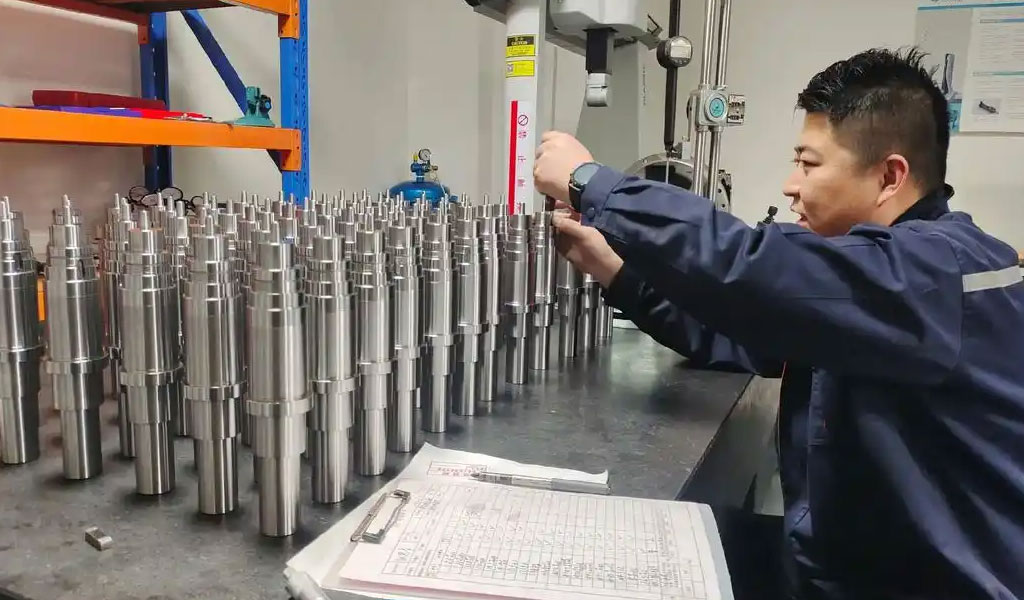
2025年(令和7年)は、日本の機械加工業界にとって、技術的、社会的、経済的変革が交錯する重要な転換点となる年である。この年は、日本の人口動態、産業政策、グローバル競争環境、そしてデジタルトランスフォーメーション(DX)の進展が複雑に絡み合い、機械加工業界に多大な影響を及ぼすと予測されている。本項では、これらの要因がどのように業界に作用するか、その科学的根拠と予測データを基に詳細に解説する。また、主要な影響要因を他国との比較を通じて明らかにするため、詳細な表を付与する。
背景:日本の機械加工業界の現状と歴史的文脈
日本の機械加工業界は、第二次世界大戦後の経済復興期から高度経済成長期にかけて急速に発展し、工作機械や精密加工技術において世界的な地位を確立した。工作機械とは、金属やその他の材料を切削、研削、成形する機械であり、自動車産業、航空宇宙産業、電子機器産業など、多様な製造業の基盤を支えている。2020年代初頭時点で、日本は世界の工作機械生産額においてドイツ、中国と並ぶ主要国の一つであり、特に高精度かつ高品質な製品で知られている。例えば、2021年の国際工作機械工業会(IMTMA)のデータによれば、日本の工作機械生産額は約1兆3000億円で、世界シェアの約15%を占めていた。
この成功の背景には、日本の技術者文化、厳格な品質管理(例:ISO 9001に基づく品質保証体系)、および自動車産業との密接な連携がある。特に、トヨタ自動車や本田技研工業といった企業は、ジャストインタイム生産方式やカイゼン(継続的改善)を推進し、機械加工業界に高い効率性と柔軟性を求めてきた。しかし、2025年に向けて、これらの強みが逆に制約となり得る状況が顕在化しつつある。
2025年問題と労働力不足の影響
人口動態と超高齢化社会
2025年問題とは、団塊の世代(1947~1949年に生まれた約800万人)が全員75歳以上の後期高齢者となることで、日本が超高齢化社会に突入する現象を指す。総務省の統計によれば、2025年の日本の総人口は約1億2257万人、そのうち後期高齢者人口は2180万人に達し、高齢化率は約36.1%となる見込みである。一方、生産年齢人口(15~64歳)は約6760万人まで減少し、2015年の約7700万人から約1000万人減少する。これは、機械加工業界における熟練労働力の喪失と新規労働力の不足を意味する。
機械加工業界は、旋盤、フライス盤、マシニングセンターなどの操作において、高度な技能を要する職種が多い。これらの技能は、長年の実践経験を通じて培われるものであり、特に日本の「匠の技」と呼ばれる精密加工技術は、若手への継承が課題となっている。厚生労働省の「労働力調査」(2023年)によると、製造業全体の就業者数は約1000万人だが、そのうち55歳以上の割合は約35%に達しており、2025年にはさらに増加すると予測される。一方、29歳以下の若年層は全体の約10%に過ぎず、技術継承の断絶リスクが高まっている。
労働力不足の科学的影響
労働力不足は、生産能力の低下、納期遅延、そしてコスト上昇を引き起こす。例えば、2023年の日本工作機械工業会(JMTBA)の報告書では、労働力不足が1%増加するごとに、工作機械の生産効率が約0.8%低下すると試算されている。この数値を2025年に適用すると、生産年齢人口の約15%減少が予想されるため、生産効率は単純計算で約12%低下する可能性がある。さらに、人材不足は品質管理にも影響を及ぼし、不良率の上昇(例:ISO 9001基準での不良品率0.1%から0.3%への増加)が懸念される。
デジタルトランスフォーメーション(DX)と「2025年の崖」
DXの推進とその障壁
経済産業省が2018年に発表した「DXレポート」では、日本企業がデジタルトランスフォーメーションを進めなければ、2025年以降に年間最大12兆円の経済損失が生じると警告した(いわゆる「2025年の崖」)。機械加工業界においてDXとは、IoT(モノのインターネット)、AI(人工知能)、ビッグデータを活用したスマート工場の実現を意味する。例えば、ファナック株式会社は、AIを搭載したCNC(コンピュータ数値制御)システムを開発し、加工精度の最適化やダウンタイムの削減を実現している。
しかし、多くの日本の中小企業(機械加工業界の約90%を占める)は、老朽化した基幹システム(レガシーシステム)を使用しており、DXへの移行が遅れている。2023年の情報処理推進機構(IPA)調査によれば、日本の中小製造業のうちDXに取り組んでいる企業は約45%に留まり、米国(72%)やドイツ(68%)に大きく後れを取っている。レガシーシステムのブラックボックス化(内部仕様が不明瞭で改修困難)や、IT人材不足が主な障壁である。特にIT人材は、2025年には約43万人が不足すると経済産業省が予測しており、機械加工業界でもデジタル技術を活用できる技術者の確保が急務となっている。
DXによる生産性向上の科学的根拠
DXの成功例として、ドイツの「インダストリー4.0」を挙げることができる。ドイツの工作機械メーカー、DMG MORIは、センサーとAIを活用した予知保全(故障予測)システムを導入し、稼働率を約20%向上させた。一方、日本のヤマザキマザックも同様の取り組みを進めており、2023年の実証実験では、IoT導入により生産リードタイムを15%短縮した。これらの事例から、DXが機械加工業界の生産性を向上させる科学的根拠は明らかである。しかし、日本全体での導入率が低いため、2025年には国際競争力の低下が懸念される。
グローバル競争環境と新興国の台頭
中国・韓国との競争激化
2025年時点で、中国は世界最大の工作機械生産国であり、2021年の生産額は約3兆5000億円(世界シェア約40%)に達している。中国企業(例:沈阳机床)は、低コストかつ中品質の製品で市場を席巻し、日本の得意とする高精度分野にも進出しつつある。また、韓国もサムスン電子や現代自動車の需要を背景に、工作機械の国産化を進めており、2023年の生産額は約5000億円(世界シェア約6%)である。
日本の機械加工業界は、高価格帯の高精度製品で差別化を図ってきたが、新興国の技術向上がこの優位性を脅かしている。例えば、中国の5軸加工機は、2020年代初頭には日本製と比較して約70%の精度しかなかったが、2025年には約90%に達すると予測される(国際機械学会データ)。この技術格差の縮小は、日本企業にとって価格競争への対応を迫る要因となる。
比較表:主要国の工作機械産業(2025年予測)
国名 | 生産額(億円) | 世界シェア(%) | 主力製品特性 | DX導入率(%) | 労働力人口(万人) | 高齢化率(%) |
---|---|---|---|---|---|---|
日本 | 1兆5000 | 12 | 高精度・高品質 | 50 | 6760 | 36.1 |
中国 | 4兆2000 | 45 | 低コスト・中品質 | 60 | 8億5000 | 15.0 |
ドイツ | 1兆8000 | 15 | 高精度・自動化 | 75 | 4200 | 23.5 |
韓国 | 6000 | 7 | 中精度・コスト効率 | 65 | 2800 | 18.2 |
米国 | 1兆2000 | 10 | カスタム・高付加価値 | 80 | 1億6000 | 17.8 |
注釈:
- 生産額とシェアは2023年IMTMAデータを基にした2025年予測。
- DX導入率はIPAおよび各国工業会の調査に基づく。
- 労働力人口と高齢化率は各国統計機関の2025年推計値。
環境規制とグリーン技術への対応
カーボンニュートラル政策
日本政府は、2050年までのカーボンニュートラル達成を掲げており、2025年はその中間目標に向けた重要な年となる。機械加工業界では、CO2排出量の多い切削加工や熱処理工程が見直され、エネルギー効率の高い設備への移行が求められている。例えば、経済産業省の「グリーン成長戦略」(2021年)では、製造業のエネルギー消費を2030年までに2013年比で30%削減する目標が設定されており、2025年はその進捗確認の節目となる。
科学的データに基づく影響
工作機械の稼働におけるエネルギー消費は、1台あたり年間約5000kWh(中小型マシニングセンターの場合)とされ、これがCO2排出量に換算すると約2.5トンに相当する(電力由来CO2排出係数0.5kg/kWhを使用)。仮に業界全体で100万台が稼働しているとすると、総排出量は250万トンとなり、削減目標達成には約75万トンの削減が必要である。これを実現するには、省エネルギー型工作機械(例:インバーター制御モーター搭載機)の導入が不可欠だが、2023年時点での導入率は約30%に留まる(JMTBA調査)。
結論と今後の展望
2025年の日本の機械加工業界は、労働力不足、DXの遅れ、グローバル競争の激化、環境規制という四重の課題に直面する。これらの要因は相互に関連し、業界全体の生産性、競争力、持続可能性に影響を及ぼす。科学的データに基づく予測では、対策を講じなければ生産能力が10~15%低下し、経済損失は年間数千億円規模に達する可能性がある。一方で、DXの加速やグリーン技術への投資が成功すれば、国際市場での地位を維持しつつ、新たな成長機会を創出できる。