークピースの最終用途により、メーカーが選択するワークピースの材料が決まり、材料の被削性は、使用できる初期の切削パラメーターを示します。たとえば、チタン合金は熱伝導率が低いため、熱の蓄積を最小限に抑えるために、低い切削速度と送り速度を使用する必要があります。通常、機械を交換する直接のオプションではないため、工作機械の機能も示されています。製造業者は、製造コストを評価する際にこれらの要因を認識しています。ただし、工作機械の特性評価が不正確で、持続不可能な切削条件を使用した場合、推定コストは実際のコストとはかけ離れたものになります。
すべての機械加工の初期切削パラメータを決定するときは、いくつかの一般的な規則に従う必要があります。ツールの破損を防ぎ、必要なスライスが確実に形成され、発熱を制限するために、適切な切断深さと送り速度を選択する必要があります。切削速度が速すぎると工具が急速に摩耗し、速度が遅すぎると工具が効率的に機能しなくなります。
通常、高速切断は短時間でワークピースを生成します。加工時間は短くなりますが、工具寿命が短くなり、工具コストが高くなります。ジョブを完了するには、より多くのツールが必要になり、ツールのインデックス作成と変更の必要性に起因するダウンタイムにより、全体的な運用コストが増加します。実際、高速切断と高い処理コスト、および低速切断と低い運用コストの間にはトレードオフがあります。安定した生産効率とプロセスの安定性は2つの方法の間にあります。不十分な切断パラメータはコストを削減しますが、ツールは効率的に機能できず、生産性は低下します。パラメータが高くなると生産性は向上しますが、ツールはすぐに摩耗または破損します。
さらに、切断条件の選択は、切断ツールに依存するだけでなく、ほとんどの場合、機械ツールの機能にも依存します。工作機械が異なれば、出力、トルク、速度、安定性の限界も異なります。最も明白な制限は電力です。
定格電力だけでは、特定のアプリケーションのマシンの機能は決まりません。 60kWの工作機械は十分な電力を供給できるようですが、長さ12m、直径3mのロールを製造する場合は、60kWでは不十分です。特定のワークピースを切断するために必要な電力は、ワークピースの材料とサイズ、切断の深さ、送り速度、および切断速度によって異なります。速度の増加に伴って切削力が指数関数的に増加するため、電力需要が増加します。したがって、切削速度が速いと、機械の定格出力を超える出力が必要になる場合があります。
さらに、極端な切削パラメータは、他の機械機能の許容範囲を超える場合があります。切削深さが極端に大きいと、工作機械構造の剛性よりも高い力が発生し、振動により部品の品質が低下する場合があります。同様に、送り速度が大きすぎると大量の切りくずが発生し、切断プロセスが妨げられ、切りくず除去システムがブロックされます。
機能限界内で工作機械を最大限に活用するには、切削パラメータの開発にインテリジェントでバランスの取れた方法を適用する必要があります。通常、それは、それに応じて送り速度と切込みの深さを増加させながら、切削速度を下げることを含みます。工作機械の安定性を考慮し、可能な限り最大の切削深さを使用すると、パスの数を減らすことができるため、処理時間を短縮できます。通常、切削深さは工具寿命にほとんど影響しませんが、切削速度は工具寿命に大きな影響を与えます。
同時に、極端な送り速度はワークピースの表面研磨に悪影響を及ぼしますが、送り速度を最大にする必要があります。
サプライヤーが送り速度と切込みの深さの信頼できる組み合わせを達成すると、切削速度を使用して機械加工の最終校正を行うことができます。目標は、実りある金属除去率とプロセスの安定性を提供する切断条件を使用することです。機械の性能と切削パラメータの最良の組み合わせにより、工具コスト、プロセスの安定性、生産性のバランスをとることができます。
今後の戦略
工作機械の性能が加工プロセスを制限する可能性があることに気付いた場合、工作機械の交換は簡単、迅速、または経済的な解決策ではありません。これは、切断ツールのアプリケーションパラメータを制御して、既存のマシンツールの最高のパフォーマンスを実現するためのより高速で簡単な方法です。新しい機械工具への投資が可能であっても、機器の比較的長い耐用年数は重要な考慮事項です。企業は、現在のニーズに匹敵する、またはそれを超える性能の工作機械を購入する可能性があります。今後5年、10年、またはそれ以上で、部品や被削材、寸法、体積などの要素は大幅に変化する可能性がありますが、機械工具は引き続き使用できます。通常の操作。
これらの変化に対応するためには、切断条件をよりスマートに変更する必要があります。
機械工具を使用して金属を切断できる時間を最大化する方法を見つけた後、推奨されるアプローチは、ワークピースの材料および関連する処理に最適な工具を選択し、最適なベース材料、コーティング、および刃先の形状を使用することです。次のステップは、ツールが正しく機能していることを確認しながら、最小切断速度を選択することです。その後、機械工具の出力と安定性の特性を考慮して、送り速度と切り込みの深さをできるだけ高くする必要があります。数式は、処理パラメーターとマシンのパフォーマンスの間の最適な一致を決定するのに役立つように作成されています。可能であれば、ショップは同様の結果を得るためにフィールドテストを実行することを好むかもしれません。通常、公式は事実を確認することしかできません。ただし、90%を超える場合、最も簡単で実用的な最も効果的な方法は、最大送り速度と切断試行を使用しながら低速の切断速度を使用し、切断速度をキャリブレーションツールとして使用することです。この方法は、信頼性が高く生産性の高い加工を実現するだけでなく、既存の工作機械の加工能力を最大限に活用することができます。